Уважаемые клиенты, с 01.01.2024г. мы прекращаем принимать инструменты BOSCH в платный ремонт
Типы изделий:
|
Диагностика и анализ неисправностей:
ECOTERM давление насоса, производительность форсунки (таблица) Развернуть ▼
|
* DHD-201W - 0,31bar - 2,00 л/ч
* DHD-301W - 0,31bar - 2,80 л/ч
* DHD-20W - 0,32bar - 2,00 л/ч
* DHD-501W - 0,38bar - 4,70 л/ч
* DHD-200 - 0,30bar - 1,58 л/ч
* DHD-300 - 0,34bar - 2,13 л/ч
* DHD-500 - 0,40bar - 3,40 л/ч
* DHI-30W - 10,0bar - 2,28 л/ч (после замены 9,0 bar_1,9 л/ч)
* DHI-50W - 10,0bar - 4,70 л/ч
* DHI-520W - 9,5 bar - 3,00 л/ч
Примечание:________________________________________________________
* DHI-30W - в этой модели необходима замена форсунки вместо штатной (0,6gal_60град.) установить (0,5gal_80град.)
** МАРКИРОВКА ФОРСУНОК
___ Производительность форсунки может обозначаться в галлонах США (USgal)-(Рис.1_А) или кг/час.-(Рис.1_В). Иногда может присутствовать оба обозначения.
___ Угол распыления факела обозначается в градусах (Рис.1_С). Это может быть 60 либо 80 градусов (Рис.2). Открыть в новой вкладке
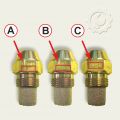 Рис.1 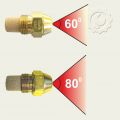 Рис.2
|
Редуктор, пробуксовка ( культиватор FM-1617MXL) Развернуть ▼
|
Такая неисправность как проскальзывание редуктора привода колес под нагрузкой объясняется износом или частичным повреждением зубчатой пары самого редуктора. В данном типе редукторов для передачи вращения используется коническая пара (Рис.1). Редуктор состоит из корпуса редуктора (Рис.2_1), ведущего вала (Рис.2_2) с конической шестерней (Рис.2_3). Ведомый вал (Рис.2_4) с коническим роликовым подшипником (Рис.2_5) входит в подшипник корпуса редуктора (Рис.2_6). На сам ведомый вал насажена коническая шестерня (Рис.2_7) и прижимная втулка (Рис.2_8). Весь этот механизм фиксируется крышкой редуктора (Рис.2_9) в которой находится внешняя обойма конического подшипника (Рис.2_5). Шестерня (Рис.2_7) при этом должна быть зафиксирована без осевого люфта. При этом должен соблюдаться температурный зазор между шестернями (Рис.2_7) и (Рис.2_3). Для обеспечения этого зазора используется регулировочная шайба (Рис.2_10), установленная на заводе. Часто случается так, что либо не выдержан необходимый зазор, либо присутствует осевой люфт шестерни (Рис.2_7). В обоих случаях появляется недопустимо большой зазор между шестернями (Рис.3), что неизменно приводит к повреждению зубчатой передачи (Рис.4). Наша задача состоит в том, что бы обеспечить правильный зазор путем подкладывания регулировочных шайб нужного размера. Увеличивая размер шайбы под шестерней (Рис.5_А) и уменьшая соответственно размер шайбы между шестерней и втулкой (Рис.5_В) мы уменьшаем зазор между шестернями. Устанавливая шайбы в обратном порядке (Рис.6) мы увеличиваем зазор между шестернями. Суть операции сводится к тому что бы ликвидировать осевое перемещение большой шестерни (Рис.2_7) и обеспечить необходимый зазор в зубчатой паре. В собранном редукторе, при вращении вала от руки, должен присутствовать небольшой люфт по оси вращения вала. Открыть в новой вкладке
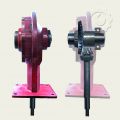 Рис.1 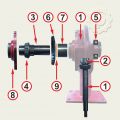 Рис.2 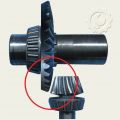 Рис.3 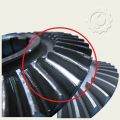 Рис.4 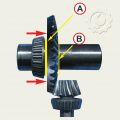 Рис.5 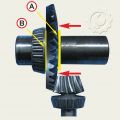 Рис.6
|
ЦПГ, абразивный износ (4-х тактный двигатель) Развернуть ▼
|
Абразивный износ поршневой группы происходит исключительно по причине попадания пыли в двигатель. Что бы этого не произошло установлен воздушный фильтр (Рис.1). Воздух, пройдя через фильтр, попадает в нижнюю часть корпуса фильтра и далее через карбюратор в камеру сгорания двигателя.
Узел воздушного фильтра (Рис.2) состоит из верхней крышки (Рис.2_А), фильтрующего элемента (Рис.2_В), нижней пластины крышки (Рис.2_С), уплотнительного кольца (Рис.2_D) и нижней части корпуса фильтра (Рис.2_Е). В нижней части корпуса фильтра (Рис.3) находится герметичная полость (синяя на рисунке) и имеет сообщение только с фильтрующим элементом и карбюратором. Эта полость образована двумя деталями, верхней и нижней и между собой плотно соединены. Были случаи когда это соединение было неплотным даже у новых устройств (Рис.4). Через эту щель воздух с абразивом попадает, минуя фильтр, прямо в двигатель. В результате грязь в карбюраторе (Рис.5) и появившиеся повреждения поршневой группы в виде задиров цилиндра и поршня и износ кулачка распредвала (Рис.6).
Устранить эту неисправность можно монтажным клеем, распределив его в углублении (Рис.7) в месте соединения двух половинок нижней части корпуса фильтра. Мы использовали монтажный клей типа "жидкие гвозди" (Рис.8).
Далее есть еще одно место, нуждающееся в хорошем уплотнении. Это примыкание фильтрующего элемента (Рис.2_В) к нижней части корпуса фильтра (Рис.2_Е). Между ними находится нижняя пластина крышки фильтра (Рис.2_С). Уплотнение обеспечивает резиновое кольцо (Рис.2_D). Все дело в том, что нижняя пластина не должна быть толще или равной по толщине с уплотнительным кольцом, иначе не возникнет плотного обжатия. По этому меняем тонкое резиновое кольцо на более подходящее толстое (Рис.9). Фильтрующий элемент (Рис.10_А) должен опираться на уплотнительное кольцо (Рис.10_В), но никак не на пластиковую пластину (Рис.10_С).
Отдельно стоит отметить, что необходимо убедиться в исправности прокладки карбюратора и плотной посадке газоотводящей трубки. Газоотводящая трубка соединена с корпусом фильтра и газ из двигателя возвращается обратно в двигатель через карбюратор, но минуя сам фильтрующий элемент. Открыть в новой вкладке
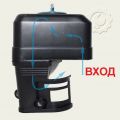 Рис.1 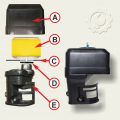 Рис.2 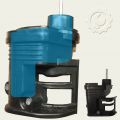 Рис.3 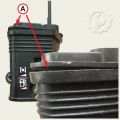 Рис.4 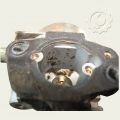 Рис.5 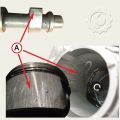 Рис.6 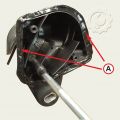 Рис.7 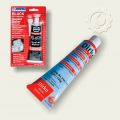 Рис.8 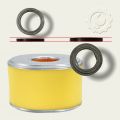 Рис.9 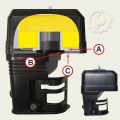 Рис.10
|
Подшипники аналоги (ГОСТ - международная система) Развернуть ▼
|
В последнее время мы привыкли к международной системе обозначений подшипников, но иногда встречаются обозначения по ГОСТу (отечественные подшипники). Здесь приведена таблица наиболее встречающихся в использовании у нас подшипников однорядных шариковых радиальных с обозначением по ГОСТу и их аналогов по международной маркировке. Нас интересуют в первую очередь сравнительные обозначения и основные размеры: наружный диаметр (Рис.1_D,Рис.4_D), внутренний диаметр (Рис.1_d,Рис.4_d) и высота подшипника (Рис.1_B,Рис.4_B).
Вначале оговоримся по маркировке ГОСТ. Подшипники могут быть открытыми, закрытыми с одной стороны и закрытыми с двух сторон защитной крышкой. Крышки могут быть металлические (Рис.1_А) и резинометаллические(Рис.2_А). Резинометаллические крышки лучше сохраняют подшипник то попадания грязи и пыли. Металлические крышки лучше переносят высокие обороты. Для примера возьмем подшипник 608(по международному стандарту), его аналог по ГОСТ (Рис.3). Последние 2 цифры (Рис.3_желтая зона) это основной тип подшипника 22-наружный диаметр_D, 8-внутренний диаметр_d, 7-высота подшипника_B. Под основной тип подшипника зарезервированы 4 последних знака. Пятая цифра сзади (Рис.3_красная зона)- количество защитных крышек, где 6-это одна крышка, 8-подшипник имеет крышки с обеих сторон. Перед 6-кой или 8-кой единица (Рис.3_зеленая зона) говорит о том, что крышки резинометаллические. Отсутствие знака - металлические. Как пример: 180018 (ГОСТ), подшипник типоразмера 22х8х7 защищен с двух сторон крышками из резинометаллического материала или 80018 (ГОСТ) подшипник 22х8х7 с двумя резинометаллическими крышками.
Обозначение защитных крышек по международному стандарту (ISO):
* отсутствие после цифр суффикса - открытый (608)
* Z-одна металлическая крышка (608-Z)
* 2Z-металлические крышки с двух сторон (608-2Z)
* RS- одна резинометаллическая крышка (608-RS)
* 2RS-резинометаллические крышки с двух сторон (608-2RS).
СРАВНИТЕЛЬНАЯ ТАБЛИЦА АНАЛОГОВ
ISO________ГОСТ________D-d-B________max об/мин
6000_______100________26-10-8__________30000
6001_______101________28-12-8__________32000
6002_______102________32-15-9__________28000
6003_______103________35-17-10_________24000
6004_______104________42-20-12_________20000
6005_______105________47-25-12_________18000
6008_______108________68-40-15_________12000
6009_______109________75-45-16_________11000
607_________17________19-7-6___________34000
608_________18________22-8-7___________32000
609_________19________24-9-7___________30000
61804____1000804______32-20-7__________22000
_6804____1000804______32-20-7__________22000
61806____1000806______42-30-7__________18000
_6806____1000806______42-30-7__________18000
6200_______200________30-10-9__________30000
6201_______201________32-12-10_________22000
6202_______202________35-15-11_________19000
6203_______203________40-17-12_________17000
6204_______204________47-20-14_________15000
6205_______205________52-25-15_________12000
6206_______206________62-30-16_________10000
625_________25_________16-5-5__________36000
626_________26_________19-6-6__________32000
627_________27_________22-7-7__________30000
628_________28_________24-8-8__________31000
629_________29_________26-9-8__________26000
6300_______300________35-10-11_________26000
6301_______301________37-12-12_________26000
6302_______302________42-15-13_________20000
6306_______306________72-30-19__________9000
6307_______307________80-35-21__________8500
6308_______308________90-40-23__________7500
6309_______309_______100-45-25__________8000
6900_____1000900______22-10-6__________36000
6902_____1000902______28-15-7__________28000
6905_____1000905______42-25-9__________18000
696______1000096_______15-6-5__________45000
697______1000097_______17-7-5__________43000
698______1000098_______19-8-6__________40000
30303_____7303_________47-17-15_________8500 Открыть в новой вкладке
|
Заклинивание редуктора (WORTEX_рейсмус) Развернуть ▼
|
Нередким явлением бывают случаи заклинивания цепной передачи в приводном механизме рейсмусного станка. Причиной неисправности являются забившиеся опилки в редуктор, которые препятствуют работе инструмента.
Добраться до редуктора несложно. В первую очередь следует ослабить 4 винта крепления верхней крышки (Рис.1). Винты откручиваются шестигранным ключом 5mm. Полностью снимать крышку не обязательно, достаточно ослабить винты крепления с тем, что бы верхняя часть не прижимала боковые крышки станка. Затем демонтируем левую боковую крышку устройства, которая крепится двумя винтами (Рис.2). Винты откручиваются крестообразной отверткой. Снимаем крышку (Рис.3). Под ней мы увидим пластиковый кожух (Рис.4_А). Крепится он двумя винтами внизу (Рис.5). Откручиваем шестигранным ключом 4mm.
Конструктивно пластиковый кожух выполнен в форме короба, который по мнению конструктора должен был защищать приводной механизм от попадания опилок (Рис.6). На практике получается обратный эффект. Опилки находят пути для попадания в редуктор и из-за защитного кожуха там аккумулируются, образуя плотную массу, препятствующую работе приводного механизма.
Сняв кожух мы доберемся до редуктора (Рис.7). Цепь и шестерни смазаны густой смазкой. Опилки, попадая в редуктор, налипают из-за смазки на узлы редуктора и образуют плотную массу (Рис.8). Наша задача очистить редуктор от опилок и смазать узлы смазкой типа Литол-24 (Рис.9).
В целях обслуживания также следует поступить и с правой крышкой, открыв приводной механизм с ремнем (Рис.10). Убедившись в чистоте механизма и целостности ремня (Рис.11), все узлы монтируем обратно.
Отдельно следует отметить один нюанс. При монтаже крышек рекомендуем не устанавливать пластиковый кожух (Рис.4_А). Если сравнивать модель WORTEX ТР-3117 с аналогичными устройствами других известных брендов (Makita, Hitachi, DeWALT), то у них дополнительные защитные кожуха отсутствуют. Опилки, попадая на узлы редуктора в процессе работы, свободно выпадают обратно под действием вращающихся узлов. Часть налипших опилок легко удаляется в процессе ежедневного обслуживания устройства по окончании работ. Открыть в новой вкладке
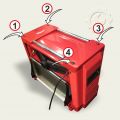 Рис.1 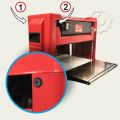 Рис.2 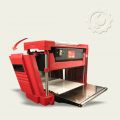 Рис.3 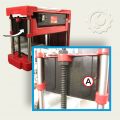 Рис.4 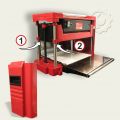 Рис.5 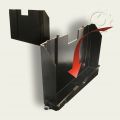 Рис.6 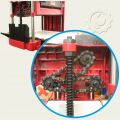 Рис.7 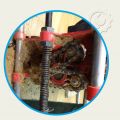 Рис.8 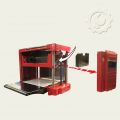 Рис.9 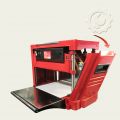 Рис.10 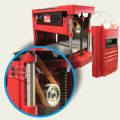 Рис.11
|
Карбюратор диагностика, ремонт Развернуть ▼
|
Статья касается карбюраторов для 2-ух тактных двигателей общего типа (Рис.1), без праймера, самовзвода и пр. дополнений.
Откручиваем винт (Рис.2_А). Сняв крышку, под ней видим прокладку (Рис.2_В) и мембрану клапанов (Рис.2_С). С другой стороны карбюратора откручиваем 4 винта и снимаем крышку (Рис.3_А). Под ней находятся дозирующая игла, жиклеры и мембрана управления иглой. Дозирующая игла приводится в действие целым механизмом, который состоит из коромысла (Рис.4_А), оси (Рис.4_В), самой иглы (Рис.4_С) и фиксирующего винта (Рис.4_D). Под коромыслом находится пружинка, которая через коромысло прижимает иглу к седлу, перекрывая топливный канал.
Открутив винт (Рис.4_D), демонтируем коромысло (Рис.5_А) с осью (Рис.5_В). Убеждаемся в свободном вращении коромысла на оси. При удержании рукой за ось, коромысло должно свободно под своим весом проворачиваться по оси и опускаться вниз.
Затем проверяем свободное перемещение иглы в канале. Взявшись за иглу пинцетом, отпускаем ее в канал (Рис.7). Она так же под своим весом должна беспрепятственно падать вниз. После этих проверок и обратного монтажа механизма дозирующей иглы проверяем уровень относительно коромысла и корпуса карбюратора (Рис.8). Коромысло не должно выступать или глубоко сидеть относительно краев ниши в корпусе. Т.е. быть почти вровень с краями.
В конце, с обратной стороны карбюратора, проверяем фильтрующую сетку (Рис.9). Она должна быть абсолютно чистой. Если устройство побыло в эксплуатации, то лучше ее заменить. Открыть в новой вкладке
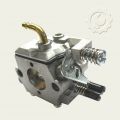 Рис.1 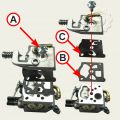 Рис.2 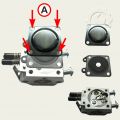 Рис.3 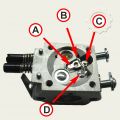 Рис.4 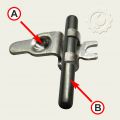 Рис.5 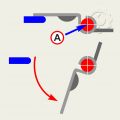 Рис.6 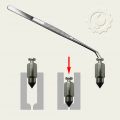 Рис.7 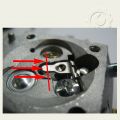 Рис.8 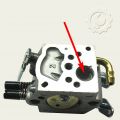 Рис.9
|
Кольца поршневые_завышен размер Развернуть ▼
|
Обнаружилось неприятное явление с ЦПГ для бензопил. Это касается поршневых групп диаметром 45мм. ЦПГ поставляются в сборе и кольца, которые лежат в комплекте, имеют завышенный размер и не входят в цилиндр. Тепловой зазор колец в замке должен быть в районе 0,3мм (Рис.1). Полученная партия ЦПГ, в некоторых случаях, имеет комплектные кольца, которые невозможно установить в цилиндр и становятся с нахлестом (Рис.2). При ремонте следует иметь ввиду этот факт и заранее проверять размерность колец, поместив их в цилиндр. Сделав это до монтажа поршня и цилиндра можно сэкономить кучу рабочего времени и нервов. Открыть в новой вкладке
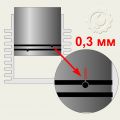 Рис.1 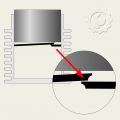 Рис.2
|
Повреждение зубчатой пары (Makita LS-1018) Развернуть ▼
|
Торцовочная пила Makita LS-1018 имеет своеобразную конструктивную особенность. Не редким обращением клиентов в СЦ связано с разрушением зубчатого соединения ротор-шестерня.
Вначале о конической передаче. При вращении под нагрузкой (Рис.1) на шестерни передачи действуют несколько сил, одна из которых направлена в противоположную сторону смыканию зубьев (Рис.1_В). В результате получается неполное зацепление зубьев, что неминуемо приводит к их повреждению (Рис.2).
В модели LS-1018, без закрепленной оснастки, шпиндель (Рис.3_А) вместе с шестерней (Рис.3_В) могут сместиться внутрь редуктора (Рис.3_С), тем самым провоцируя неполное зацепление зубьев передачи. Почему это происходит?
Данную модель пилы НЕЛЬЗЯ ВКЛЮЧАТЬ БЕЗ ОСНАСТКИ!!! У шпинделя с конической шестерней есть конструктивная возможность перемещаться в осевом направлении относительно внутренней обоймы подшипника (Рис.4_А). Внутренняя часть шпинделя вращается в подшипнике скольжения (бронзовая втулка). Там есть некоторый зазор по торцевой части. Под нагрузкой шестерня ротора отжимает коническую шестерню в сторону расцепления (Рис.4_В), провоцируя неполное зацепление зубьев с последующим их повреждением.
При установленной оснастке шпиндель с шестерней, через фланцы и диск (Рис.5_А) прижимается
винтом крепления (Рис.5_В) к подшипнику (Рис.5_С), тем самым предотвращая смещение его в сторону расцепления зубчатого соединения.
В противном случае имеется достаточно большой риск получить повреждение зубьев редуктора (Рис.6) Открыть в новой вкладке
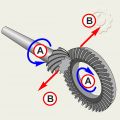 Рис.1 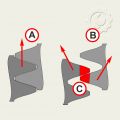 Рис.2 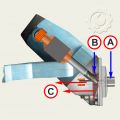 Рис.3 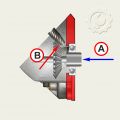 Рис.4 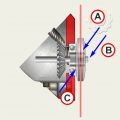 Рис.5 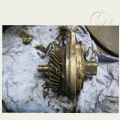 Рис.6
|
Протекает адаптер Развернуть ▼
|
Иногда появляются случаи с протеканием в районе адаптера в очистителях высокого давления у практически новых устройств. В частности это касается моделей ECO HPW-1770 и HPW-1860RSE. Замена адаптера на новый практически не помогает. Проблема в том, что подсоединенный к адаптеру шланг не до конца доходит до упора в адаптере. Шланг вроде как и зафиксировался, но неплотное соединение не позволяет обеспечить надежную герметизацию.
Есть вариант незначительной доработки. Достаточно просто подложить уплотнительное колечко в сам адаптор (Рис.1). На Рис.2 вид сверху и пунктирной линией показано где должно стоять кольцо. На Рис.3 вид в разрезе и место, куда укладывается кольцо.
Отдельно можно добавить, размер кольца внешний 20,7мм, внутренний 14,9мм, толщина 2,9мм. Идеально подходит от поршня перфоратора WORTEX RH-2629 (арт.AB26-41) или WORTEX CRH-1820 (арт.Z0A-ZP-20LI-26). Либо любое, подходящее по размеру. Открыть в новой вкладке
|
AV Engineering, конденсаторы в коробках управления Развернуть ▼
|
В скважинных насосах разных моделей AV Engineering используются фазосдвигающие конденсаторы, которые расположены в коробках управления. Номиналы их отличаются и зависят от того какой мощности используется двигатель. В самих коробках даны параметры двигателя и мощность указана в так называемых электрических лошадиных силах. В энергетике используется электрическая лошадиная сила равная 746 ватт. Ниже приведена таблица с переводом в более привычную систему измерения мощности в ваттах.
Слева внизу на картинках данные указанные на коробках. Справа внизу (красный цвет) перевод данных в ватты. И соответственно к каждому виду двигателя показаны номиналы конденсаторов. Открыть в новой вкладке
|
Заламывание поршневых колец Развернуть ▼
|
Обнаружились случаи заламывания поршневых колец. Это касается поршневых групп мотокос с диаметром цилиндра 40 мм. Причина неисправности в неточности изготовления поршней, а в частности нарушение посадочных размеров для замков поршневых колец. Как можно определить правильность размеров и вычислить заведомо неисправный поршень?
Для начала частично соберем поршень, поставим кольца и палец (стопорные кольца устанавливать не обязательно). Вставим поршень в цилиндр, выровняв по горизонтали, т.е. придадим ему рабочее положение (Рис.1). Во впускном окне будет хорошо видно неисправен поршень или нет (Рис.2). В неисправном поршне кольцо будет выпадать во впускное окно (Рис.3). На Рис.4 более укрупненный участок выпадения кольца.
На конкретном примере были проведены замеры неисправного поршня. С одной стороны замок был расположен относительно оси пальца на удалении 16,3 мм (Рис.5). С другой стороны расстояние между осью пальца и замка было 13,1 мм (Рис.6). Тот замок, у которого получилось большее удаление от оси пальца и выпадал во впускное окно. Впускное окно на Рис.5 и 6 обозначено красным цветом. При сравнении исправного поршня с неисправным заметно существенное смещение в положении замков (Рис.7).
Дополнительно усугубляет ситуацию фаска впускного окна со стороны стенок цилиндра. Само окно в ширину имеет размер в 23 мм, а края фаски 25 мм (Рис.8). Т.е. к тем неточностям в изготовлении поршней добавляется дополнительно по одному миллиметру на каждую сторону. В эту фаску и проваливается край кольца (Рис.9).
Такое явление можно рассмотреть на конкретном примере (Рис.10). Край кольца попадал в фаску, от чего стало образовываться затирание (показано красной стрелкой). На Рис.11 показан путь края кольца. По красной линии видно место заваливания кольца в фаску. На первом этапе работы двигателя заваливания может и не произойти. Но учитывая то, что место для замка поршневого кольца находится на грани фола, т.е. у самого края окна, все может закончится повреждением. Здесь хочется отметить еще один неприятный момент. Поршневое кольцо имеет некоторую осевую подвижность. Это обусловлено температурными требованиями, т.е. имеется необходимый температурный зазор, позволяющий кольцу перемещаться вдоль канавки. Добавим к этому небольшую выработку в процессе притирания ЦПГ, что несомненно увеличит эту подвижность (Рис.12). В результате получаем смещение кольца в сторону окна с возможным повреждением ЦПГ.
На Рис.13 показано такое перемещение по оси поршня. Для наглядности показано проворачивание поршня, кольца при этом находятся неподвижно. В действительности положение поршня ограничено шатуном, а кольца могут смещаться в пределах показанного люфта. На верхнем рисунке палец поршня параллелен цилиндру, на нижнем рисунке видно осевое проворачивание в пределах люфта по кольцам.
Бывают и другие случаи, когда кольцо попадает не во впускное окно, а в боковые, перепускные окна. Для начала следует обратить внимание на Рис.14. На нем видно как исполнен замок поршневых колец. Сам штифт замка, если смотреть на него в радиальном направлении, слишком глубоко посажен и в замковой части выступает лишь незначительная его часть. Выборка в поршневом кольце под штифт слишком большой и не соответствует диаметру самого штифта. Для лучшей наглядности на Рис.15 белой контурной линией показана эта проблема. В результате у поршневого кольца есть дополнительная степень свободы, позволяющая ему перемещаться в пределах канавки поршня, в конкретно взятом случае, на 2,3mm (Рис.16). По итогу видим такую картину (Рис.17).
Провели измерения, по итогу получили такие данные. Края между боковыми перепускными окнами расположены друг от друга на расстоянии 32mm (Рис.18_красные метки). Штифты по габаритным точкам имеют расстояние в 33mm (Рис.18_синие метки). Исходя из этих данных мы понимаем, что кольцо не будет обжато цилиндром по всему своему ходу. И как только попадет в зону перепускного окна, край его сразу зацепится за торцевую часть этого окна. Результат - обламывание кольца с повреждением ЦПГ (Рис.19). Открыть в новой вкладке
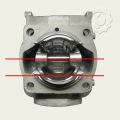 Рис.1 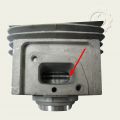 Рис.2 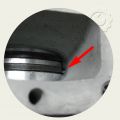 Рис.3 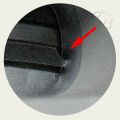 Рис.4 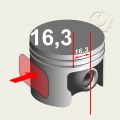 Рис.5 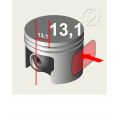 Рис.6 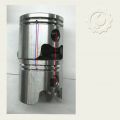 Рис.7  Рис.8 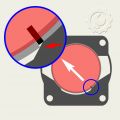 Рис.9 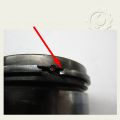 Рис.10 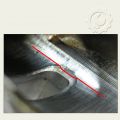 Рис.11 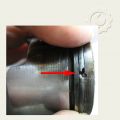 Рис.12 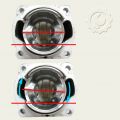 Рис.13 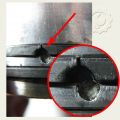 Рис.14 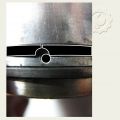 Рис.15 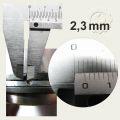 Рис.16  Рис.17 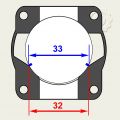 Рис.18 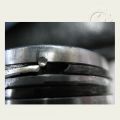 Рис.19
|
Прогар поршня Развернуть ▼
|
Иногда в ремонт потупают двигатели с прогоревшим поршнем. В чем может быть проблема? Есть две причины возникновения такого повреждения.
Бывают поршни прогоревшие по боковой стенке (Рис.1_А) и по днищу (Рис.1_В).
В первом случае причиной может быть некачественное масло в топливной смеси, слишком богатая смесь либо работа в режиме постоянной перегрузки двигателя. Т.е. причины, приводящие к закоксовыванию поршня с залеганием поршневых колец. В двигателях внутреннего сгорания предусмотрен температурный зазор поршня и поршневых колец. При работе двигателя поршень, переходя верхнюю мертвую точку, как бы переваливается в пределах теплового зазора(Рис.2). Образовавшийся зазор, компенсируют поршневые кольца, обеспечивая компрессию в камере сгорания (Рис.2_А). Если же кольца залегли, то в получившийся зазор прорывается газ от сгорания топливной смеси (Рис.3_А). В результате боковая стенка поршня получает мощный тепловой удар. Здесь сказывается большая скорость разогрева и слабое охлаждение поршня в этой зоне, т.к. находится со стороны выхода выхлопных газов. Повреждение поршня, как правило, имеет клиновидную форму (Рис.4_А). Края поврежденного участка имеет ярко выраженные следы оплавления.
Во втором случае это может быть детонация. В этом случае повреждения будут иметь вид механического повреждения и местом разрушения будет дно поршня (Рис.5). Т.е. по краям разлома будет видна кристаллическая структура металла без явных следов оплавления. Что такое детонация и чем она может быть вызвана?
Энциклопедическая формулировка: "Детонация — режим горения, при котором по веществу распространяется ударная волна, инициирующая химические реакции горения. Иногда формулируют как «сгорание во фронте ударной волны».
При нормальной работе двигателя скорость распространения фронта пламени в момент вспышки топлива обычно не более 50 м/сек. При детонации - скорость сгорания топлива происходит со сверхзвуковой скоростью и может превышать скорость звука в несколько раз (скорость звука 330 м/сек). При такой скорости горения появляется ударная волна с выделением большого количества тепла, что и приводит к разрушению поршня.
Основной причиной вызывающей детонацию является применение топлива с низкооктановым числом. Можно возразить, мол где сейчас можно найти низкооктановый бензин? Но тут есть нюанс. В основе любого бензина есть базовый бензин, который изначально получается после ректификации нефти. Он как правило имеет низкое октановое число и составляет около 65 ед. Есть и другие варианты с применением более современных технологий, но это все равно будет бензин с числом около 74-76 ед. Дальше вступают в процесс антидетонационные присадки. Эти присадки имеют свойство улетучиваться. Все зависит от условий хранения. Плюс к этому вы не можете знать насколько свежий бензин был на заправке. Более подробную информацию по этому вопросу можно найти в интернете. Можно только сказать следующее, при неблагоприятном стечении обстоятельств с условиями хранения можно через 3-4 недели получить низкооктановый бензин с выше сказанными неприятностями.
Похожие повреждения, такие как на Рис.5 могут случиться из-за калильного зажигания. Это и некачественный бензин с какими-нибудь особыми присадками и конечно свечи зажигания с неправильно подобранным калильным числом. На слишком "холодных" свечах может образовываться нагар, а слишком "горячие" могут способствовать калильному зажиганию. Т.е. вспышка топлива будет происходить раньше положенного времени, до выхода поршня в ВМТ.
Открыть в новой вкладке
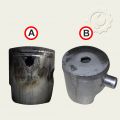 Рис.1 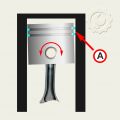 Рис.2 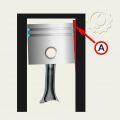 Рис.3 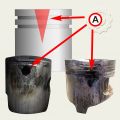 Рис.4 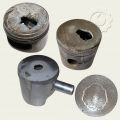 Рис.5
|
Подтекание масла (ASILAK__FERMER) Развернуть ▼
|
Причина частого обращения клиентов с жалобой на подтекание масла из корпуса редуктора в некоторых моделях культиваторов ASILAK и FERMER, является некачественная сварка узлов культиватора.
Редуктор культиватора ASILAK__FM-811MX несколько отличается от предыдущих моделей. Заливная пробка стала выше по уровню. Если в предыдущих моделях заливная пробка под масло располагалась в районе (Рис.1_А), то в FM-811MX она расположена значительно выше (Рис.1_В). Это позволяет пользователю заливать больше масла. В результате появляется возможность выброса масла в верхнюю часть кронштейна рукоятки. К кронштейну приварена пластина крепления механизма переключения передач (Рис.2).
Сварной шов этой пластины оставляет желать лучшего и часто из-под сварки выступают излишки масла, которые негативно влияют на реакцию пользователя. Сразу возникает вопрос об исправности культиватора.
Есть простой способ избавиться от подтеканий масла. Проблемную зону следует очистить от краски, обработать поверхность немного углубив место протекания (сверло, фреза, бормашинка) для лучшего сцепления герметизирующего состава. Затем "холодной сваркой" заделать обработанную поверхность (Рис.4). В конце доработки желательно восстановить покраску изделия (Рис.5). Открыть в новой вкладке
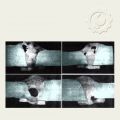 Рис.1 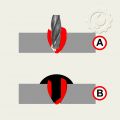 Рис.3  Рис.4 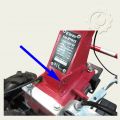 Рис.5 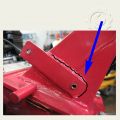 Рис.6 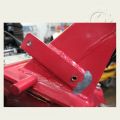 Рис.7 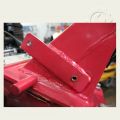 Рис.8
|
Заклинивание шатуна (ошибки при запуске) Развернуть ▼
|
При первом запуске компрессора надо понимать, что масла в большинстве моделей в картере нет. Об этом сигнализирует стикер, наклеенный на кнопку прессостата (Рис.1). Нередко на это некоторые не обращают внимание и ориентируются на окошко уровня масла. Об этом подробнее.
При большой разнообразности конструкций крышек картера (Рис.2) все они имеют схожее конструктивное решение по креплению смотрового окошка через резьбовой канал. Если смотреть на крышку картера изнутри (Рис.3), то можно заменить что этот канал имеет некоторую полость (показано красными стрелками) в которую попадает масло и там удерживается некоторое время. Это обусловлено коэффициентом поверхностного натяжения масла, что может ввести в заблуждение наблюдающего (Рис.4). Для проверки работоспособности устройства на заводе изготовителе заливается масло и после проверки сливается. Некоторое его количество остается в картере, это может быть где-то около 50 мл. Это скопившееся в окошке масло порой и вводит в заблуждение пользователя.
Иногда при продаже изделия продавец, ускоряя процесс продажи, не устанавливает колеса на компрессор. Если такой компрессор установить на ровную поверхность, то мы заметим большой уклон в сторону смотрового окошка (Рис.5) и уровень масла будет обманчивым (Рис.5_А).
Перед первым пуском необходимо соблюдать несложные правила. Установить колеса (Рис.6) или обеспечить нужный уровень, подложив под кронштейны колес какой-нибудь упор нужной высоты. Наклонить компрессор окошком вверх, с тем что бы слить остатки масла. Поставить обратно компрессор по уровню, убедиться по окошку в достаточном количестве масла (уровень должен находиться по середине окошка). При недостаточном количестве долить.
И напоследок о диагностике.
Случай при котором устройство пришло в ремонт с прихваченным шатуном и масло в картере присутствует в полном объеме. Порой бывает такое, что пользователь понял в чем его ошибка и желая скрыть истинную причину неисправности, постфактум доливает масло. Как определить подлог. Если заклинивание шатуна произошло с маслом (заводской дефект), то в нем будет присутствовать алюминиевая пыль и прочие продукты от трения. Алюминиевую пыль легко обнаружить подсветив масло фонариком или на ярком свету (будут заметны блестки). Если масло чистое, можно с большой долей вероятности утверждать, что оно не работало и залито было позднее. Открыть в новой вкладке
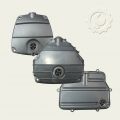 Рис.1 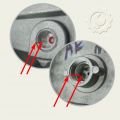 Рис.2 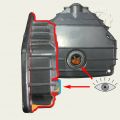 Рис.3 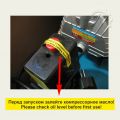 Рис.4 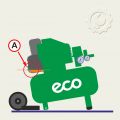 Рис.5 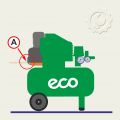 Рис.6
|
Заклинивание шатуна (ECO AE251-1, DGM AC-127) Развернуть ▼
|
В компрессорах довольно частой неисправностью является прихватывание шейки шатуна к коленвалу. Основная причина подобной поломки - это недостаток смазки. Это справедливо для всех типов компрессоров. Однако бывают исключения и в частности это касается моделей ECO AE251-1 и DGM AC-127. Здесь имеет место быть изначально неудачная сборка на заводе. Из практики ремонтов было определено, что установка шатуна в этих конкретных моделях требует соблюсти некоторые правила.
Шатун (Рис.1) имеет следующую конструкцию. В шатуне, в нижней его части, имеется подводящее отверстие для смазки. На Рис.2 показаны 2 проекции, (А) и (В). В проекции (А1) обычный вид, (А2) полупрозрачный для демонстрации подводящего канала. В нижней части шатуна (Рис.2_А2) виден канал отверстия. В проекции (В) показано направление канала. (В3)-обычный вид, (В4)-полупрозрачный, (В5)-в разрезе. Исходя из выше сказанного, шатун должен быть установлен на коленвал входным отверстием подводящего канала в сторону электродвигателя (Рис.3). В противном случае возможно масляное голодание шейки шатуна и как следствие его прихватывание к коленвалу. Это обусловлено конструктивным решением в изготовлении самого картера. По какой-то причине получается так, что при установке шатуна отверстием от двигателя масло не попадает в канал шатуна. Возможно это какая-то недоработка конструкции, но разговор сейчас не об этом. Наша задача минимизировать риск прихватывания шатуна к коленвалу и одно из решений оговорено выше.
Но это не отменяет общие причины поломки и при диагностике следует обращать внимание на наличие масла и на правильность установки шатуна. Как писалось в другой статье "Заклинивание шатуна компрессора (ошибки при первом пуске)"_
бывают случаи, когда из-за недостатка масла или его отсутствия происходит заклинивание. Пользователь, поняв свою ошибку, пытается скрыть ее, долив масло после произошедшего повреждения. Обнаружить подобную "хитрость" можно рассмотрев залитое масло и поверхность картера. Если масло имеет частицы алюминия и на поверхности картера имеются его остатки, то скорее всего задир произошел с залитым маслом. Если подсветить такое масло фонариком, то легко можно будет заметить блестящие частицы, плавающие внутри. Но тут следует обратить внимание на количество залитого масла, возможно его было мало. Если же масло чистое, то это может свидетельствовать о том, что клиент доливал масло после повреждения, что бы скрыть свою ошибку. Открыть в новой вкладке
|
Стартер ErgoStart принцип работы Развернуть ▼
|
Стартера с обычной системой и системой ErgoStart принципиально отличаются друг от друга не только конструктивным исполнением, но и приемом запуска двигателя. Очень часто в устройствах, где используется система ErgoStart, клиенты зачастую совершают одну и ту же ошибку, пытаясь применять приемы запуска как с обычными стартерами. Разберем подробнее.
ErgoStart - это запатентованная в 2003 году инновационная технология компании STIHL. Подобная технология значительно облегчает запуск двигателя и не требует от оператора необходимость дергать за ручку стартера. Как это работает? Между стартерной катушкой и коленчатым валом размещена пружина с двумя поводками (Рис.1_А), которая натягивается при плавном вытягивании тросика. В камере сгорания находится воздух, который сжимаясь на каком-то этапе препятствует проворачиванию коленвала. Пружина, сжимаясь, аккумулирует энергию пружины (Рис.2_А). Затем, в какой-то момент усилие пружины преодолевает сопротивление воздушной подушки в камере сгорания и вся энергия, накопленная пружиной, одномоментно передается на коленвал, запуская двигатель (Рис.3). Этим предотвращаются повышенные нагрузки, которые возникают при рывках. Пружина передает коленчатому валу энергию, конвертирует ее в движение, чем обеспечивает правильный безопасный запуск мотора. Оператору нужно всего лишь потянуть за тросик без резких рывков и больших усилий.
На Рис.4 показан сравнительный график запуска двигателя обычным стартером и стартером ErgoStart. График взят с официального сайта компании STIHL. Вертикальные столбцы - это количество тактов двигателя при вытягивании троса стартера. Как видно из графика при вытягивании троса с обычным стартером происходят рывки на каждом такте двигателя, что и передается на руку оператора, вынуждая его прилагать дополнительные усилия в виде резкого дергания на рукоятку стартера. С ErgoStart-ом это не происходит. Оператор плавно вытягивает трос и в какой-то момент происходит запуск двигателя.
Клиенту, который не знакомом с подобной конструкцией, следует объяснить что дергать за рукоятку стартера не только необязательно, но даже вредно для конструкции. Иногда по этой причине происходили поломки в виде повреждения пружины.
Открыть в новой вкладке
|
Доработка заглушки в садовых насосах Развернуть ▼
|
Корпуса насоса в насосных станциях и садовых насосах взаимозаменяемые. Отличие заключается в том, что в насосных станциях присутствует рессиверный баллон (Рис.1_А), а в садовых насосах его нет. В варианте с использованием корпуса в садовом насосе будет отсутствовать трубка соединяющая рессиверный баллон и корпус насоса (Рис.1_В). А отверстие необходимо будет заглушить пробкой с резьбой 1/2 дюйма (Рис.2). В заглушке есть уплотнительное кольцо (Рис.3). И все бы могло решиться просто, но есть небольшой нюанс.
Корпус изначально не был рассчитан на использование заглушки. Торцевая поверхность резьбовово отверстия, куда мы собираемся вкрутить заглушку, имеет корявую поверхность от литья, что не способствует хорошему прилеганию уплотнения и не имеет углубления под уплотнительное кольцо. В результате, после закручивания заглушки, уплотнение просто выползает из-под гайки наружу (Рис.4). Необходимо предусмотреть углубление ввиде фаски, что бы уплотнительное кольцо при закручивании оставалось в этом углублении.
Для операции по снятию фаски мы использовали конусное сверло (Рис.5). По итогу получилась вполне удовлетворительная фаска. Углубление фаски должно быть примерно на толщину уплотнительного кольца. При закручивании заглушки, кольцо внутри уплотниться и надежно перекроет выход давления наружу (Рис.6). Открыть в новой вкладке
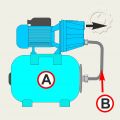 Рис.1 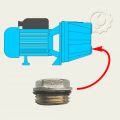 Рис.2 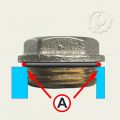 Рис.3 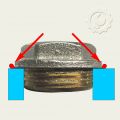 Рис.4 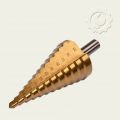 Рис.5 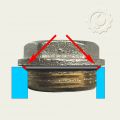 Рис.6
|
Задир ЦПГ, наиболее вероятные причины Развернуть ▼
|
Предварительная оценка повреждений - очень важный этап диагностики. Ошибочное предварительное мнение может сыграть ключевую роль в дальнейшей оценке причин неисправности. Механик может пойти по ложному пути рассуждений и в дальнейшем, подводя под свою первичную оценку, объяснять почему эти повреждения произошли, подтасовывая факты. Человек делает это не осознанно, просто в силу своих убеждений.
Перед нами двигатель с тепловым задиром ЦПГ. По характеру задира на поршне можно определить причины по которым произошло повреждение. Подача топлива и его сгорание происходит от впускного окна (Рис.1_А) до выпускного (Рис.1_В). Следовательно та часть поршня, которая находится к впускному окну всегда будет холоднее чем та, которое направлена к выпускному окну (Рис.2). Через впускное окно постоянно подается топливо, охлаждая эту часть поршня (Рис.2_А). После вспышки, отработанные горячие газы выбрасываются в выпускное окно, разогревая эту часть поршня (Рис.2_В).
Если двигатель перегревается и выходит за температурные расчетные нормы, то происходит локальный срыв масляной пленки и как результат задир. В случаях перегрева задир начинается с самой горячей точки - выпускное окно (почему, говорилось выше). Если вы увидели локальный задир со стороны глушителя (Рис.3), то однозначно это тепловой задир. Задир по перегреву можно получить двумя способами. Ограничить охлаждение двигателя и бедная смесь. На тему бедной смеси есть сопутствующая статья на сайте "Кратко о двухтактных двигателях" http://remont.tools.by/diagnostics/view/1551959975. Отсутствие охлаждения двигателя может быть в случаях когда ребра цилиндра покрыты теплоизолирующей грязью или как в случаях с бензорезами гудроном (при резке асфальта).
Если есть такой же локальный задир со стороны впускного окна (Рис.4) это может свидетельствовать о том, что работали с грязным воздушным фильтром или вовсе без него. Посторонние частицы через впускное окно попадали в камеру сгорания, по пути повреждая поршень на входе.
Если же задир по всей окружности поршня и поршень при этом не имеет замасляности (сухой), это отсутствие смазывающего материала в топливе. Здесь задир начинается со стороны выпуска (Рис.5) и почти сразу распространяется по всей поверхности (Рис.6) как только поршень начнет расширяться и выбирать тепловые зазоры.
Остальные случаи можно отнести к визуально понятным, Рис.7 - обламывание стопорного или поршневого кольца, разрушение сепаратора подшипника коленвала либо попадание постороннего предмета через впускное окно. Здесь надо смотреть по обстоятельствам и внимательно осмотреть картер на наличие осколков и идентификации их. На Рис.8 - разрушение подшипника и характерные вмятины от его шариков. Открыть в новой вкладке
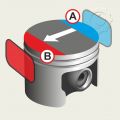 Рис.1 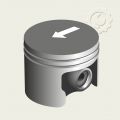 Рис.2 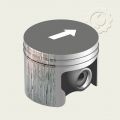 Рис.3 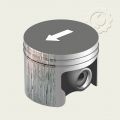 Рис.4 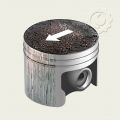 Рис.5 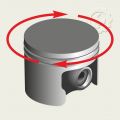 Рис.6 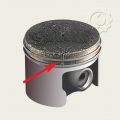 Рис.7 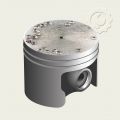 Рис.8
|
Некомплект GS-232 _ GS-282 Развернуть ▼
|
Обнаружены случаи некомплекта в бензопилах моделей GS-232 и GS-282. Отсутствует крепление воздушного фильтра.
В предыдущих моделях бензопил, таких как GS-231, GS-281 и пр., крепление воздушного фильтра осуществлялась внешней гайкой через прижатие крышкой фильтра (Рис.1_А). В моделях GS-232 и GS-282 крепление фильтра реализовано отдельным креплением ввиде барашкового винта и расположен он под крышкой фильтра (Рис.1_В).
Воздушный фильтр крепится барашковым винтом через шайбу (Рис.2). Вот их-то порой и нет в комплекте. Фильтр просто насажен на крепежную шпильку. Так же иногда отсутствует и прокладка между воздушным фильтром и корпусом (Рис.3). Барашковый винт с резьбой М5 и шайба в внутренним отверстием 5мм (Рис.4).
Возможно кому-то пригодятся размеры прокладки. В случае безвыходной ситуации, когда есть желание изготовить из подходящей резины. (Рис.5_А) размеры прокладки с указанием диаметров отверстий. (Рис.5_В) координатные размеры межосевых расстояний отверстий. Открыть в новой вкладке
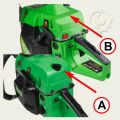 Рис.1 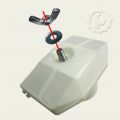 Рис.2 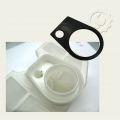 Рис.3 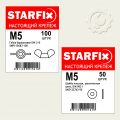 Рис.4 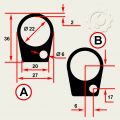 Рис.5
|
Демонтаж крыльчатки AV Engineering ENERGY-II-2700 Развернуть ▼
|
Возможно некоторые механики сталкивались с проблемой демонтажа крыльчатки. Если внимательно присмотреться, то будут заметны 2 резьбовых отверстия (Рис.1). Они-то и являются конструктивными элементами для демонтажа крыльчатки. Достаточно вкрутить два винта М4 и поочередно закручавая (Рис.2), стянуть крыльчатку. Винты должны быть длиной около 30-40мм. При вкручивании они упираются в корпус и повредить сальник не могут. Открыть в новой вкладке
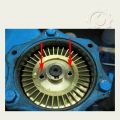 Рис.1 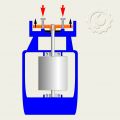 Рис.2
|
Углы заточки пильных цепей Развернуть ▼
|
Остро заточенная цепь обеспечивает эффективную, безопасную и точную работу цепной пилы. В этой статье речь об углах заточки.
Вначале о конструктивном исполнении режущего звена пильной цепи. Режущий зуб состоит из основания зуба (Рис.1_1), лопатки зуба (Рис.1_2), ограничителя глубины реза (Рис.1_3). Лопатка имеет вертикально расположенное торцевое лезвие (Рис.1_4) и спадающее подуглом назад верхнее лезвие (Рис.1_5), расположенное горизонтально.
В вертикальном направлении по срезу зуб (Рис.2_В) погружается на глубину до ограничителя (Рис.2_А). В горизонтальном направлении (Рис.3) дерево срезается боковой (вертикальной) частью зуба. Все режущие кромки должны иметь правильные углы заточки. От правильно заточенной цепи зависит не только точность выполняемой работы, но и значительно уменьшает нагрузку на двигатель.
Задний угол верхнего лезвия (наклон)(Рис.4). Спадающая под углом назад спинка зуба образует задний угол верхнего лезвия. Этот угол необходим для врезания верхнего лезвия в древесину и определен заводом изготовителем.
Задний угол торцевого лезвия (Рис.5). Суживающаяся назад лопатка зуба образует задний угол торцевого лезвия. Угол служит для бокового обрезания стружки и препятствует прихватыванию шины в дереве. Этот угол также остается неизменным и заточке не подлежит.
Передний угол (Рис.6). Кромка торцевого лезвия образует с поверхностью скольжения режущего зуба передний угол. В основной массе цепей этот угол составляет 85 градусов. Исключением являются специальные цепи - с победитовыми напайками (Rapid Duro) 65 градусов и для продольной распиловки 80 градусов.
Задний угол верхнего лезвия (скос)(Рис.7). Этот угол наиболее важен. Он должен быть, в зависимости от типа цепи, от 50 до 60 градусов, но специально его определять при заточке нет необходимости. При соблюдении остальных предписанных величин он должен получиться автоматически.
Угол заточки в плане (угол верхней кромки)(Рис.8). Угол заточки или угол в плане (вид сверху) получается измерением от верхней режущей кромки под прямым углом к направляющей шине цепи. В основной массе цепей этот угол составляет 30 градусов. Исключением являются цепи с победитовыми напайками (типа Rapid Duro) - 25 градусов и для продольной распиловки 10 градусов.
Расстояние ограничителя глубины (Рис.9). В большинстве используемых цепей этот размер равен 0,65 мм. Это цепи с шагом 1/4; 3/8; .325; Для цепей с шагом .404 требуется больший размер для ограничителя - 0,8 мм.
Кратко основные размеры:
* передний угол (Рис.6) - 85 градусов
* угол в плане (Рис.8) - 30 градусов
* ограничитель глубины (Рис.9) - 0,65 мм
Открыть в новой вкладке
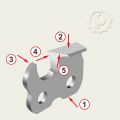 Рис.1 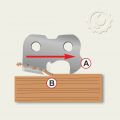 Рис.2 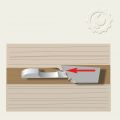 Рис.3 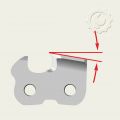 Рис.4 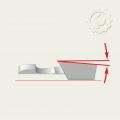 Рис.5 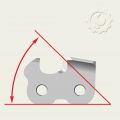 Рис.6 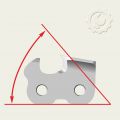 Рис.7 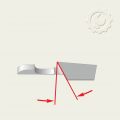 Рис.8 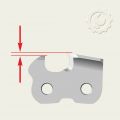 Рис.9
|
Травит воздух Развернуть ▼
|
Такая неисправность как травит воздух в районе прессостата (Рис.1_А) не всегда связана с неисправностью самого прессостата. Проблема может быть в обратном и разгрузочном плапанах. Как разобраться который из них некорректно работает?
На Рис.2 показаны магистрали, которые нас интересуют на данный момент. Красная магистраль (Рис.2_А) от поршневой группы к рессиверному баллону, синяя магистраль (Рис.2_С) связана с разгрузочным клапаном (в данном примере клапан расположен на прессостате), а черным (Рис.2_В) обозначена электрическая цепь управления работой электродвигателем.
В процессе работы компрессора (Рис.3), воздух от поршневой группы закачивается в рессиверный баллон. При этом разгрузочный клапан (Рис.4_А) должен быть закрыт, а обратный клапан (Рис.4_В) открыт.
Как только компрессор достигнет установленного максимального давления, прессостат подаст команду на отключение электродвигателя (Рис.5_А). Обратный клапан, при этом, закроется, препятствуя выходу воздуха из рессиверного баллона в поршневую группу. Одновременно с этим должен сработать разгрузочный клапан (Рис.5_В) для сброса лишнего давления в нагнетающей магистрали. Это предусмотренно для того, что бы поршневая группа не испытывала нагрузку при следующем запуске двигателя. При старте электродвигатель имеет слабый крутящий момент и его может не хватить для преодоления дополнительной нагрузки ввиде избыточного давления в магистрали.
Теперь о том как определить какой из двух клапанов ведет себя некорректно? Если при работающем компрессоре происходит стравливание воздуха, но при отключении стравливание прекращается, то проблема в разгрузочном клапане (Рис.6_А). Возможно он подклинил по какой-то причине. Если же стравливание продолжается и при отключениии компрессора, то проблема в обратном клапане (Рис.6_В). В этом случае воздух через неработающий обратный клапан поступает в магистраль и через разгрузочный клапан, который в данном случае должен быть открыт, выходит наружу.
Открыть в новой вкладке
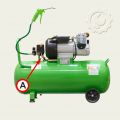 Рис.1 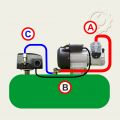 Рис.2 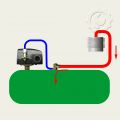 Рис.3  Рис.4 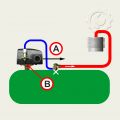 Рис.5 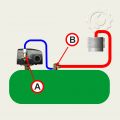 Рис.6
|
Не качает DGM BP-A111 Развернуть ▼
|
Столкнулись с такой проблемой как "не качает жидкость". Речь идет, пока, о модели насосов DGM BP-A111 (Рис.1).
Разгорор пойдет о шпонке, приводящей в движение крыльчатку (Рис.2). Если после диагностики установлено, что все узлы исправны, т.е. двигатель работает, поплавковый выключатель срабатывает, визуально вал вращается (снаружи мы видим только вращение ножа измельчителя), но жидкость при этом не перекачивается. Возможной причиной может быть смещение шпонки, стопорящей крыльчатку на валу двигателя.
На Рис.3 общая схема насосной части. Где (А) - вал двигателя с проточкой под шпонку, (В) - крыльчатка, (С) - пластина режущего механизма измельчения, (D) - нож измельчителя и (Е) - прижимная гайка. Как видно из рисунка, проточка под шпонку на валу сплошная и проходит почти через весь вал. И если в связке шпонка-вал имеется люфт, то у шпонки появляется возможность сместиться вниз, выпадая при этом из зацепления с крыльчаткой.
На Рис.4 зеленым цветом показана шпонка, находящаяся во втулке крыльчатки и красным, когда шпонка сместилась вниз и вышла из зацепления с крыльчаткой.
P.S. Были случаи, когда шпонка вовсе отсутствовала у новых изделий.
Данный случай относится к гарантийным. Открыть в новой вкладке
|
Притирание тормозной ленты (Вариант 1) Развернуть ▼
|
Притирание тормозной ленты о цепной барабан может происходить по двум причинам - это дефект крышки тормоза цепи и дефект самой тормозной ленты. Первая причина изложена в этой статье.
Неисправность, о которой пойдет речь, в последнее время приняло довольно массовый характер. У новых пил в большом количестве присутствует такой дефект как притирание тормозной ленты о цепной барабан. Причина - некачественное изготовление корпуса крышки тормоза цепи (Рис.1). Замена на новую крышку не помогает, на складе запчасти с таким же дефектом.
Притирание происходит по нижней части ленты (Рис.2). Если посмотреть внимательно на внутреннюю часть крышки, то заметим что уложеная тормозная лента в отпущенном состоянии не укладывается в окружность, а образует некоторый эллипс. Рис.3_А - фактическое положение ленты. Рис.3_В окружность, в которой теоретически должна находиться тормозная лента. В результате такого положения ленты, происходит ее притирание к цепному барабану (Рис.4_белая стрелка). Нижняя опора тормозной ленты, что является частью корпуса, не дает ленте лежать по окружности. Т.е. корпус выполнен с конструктивным дефектом геометрии.
Случай относится к гарантийным и изделие нуждается в замене, т.к. новые крышки имеют такой же дефект.
Негативные последствия такого притирания тормозной ленты о барабан на Рис.6. Начальная стадия оплавления (Рис.6_А), лента сдвинута для наглядности. Фатальное оплавление (Рис.6_В), тормозная лента снята.
P.S. Можно предложить вариант исправления дефекта путем удаления части корпуса (опорная нижняя часть под тормозную ленту) - Рис.5 Открыть в новой вкладке
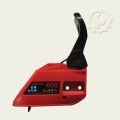 Рис.1 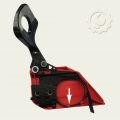 Рис.2 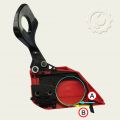 Рис.3  Рис.4 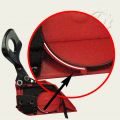 Рис.5 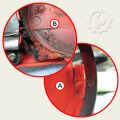 Рис.6
|
Притирание тормозной ленты (Вариант 2) Развернуть ▼
|
Второй вариант притирания тормозной цепи к цепному барабану отличается от предыдущего тем, что в данном случае неисправность касается не дефектного корпуса, а самой тормозной ленты.
В тормозную расстопоренную ленту должна вписываться окружность цепного барабана без какого-либо касания (Рис.1). В исправной крышке тормоза цепи лента лежит ровно и опирается на все ограничители корпуса крышки (Рис.2). Дефект можно обнаружить по опоре (Рис.3). На этом рисунке лента прилегает к опоре, что свидетельствует об исправном устройстве.
Если инструмент с дефектом, то лента, в этом месте, не будет прилегать (Рис.4). На Рис.5 показано в укрупненном плане, где хорошо заметен довольно большой зазор.
Причиной такой неисправности является плохая повторяемость при изготовлении тормозных лент. Как выяснилось, они имеют разную длину. При замерах лент (Рис.6) от точки (А) до точки (В) получались разные результаты.
Решить данную проблему можно заменив ленту на заведомо исправную. Открыть в новой вкладке
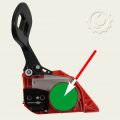 Рис.1 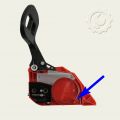 Рис.2 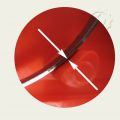 Рис.3 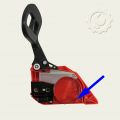 Рис.4 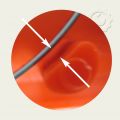 Рис.5 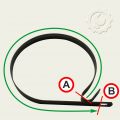 Рис.6
|
Схема электрическая ЕСО_ ОН-15, ОН-30, ОН50 Развернуть ▼
|
Электрическая схема теплогенераторов ЕСО моделей ОН-15, ОН-30, ОН-50.
На Рис.1 электронный модуль, на котором три подключаемых разъема. Обозначены как А1, А2 и А3.
Номера контактов начинаются от единицы, отмеченные цифрой (1). Счет идет порядно, не по кругу.
На Рис.2 наспиновка разъема (А1). Контакты (4) и (10) не задействованы. Снизу таблицы подписаны цвета проводов в оригинальном исполнении. На схеме провода раскрашены условно для простоты восприятия.
На Рис.3 приборы, подлючаемые к разъему (А2). Индикатор, подключенный к контактам (4), (5), представляет собой светодиод красного цвета и находится внутри теплогенератора. Обычно он примотан к жгуту.
На Рис.4 панель управления. В нижней части схемы его внешний вид и выходящие провода по цветам. Вверхней части схемы распиновка этих проводов в разъеме (А3). Открыть в новой вкладке
|
Сопротивление обмоток статора компрессоров (таблица) Развернуть ▼
|
Сводная таблица сопротивлений пусковой и рабочей обмоток статора и пусковых конденсаторов.
Сопротивления обмоток указаны с учетом сопротивления щупов тестера (0,4-0,5 Ом).
По мере поступления в ремонт новых моделей компрессоров таплица будет обновляться. Открыть в новой вкладке
|
Индикатор срабатывания момента затяжки (разрушение) Развернуть ▼
|
Динамометрический ключ как измерительный инструмент момента затяжки резьбовых соединений (Рис.1). Этот инструмент только так и следует рассматривать. Ни для каких срывов болтов и откручивания "укорчевшего" крепежа он не предназначен. Более того, такие операции зачастую могут привести к поломке инструмента. Один из таких случаев в этой статье.
Устройство такого ключа представлено на Рис.2. Из рисунка понятно как работает механизм срабатывания сигнала при достижении нужного крутящего момента. Вращающаяся по резьбе рукоятка, опирающаяся на цилиндр. Далее идет опорный подшипник, обеспечивающий плавное вращение рукоятки. Следом идут два калиброванных цилиндрика, которые опираются на пружину. После пружины расположен шарнирный механизм. Он и является индикатором предустановленного крутящего момента.
По достижении предустановленного значения (данные видны в окошке на ручке) раздается щелчок. Это сработал шарнирный механизм, говорящий о том, что значение достигнуто. Вращая рукоятку, мы сжимаем пружину, усиливая нагрузку на шарнирный механизм. Этим мы задаем нужное значение крутящего момента, которе хотим проверить.
Теперь о срабатывании механизма. На Рис.3 в верхней части, начальное состояние механизма. Часть (В), под действием пружины, через шарнирное соединение (синяя стрелка), прижимается к части (А). Часть (А) это часть ключа относящаяся к трещоточному механизму. Закручивая гайку, создается боковое усилие (красная стрелка). Обе части механизма начинают перемещаться между собой, показанный на схеме синей стрелкой, преодолевая специальный выступ. В какой-то момент проискодит соскакивание части (А) с этого выступа и механизм как бы "переламывается" (Рис.3_нижняя часть рисунка). При этом раздается щелчок (Рис.3_С), что говорит о том, что предустановленное значение достигнуто.
Если проигнорировать этот момент срабатывания индикатора, или намеренно, или не услышав и продолжить прилагать усилие на рычаг ключа, то этот механизм может быть поврежден. Особенно это касается ключей с большими моментами затяжек, т.к. рычаг этих ключей довольно внушительный. Длина рычага таких ключей порой бывает больше метра. Усилия одного человека вполне достаточно, чтобы сломать такой механизм.
Как правило ломается та часть, которая расположена со стороны трещотки (Рис.4_А). Красной линией показано наиболее вероятное место разрушения рычага. В низней части рисунка 4 показан момент после срабатывания механизма, т.е. после щелчка (Рис.4_В). При этом остается зазор между трубой ключа и рычагом механизма индикации (Рис.4_С). Иными словами есть куда "душить" ключ дальше и как результат... "легким" движением руки ключ превращается в неисправный инструмент (Рис.5).
Очень часто, при такой поломке, можно наблюдать дополнительные признаки превышения нагрузок. Это изгиб трубы самого ключа. На Рис.6 показано место, в котором обычно происходит такой изгиб (красная точка на нижней части рисунка). Проверить это можно, приложив уголок к этому месту. В этом месте обычно находится резиновая заглушка под наклейкой. Перед измерением надо аккуратно снять наклейку и вытащить заглушку, т.к. она будет мешать замеру. Затем приложив уголок (Рис.6_верхняя часть рисунка), попеременно нажимая по краям уголка (красные стрелки) мы сможем обнаружить "перекатывание" как на весах. Место, вокруг которого происходит перекатывание и будет местом изгиба трубы ключа.
Данный случай относится к негарантийным и расценивается как превышение допустимой нагрузки на инструмент.
Открыть в новой вкладке
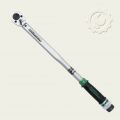 Рис.1 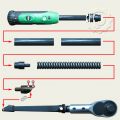 Рис.2 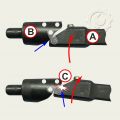 Рис.3 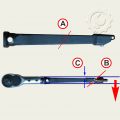 Рис.4 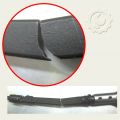 Рис.5 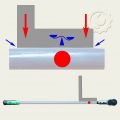 Рис.6
|
Электрическая схема (двигатель 4-х тактный) Развернуть ▼
|
Конструктивное решение электрической схемы в культиваторах практически одинаковые, но с одним небольшим нюансом. Есть решения, где от рукоятки управления отходит один провод (Рис.1), а есть с двумя (Рис.2). Разница заключается только в том, что в культиваторах с одним проводом закорачивание на корпус реализовано в самой рукоятке, а те которые с двумя проводами один из них закрепляется отдельно на корпус.
На Рис.3 приведена электрическая схема культиватора. Все узлы прописаны и ошибки в монтаже быть не должно. Стрелкой (А) показан провод закорачивания, который может выходить из рукоятки и закрепляться на корпус двигателя. Если провода нет, значит он соединен с корпусом двигателя внутри выключателя. Открыть в новой вкладке
|
Датчик масла, проверка работоспособности (культиваторы, мотопомпы) Развернуть ▼
|
Речь идет о малых 4-х тактных двигателях, используемых в малой сельхозтехнике. Культиваторах, бензогенераторах, мотопомпах и пр. (Рис.1). Прежде чем приступать к диагностике необходимо проверить уровень масла в картере двигателя. Масло должно быть залито по самую горловину. Иногда на двигателе имеется сервисная картинка на которой указан уровень заливки масла (Рис.2). В данной статье описывается ситуация когда двигатель либо не заводится, либо заводится и глохнет. Здесь описан способ как быстро определить неисправность.
Система, которая может влиять на выключение двигателя состоит из 3-х узлов. Это датчик масла (Рис.3,А), электронный блок (Рис.3,В) и выключатель (Рис.3,С). Отдельно по каждой детали.
Выключатель (Рис.4) нормально разомкнутый, при переключении в положение OFF замыкает искру от модуля зажигания на корпус двигателя.
Электронный модуль (Рис.5) так же обрывает искру, но в случае если появится хотя бы одно замыкание искры на корпус. Этот сигнал поступает от датчика масла. Т.е. электронный модуль работает как триггер. Это нужно для того, чтобы исключить неустойчивое, пограничное состояние, когда масла мало и датчик то замыкается на корпус, то опять возвращается в исходное состояние.
И наконец сам датчик масла (Рис.6). Его принцип работы несложно проследить по картинке (Рис7). В датчике реализованы две электрические цепи. Через болт крепления (Рис.7,1) образуется цепь, связанная с корпусом двигателя (оранжевая цепь). В поплавке (желтый) находится стержень, который через скользящий контакт соединен с проводом (красная цепь). При нормальном уровне масла цепи красная и оранжевая разомкнуты (Рис.7,А) - искра от модуля зажигания поступает на свечу. Если уровень масла ниже нормы цепи замыкаются (Рис.7,В). Стержень касается пластины и искра замыкается на корпус (двигатель глохнет).
Типовая схема Рис.8,1, где "С" выключатель, "В" электронный модуль, "А" датчик масла. Сразу исключаем из схемы выключатель просто отсоединив разъем. Мультиметром прозваниваем выключатель в положении ON, на корпус. Если прозванивается - неисправен выключатель. Также поступаем с датчиком масла. отсоединяем разъем и прозваниваем на корпус, если прозванивается - неисправен датчик масла, "завис" в нижнем положении, замкнувшись на корпус.
Если все нормально, двигаемся дальше. Возвращаем контакт выключателя на место и исключаем из схемы электронный блок (Рис.8,2). Отключаем электронный блок (Рис.8,В) и перебрасываем контакт на выход выключателя (красная линия). Запускаем двигатель. Если двигатель работает устойчиво, без перебоев - неисправен электронный блок. Если двигатель работает с перебоями и как бы "чихает" - неисправен датчик масла. Такая неисправность больше проявляется на "холодном" двигателе. В горячем масле поплавок датчика может работать вполне прилично, но стоит двигателю остыть, как датчик начинает "заедать" и неуверенно себя вести, периодически касаясь контактной пластины связанной с корпусом двигателя.
И в заключение. Обязательно выставить обороты двигателя. Особенно это касается мотопомп ECO серии WP. Часто на заводе обороты двигателя не проверяются и приходят с завышенными показателями, как результат повреждение ЦПГ, обрыв шатуна. Винт максимальных оборотов находится под корпусом фильтра (Рис.9, красная стрелка). Обороты должны быть 3600 об/мин. Винт холостого хода находится на самом карбюраторе (Рис.10, красная стрелка). Обороты холостого хода двигателя 1600 об/мин. Открыть в новой вкладке
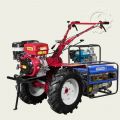 Рис.1 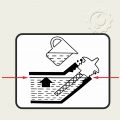 Рис.2 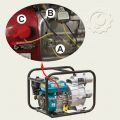 Рис.3 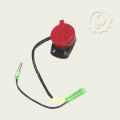 Рис.4 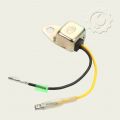 Рис.5 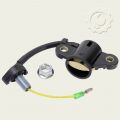 Рис.6 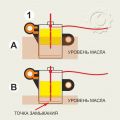 Рис.7 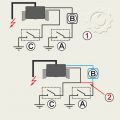 Рис.8 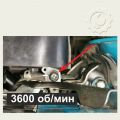 Рис.9 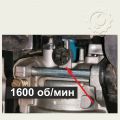 Рис.10
|
|
|
|