Уважаемые клиенты, с 01.01.2024г. мы прекращаем принимать инструменты BOSCH в платный ремонт
Типы изделий:
|
Диагностика и анализ неисправностей:
Реверс, не работает. Способ 1 (перфораторы WORTEX) Развернуть ▼
|
Были случаи когда в новых перфораторах WORTEX может плохо работать реверс. В реверсном режиме обороты двигателя должны быть ниже рабочих оборотов. Это связано с конструктивными особенностями, что справедливо практически для всех перфораторов. На кнопке выключателя (Рис.1_А) имеется выступ (Рис.1_В) который в свою очередь в режиме реверса опирается на выступ в корпусе выключателя, ограничивая обороты. На Рис.2 хорошо видно смыкание упоров, (Рис.2_А) - кнопка в отпущенном состоянии, (Рис.2_В) - кнопка в нажатом состоянии. Проблема заключается в том, что выступы имеют несколько завышенные размеры и не позволяют выключателю замкнуть контактные группы.
Из опыта нашего сервиса можем посоветовать укоротить выступ (Рис.3).
Для этого необходимо снять правую половину рукоятки и надфилем аккуратно спилить часть ограничителя (рис.4), периодически проверяя устройство на работоспособность и искрение.
Если удалить слишком много, то возникнет большое искрение, что и пытались предотвратить разработчики. Проверять желательно в резиновых перчатках аккуратно придерживая щеткодержатели от выпадения при вращении ротора (Рис.5).
Будьте предельно аккуратны - это может быть опасно! Открыть в новой вкладке
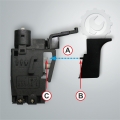 Рис.1 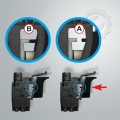 Рис.2 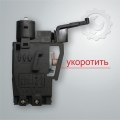 Рис.3 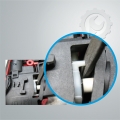 Рис.4 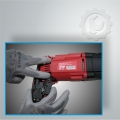 Рис.5
|
Подшипники, повреждения и их диагностика (часть 4) Развернуть ▼
|
Продолжение частей 1, 2, 3
ПЕРЕЧЕНЬ НЕИСПРАВНОСТЕЙ:
Часть 1
* Усталостные разрушения
* Выкрашивание поверхности
Часть 2
* Абразивный износ
* Атмосферная коррозия
* Фреттинг-коррозия
* Бринеллирование
* Ложное бринеллирование
* Повреждения электротоком
Часть 3
* Адгезивный износ
* Выбоины
* Повреждения при сборке
* Перегрев
Часть 4
* Несоосность колец
* Разрушение из-за дисбаланса
* Раскалывание
* Повреждение сепаратора
НЕСООСНОСТЬ КОЛЕЦ
Основной причиной повреждения подшипника, показанного на Рис.1 является несоосность колец, которая привела к фреттинг-коррозии и выкрашиванию металла. Несоосность ведет к высоким осевым нагрузкам, вызывающим усталостное разрушение и сильные сколы поверхности. Наружное и внутреннее кольца подшипника смещаются относительно друг друга по оси вращения (Рис.1_1), вызывая неравномерную нагрузку на направляющую дорожку (Рис.1_2).
РАЗРУШЕНИЕ ИЗ-ЗА ДИСБАЛАНСА
Характерные диагностические признаки дисбаланса это шум и высокий уровень радиальной вибрации. Повреждения будут иметь вид схожий с ложным бринеллированием, но поврежденные участки имеют менее упорядоченный вид и разбросаны более хаотично (Рис.2). Чаще такие повреждения появляются на внутреннем кольце подшипника.
РАСКАЛЫВАНИЕ
Раскалывание колец подшипника (Рис.2) это результат ударных и вибрационных нагрузок превышающих допустимые значения для данного типа подшипников. Подобное повреждение так же может быть вызвано неправильным монтажом подшипников, погрешностями формы и размеров посадочных поверхностей валов и корпусов.
ПОВРЕЖДЕНИЕ СЕПАРАТОРА
Повреждение сепаратора (Рис.4) проявляется в образовании в нем трещин с последующим его разрушением. Это в свою очередь ведет к быстрому выходу из строя всего подшипника, иногда затушевывая тот факт, что первопричиной разрушения был сепаратор. Чаще всего причиной выхода из строя сепаратора является его изгиб, возникающий при движении шариков по взаимно пересекающимся путям. Это может быть боковая нагрузка при высоких угловых скоростях, либо неправильная сборка или эксплуатация (несоосность посадки, несвоевременная смазка подшипника). Наиболее частым явлением подобного повреждения является грязь, попадающая вместе со смазкой на пути движения тела качения (Рис.4_1). Тело качения смещается в сторону (Рис.4_2), создавая боковую нагрузку на сепаратор.
ПОДВЕДЯ ИТОГ всего выше сказанного механик сам должен определить гарантийность или не гарантийность данного конкретного случая. Соблюдая все правила сборки и правильно применяя смазку, повреждения подшипников носят как правило гарантийный случай. Исключения составляют нарушения правил эксплуатации пользователем. Открыть в новой вкладке
|
Подшипники, повреждения и их диагностика (часть 3) Развернуть ▼
|
Продолжение частей 1, 2
ПЕРЕЧЕНЬ НЕИСПРАВНОСТЕЙ:
Часть 1
* Усталостные разрушения
* Выкрашивание поверхности
Часть 2
* Абразивный износ
* Атмосферная коррозия
* Фреттинг-коррозия
* Бринеллирование
* Ложное бринеллирование
* Повреждения электротоком
Часть 3
* Адгезивный износ
* Выбоины
* Повреждения при сборке
* Перегрев
Часть 4
* Несоосность колец
* Разрушение из-за дисбаланса
* Раскалывание
* Повреждение сепаратора
АДГЕЗИВНЫЙ ИЗНОС
Адгезия - сцепление поверхностей разнородных твёрдых и/или жидких тел. Адгезивный износ - перенос материала с одной поверхности на другую во время относительного движения благодаря процессу сварки в твердой фазе. Частицы, которые удалены с одной поверхности — временно или постоянно, присоединяются к другой поверхности. Если две недостаточно смазываемые поверхности скользят одна относительно другой под нагрузкой, то происходит перенос частиц металла с одной поверхности на другую. Это явление иногда называют задиром. Поверхности при этом явлении выглядят шероховатыми. При возникновении таких задиров материал подшипника нагревается до температуры, при которой происходит отпуск. Возникает местная концентрация напряжений, следствием которой является образование трещин и раковин.
ВЫБОИНЫ
Выбоины поверхности (Рис.2). Этот вид повреждения подшипников напоминает бринеллирование, т.к. выбоины скорей являются результатом пластических деформаций, чем износа. Тем не менее, они возникают при повреждении поверхности - это царапины, истирание мелкими посторонними частицами, которые являются результатом износа или попадают в подшипник при его работе. Тела качения при вращении захватывают посторонние частицы, попадающие в подшипник. Эти частицы, попав на дорожку качения оставляют случайные насечки, в районе которых возникает концентрация напряжений и разрывы масляной пленки, что приводи к усталостному выкрашиванию металла и появлению выбоин.
ПОВРЕЖДЕНИЯ ПРИ СБОРКЕ
Повреждение подшипника может произойти по причине неквалифицированной сборки. При посадке подшипника, из желания меньше повредить сам подшипник, механик с недостаточным опытом использует резиновую киянку. Этого делать ни в коем случае нельзя. Резиновая киянка, в силу своей эластичности, при ударе прогибается и повреждает пыльник подшипника (Рис.3_2) и (Рис.3_3). Результат такой "работы" поврежденный пыльник (Рис.3_1). При установке подшипника на вал необходимо использовать оправку опираясь на внутреннее кольцо подшипника (Рис.4_1). При установке внутрь посадочного места подшипника оправка должна опираться на внешнее кольцо подшипника и иметь трубчатую форму. Желательно иметь оправку с проточкой (Рис.4_синяя стрелка) для предотвращения ее соскальзывания и попадания по пыльнику. Если не соблюдать эти правила, то возможно появление такого повреждения как ложное бринеллирование (о чем говорилось во второй части). Подшипники должны устанавливаться по системе отверстий. Весьма важно соблюдать заданные посадки как для внутреннего кольца, так и для наружного. Подшипник внутренним кольцом насаживают на вал по глухой, тугой, напряженной или прессовой посадкам в системе отверстия, а на оси — по скользящей посадке или по посадке движения. Наружным кольцом подшипник устанавливают по напряженной или скользящей посадке в случае неподвижного корпуса и по глухой или тугой посадке —в случае вращающегося корпуса.
ПЕРЕГРЕВ
Перегрев подшипника можно определить визуально по цвету побежалости (Рис.5). Нормальной температурой в полости подшипника считается температура до 65⁰С. При температуре, не превышающей 65⁰С, реализуется максимальный эксплуатационный ресурс подшипника. Допускается, однако, перегрев подшипника до температуры 95⁰С. Но это уже критическая температура, при которой происходит повышенный износ рабочих деталей и изменяются свойства смазочного материала. Следствием изменения свойств смазки (масла) снова становится повышенный износ. Причины перегрева можно разделить на четыре группы.
* В первую группу условно можно отнести культуру производства. Подшипник установлен с перекосом, слишком тугой натяг или чрезмерно плотная посадка, использование недопустимой оснастки при монтаже.
* Вторая группа это перегрев как вторичный признак, вызванный повреждением подшипника (износ, ржавчина, задиры, всевозможные разрушения и пр.). Продукты износа попадают под тело качения и вызывают дополнительное сопротивление вызывая нагрев подшипника.
* Третья группа это неправильная смазка и ее количество. При недостатке смазки нагрев будет исходить от контактного трения, при большом количестве от избыточной нагрузки на преодоление сопротивления смазки. В случаях незащищенности подшипникового узла от внешней среды грязь может попадать в подшипник вместе со смазкой так же вызывая дополнительную нагрузку и как результат перегрев.
* И наконец четвертая группа это неправильно подобранный подшипник к предполагаемым условиям работы в данном узле. Если на высокоскоростной вал с вращением в 15000-20000 об/мин. установить подшипник с расчетными параметрами в 10000 об/мин., то это будет избыточной нагрузкой и вызывает быстрый перегрев подшипника. Открыть в новой вкладке
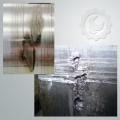 Рис.1 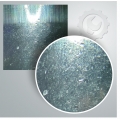 Рис.2 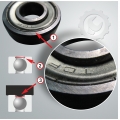 Рис.3 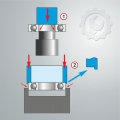 Рис.4 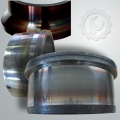 Рис.5
|
Подшипники, повреждения и их диагностика (часть 2) Развернуть ▼
|
Продолжение части 1
ПЕРЕЧЕНЬ НЕИСПРАВНОСТЕЙ:
Часть 1
* Усталостные разрушения
* Выкрашивание поверхности
Часть 2
* Абразивный износ
* Атмосферная коррозия
* Фреттинг-коррозия
* Бринеллирование
* Ложное бринеллирование
* Повреждения электротоком
Часть 3
* Адгезивный износ
* Выбоины
* Повреждения при сборке
* Перегрев
Часть 4
* Несоосность колец
* Разрушение из-за дисбаланса
* Раскалывание
* Повреждение сепаратора
АБРАЗИВНЫЙ ИЗНОС
Абразивное истирание металла разрушает поверхности элементов подшипника. Малые абразивные частицы, например продукты изнашивания металлов, проникающие в подшипник, приводят к повреждению дорожек качения, тел качения и сепаратора. Поверхность качения становится в большей или меньшей степени матовой, в зависимости от размера (зернистости) и типа абразивных частиц. Продукты износа латунных сепараторов могут окрасить светлую смазку в зелёный цвет. В зависимости от типа абразивного износа, поверхность приобретает или тусклый серый металлический цвет (Рис.1_3),(Рис.1_4) или же зеркально полируется (Рис.1_2). Иногда заметны мелкие царапины в виде небольших вмятин (Рис.1_1). По мере изнашивания дорожек качения и сепаратора количество абразивных частиц возрастает. Этот процесс распространяется всё шире, до тех пор, пока детали подшипника ни изнашиваются настолько, что он становится непригодным к работе. Все эти повреждения результат попадания абразивной пыли либо извне (плохое уплотнение), либо при неквалифицированной сборке. Поэтому при монтаже подшипника рекомендуется протирать каждый элемент чистой тканью перед смазкой и содержать в чистоте рабочие поверхности. Хорошие, промытые уплотнения и чистые смазочные материалы помогут избежать подобные негативные последствия.
АТМОСФЕРНАЯ КОРРОЗИЯ
Коррозия - это самопроизвольное разрушение металлов и сплавов в результате химического, электрохимического или физико-химического взаимодействия с окружающей средой. Влажный воздух, попадая внутрь подшипника, при охлаждении окружающей среды конденсируется, разрывая смазочную пленку в местах контакта тел и дорожек качения. В результате появляются очаги ржавчины (Рис.2), которые существенно сокращают срок службы подшипника. Атмосферную коррозию можно предотвратить, используя качественное уплотнение, эффективную пластичную смазку.
ФРЕТТИНГ-КОРРОЗИЯ
Фреттинг-коррозия очень похожа на обычную коррозию. Она возникает на посадочных поверхностях подшипника и на других сопрягаемых поверхностях. Эта коррозия вызывается незначительными (микроскопическими) нагрузками. Частицы, образующиеся в результате износа имеют черный цвет в присутствии воздуха и красные - в его отсутствие (Рис.3). Фреттинг-коррозия может вызвать как ослабление посадки внутреннего кольца на валу, так и его заклинивание, при котором подшипник невозможно будет снять. Сильно проявившаяся фреттинг-коррозия может привести даже к разрушению кольца. Предотвратить подобное негативное явление можно следуя рекомендациям производителя относительно допусков и убедившись, что элементы подогнаны наилучшим образом.
БРИНЕЛЛИРОВАНИЕ
Бринеллирование происходит от понятия "метод Бриннеля". Такие повреждения по внешнему виду напоминают вмятины, которые образуются на металле при проверке на твердость по методу Бринелля. При бринеллировании на поверхности колец появляются регулярно следующие друг за другом отпечатки, развивающиеся в заметные вмятины. Это является следствием пластических деформаций металла в местах контакта, которые возникают вследствие перенапряжения металла характерен для шарнирно‑рычажных механизмов, в которых звенья совершают колебательные (возвратно‑вращательные) движения. Результат бринеллирования дорожек качения показан на (Рис.4). Бринеллирование является следствием высоких статических или ударных нагрузок, неправильной технологии установки подшипника, сильных механических ударов, падения механизма, возникающих вибраций в поперечной нагрузкой на подшипник.
ЛОЖНОЕ БРИНЕЛЛИРОВАНИЕ
Ложное бринеллирование очень похоже на обычное бринеллирование. В отличие от «истинного» бринеллирования отпечатки характеризуются не только продавливаем металла в зонах пластических деформаций, но и его сдвигом (Рис.5). Иногда из-за сдвига места повреждения плохо заметны даже при внимательном осмотре. Ложное бринеллирование результат сильных вибраций или ударов механизма в нерабочем состоянии (транспортировка, вибрация от работающих рядом механизмов, ударные нагрузки при монтаже подшипника). Стрелками показано направление в котором двигались трущиеся части подшипника при вибрации или частых ударов.
ПОВРЕЖДЕНИЯ ЭЛЕКТРОТОКОМ
В результате прохождения через подшипник электрического тока может появиться точечный питтинг (сваривание). Такое повреждение часто имеет регулярный характер на поверхностях элементов качения и на дорожке качения (Рис.6_1). Наиболее распространенными причинами электро повреждений является статическое электричество, создаваемое ремнями транспортера и токами сварочных аппаратов. Поэтому транспортеры должны быть снабжены заземляющими лентами, а сварочное оборудование необходимо заземлять. Электрический ток может вызвать также и случайное локальное выкрашивание (Рис.6_2).
Открыть в новой вкладке
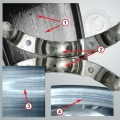 Рис.1 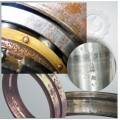 Рис.2 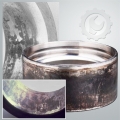 Рис.3 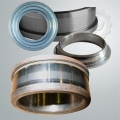 Рис.4 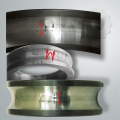 Рис.5 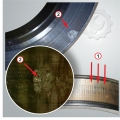 Рис.6
|
Подшипники, повреждения и их диагностика (часть 1) Развернуть ▼
|
Речь пойдет о подшипниках качения. Подшипники качения состоят из двух колец - наружного (Рис.1_1) и внутреннего (Рис.1_2), тел качения - шарики, ролики (Рис.1_3) и сепаратора (Рис.1_4), отделяющего тела качения друг от друга, удерживающего на равном расстоянии и направляющего их движение. По наружной поверхности внутреннего кольца и внутренней поверхности наружного кольца или на торцевых поверхностях колец упорных подшипников качения выполняют желоба — дорожки качения (Рис.1_5), по которым при работе подшипника катятся тела качения.
ИЗ-ЗА БОЛЬШОГО ОБЪЕМА ИНФОРМАЦИИ СТАТЬЯ РАЗБИТА НА 4 ЧАСТИ.
К основным видам повреждений подшипников можно отнести:
Часть 1
* Усталостные разрушения
* Выкрашивание поверхности
Часть 2
* Абразивный износ
* Атмосферная коррозия
* Фреттинг-коррозия
* Бринеллирование
* Ложное бринеллирование
* Повреждения электротоком
Часть 3
* Адгезивный износ
* Выбоины
* Повреждения при сборке
* Перегрев
Часть 4
* Несоосность колец
* Разрушение из-за дисбаланса
* Раскалывание
* Повреждение сепаратора
УСТАЛОСТНЫЕ ПОВРЕЖДЕНИЯ
Усталостное разрушение — явление, приводящее металл к разрушению после многократного изменения его напряженного состояния.Механизм усталостного разрушения во многом связан с неоднородностью реальной структуры материалов (ориентация соседних зёрен металла, наличие разных включений — шлаков, примесей; дефекты кристаллической решётки, дефекты поверхности материала — царапины, коррозия и т. д.) (Рис.2_1). Из-за неоднородности металла при переменных нагрузках на границах отдельных включений возникает концентрация напряжений, которая приводит к микропластичным деформациям сдвига некоторых зёрен металла (Рис.2_2). Далее происходит развитие сдвигов в микротрещине, их сращивание, на последнем этапе появляется одна или несколько макротрещин (Рис.2_3). По мере разрастания трещины поперечное сечение детали всё более ослабляется, и, наконец, происходит разрушение детали (Рис.2_4). При накоплении усталости в материале дорожки ее поверхность становится шероховатой (Рис.3), подшипник начинает шуметь и излишне нагреваться. Постоянная перегрузка, плохо обработанные и загрязненные поверхности неизбежно ведут к усталостным явлениям.
ВЫКРАШИВАНИЕ
Выкрашивание поверхности схоже с усталостью поверхности, но отличается от него более сильной степенью повреждения подшипника и может указывать на то, что подшипник исчерпал ресурс усталости (Рис.4). Появляются сколы и выбоины, которые хорошо заметны визуально.
Открыть в новой вкладке
|
Схемы электрические компрессоров (все ремонтируемые у нас модели) Развернуть ▼
|
Рис.1__двухцилиндровые, с центробежным выключателем
ECO
* АЕ-502
* АЕ-502-1
* АЕ-502-3
* AE-704-22
* АЕ-705-1
* АЕ-705-3
* AE-1005-B1
DGM
* АС-250
* АС-253
HDC
* HD-071
Рис.2__одноцилиндровые без предохранительного реле по току
DGM
* АС-125
* АС-126
* АС-127
* АС-153
ECO
* АЕ-251
Рис.3__двухцилиндровые и одноцилиндровые с предохранительным реле по току
DGM
* АС-254
* АС-502-22
* АС-702-22
ECO
* АЕ-251
* АЕ-251-1
* АЕ-251-2
* АЕ-251-3
* АЕ-251-4
* АЕ-501
* АЕ-501-1
* АЕ-501-2
* АЕ-501-3
Рис.4 и Рис.5 - компрессоры с трехфазными двигателями
Рис.4 - подключение двигателя по схеме "треугольник", Рис.5 - подключение двигателя по схеме "звезда".
ОБОЗНАЧЕНИЯ НА СХЕМАХ
* С - конденсатор (С1-рабочий, С2-пусковой)
* Р - контактная группа прессостата
* S - центробежный выключатель
* S1 - выключатель
* L1 - рабочая обмотка двигателя
* L2 - пусковая обмотка двигателя
* QA - токовое реле защиты
* Rt - температурное реле защиты (закреплена на обмотке статора)
* К - обмотка пускателя
* К1,К2,К3 - контактная группа пускателя
* RK - контактная группа токового реле защиты пускателя (интегрировано с пускателем)
* U,V,W - обмотки трехфазного двигателя, где 1-начало, а 2-конец обмотки
* U(C1),W(C2),V(C3) - трехфазная сеть
Синие кружки с обозначениями a,b,c точки замера сопротивлений обмоток статора. На Рис.1 (a,b) - сопротивление рабочей обмотки, (a,c) - пусковой обмотки. На Рис.2 и 3 замер производится двух обмоток одновременно в точках (a,b), т.к. нет возможности подключиться к средней точке обмоток (как результат - сумма двух обмоток). Замер сопротивлений трехфазного двигателя (Рис.4) в точках a,b,c,d,e,f. Концы всех обмоток выходят наружу и коммутируются по треугольной схеме на клеммной колодке. Подробная схема подключения в статье "Схема подключения прессостата (3-х фазные компрессоры)". Данные обмоток в статье "Сопротивление обмоток статора компрессоров (таблица)".
P.S. Сопротивление рабочей обмотки всегда будет меньше сопротивления пусковой обмотки. Открыть в новой вкладке
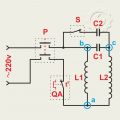 Рис.1 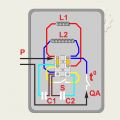 Рис.2 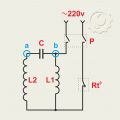 Рис.3 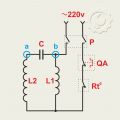 Рис.4 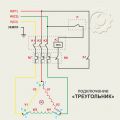 Рис.5 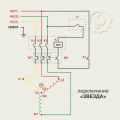 Рис.6
|
Схема подключения прессостата (3-х фазные компрессоры) Развернуть ▼
|
Компрессоры компании ЕСО с трех-фазными двигателями (Рис.1) подключаются по "треугольной" схеме, где начало одной обмотки соединяется с концом другой, замыкаясь между собой в треугольник (Рис.2). Если из двигателя выходит 6 проводов, то это значит что все концы обмоток выходят наружу и схемное переподключение осуществляется на клеммной колодке. Некоторые двигатели заранее подключены по какой-то схеме ("треугольник" или "звезда") внутри корпуса электромотора, то в этом случае из корпуса будет выходить только 3 провода. В нашем случае мы имеем дело с 6-тью проводами. Провода, выходящие из корпуса двигателя, промаркированы и имеют обозначения U1,U2,V1,V2,W1 и W2. Буквенные символы U,V и W - это обозначение обмоток, где цифра 1 начало обмотки, а 2 ее конец. Т.е. U1-начало обмотки U, а U2-конец обмотки U. Расключение колодки по "треугольной" схеме на (Рис.2). Это о переподключении обмоток электродвигателя. Сам двигатель запускается прессостатом (Рис.3). К контактам прессостата подключается трех-фазная сеть (Рис.3_С1,С2 и С3). Остальная группа контактов (3 шт.) подключается к клеммной колодке на которой выполнено подключение обмоток двигателя. Общая схема подключения на (Рис.4). На вход прессостата (Рис.4_Р) подключается 3-х фазная сеть (Рис.4_С1, С2, С3), выход подключается к колодке. Электродвигатель (Рис.4_М) имеет 3 обмотки и на схеме обозначены соответствующими символами. Как маркируются провода видно на (Рис.5).
Открыть в новой вкладке
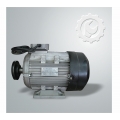 Рис.1 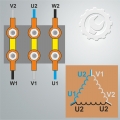 Рис.2 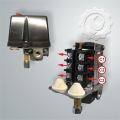 Рис.3 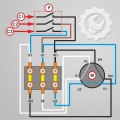 Рис.4 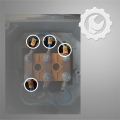 Рис.5
|
Схема подключения прессостата (1-фазные компрессоры, насосные станции) Развернуть ▼
|
Электрическая часть компрессоров состоит из прессостата (Рис.1), конденсаторов пускового (Рис.2_А) и рабочего (Рис.2_В), реле перегрузки по току (Рис.3) и самого электродвигателя у которого имеются две обмотки пусковая и рабочая. Сопротивление обмоток некоторых моделей компрессоров описаны в статье "Сопротивление обмоток статора (таблица)". Подключение прессостата на (Рис.4) где красный цвет это входная цепь сети, а синий выходная. На (Рис.5) принцип работы прессостата. Контактная группа замыкает входную (Рис.5_1,2) и выходную (Рис.5_3,4) цепи и управляется давлением (Рис.5_Р). Принципиальная схема (Рис.6) где сетевой вход (Рис.6_1), реле перегрузки по току (Рис.6_2), прессостат (Рис.6_3), центробежный выключатель (Рис.6_4), пусковой конденсатор (Рис.6_5), рабочий конденсатор (Рис.6_6), электродвигатель с рабочей (Рис.6_L1) и пусковой (Рис.6_L2) обмотками. Как дополнительная информация: пусковая обмотка электродвигателя всегда больше рабочей и имеет большее сопротивление, пусковой конденсатор большей емкости чем рабочий. О центробежном выключателе подробно описано в статье "Принцип работы центробежного выключателя в компрессорах". На (Рис.7) электрическая схема компрессора, где (GA) реле перегрузки по току, (S1) контактная группа прессостата, (S2) контакты центробежного выключателя, (С1) рабочий конденсатор, (С2) пусковой конденсатор, (L1) рабочая обмотка электродвигателя и (L2) пусковая.
В насосных станциях прессостат подключается аналогично, входная цепь от сети, выходная цепь на электродвигатель. Остальные узлы в насосных станциях отсутствуют (реле защиты по току, центробежный выключатель, пусковые обмотка и конденсатор). Открыть в новой вкладке
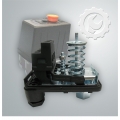 Рис.1 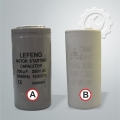 Рис.2 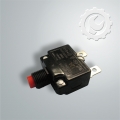 Рис.3 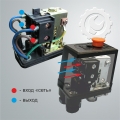 Рис.4 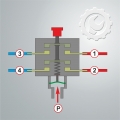 Рис.5 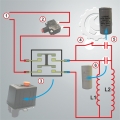 Рис.6 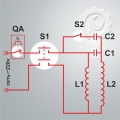 Рис.7
|
Взаимозаменяемость электродвигателей (пылесос NORMANN AVC-211) Развернуть ▼
|
В пылесосе NORMANN AVC-211 с 2018 года стали устанавливаться электродвигатели нового образца.
На Рис.1 электродвигатель устанавливавшийся до 2018 года. На Рис.2 двигатель нового образца, который стали устанавливать с 2018 года. Электродвигатель пылесоса (Рис.3_А) установлен на резиновый амортизатор (Рис.3_В), который прикрыт пластиковой крышкой (Рис.3_С). Резиновый амортизатор имеет два выступа, которыми вставлен в корпус двигателя (Рис.3_D) по направлению синих стрелок. Ответные отверстия в двигателях нового и старого исполнения имеют отличные друг от друга размеры. В старом исполнении они имеют межосевое расстояние 50 мм (Рис.4), в новом исполнении 57 мм (Рис.5). Поэтому при замене электродвигателя следует учитывать, что меняются обе детали вместе, электродвигатель и амортизатор. Открыть в новой вкладке
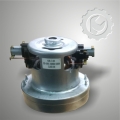 Рис.1 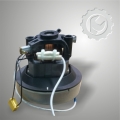 Рис.2 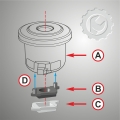 Рис.3 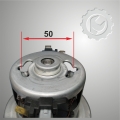 Рис.4 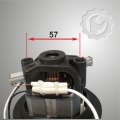 рис.5
|
Доработка корпуса фильтра (бензорез BIM GC 3540) Развернуть ▼
|
В бензорезах BIM модели GC-3540 обнаружена конструктивная недоработка. Основной воздушный фильтр не имеет плотного прилегания и не выполняет свои основные функции по фильтрации воздуха от пыли.
В нижней части корпуса фильтра присутствует кривизна (Рис.1), которая и не позволяет плотно прилегать фильтру. Объясняется это тем, что конструкция карбюратора не позволяет нижней части корпуса фильтра принять нормальное положение. Воздушный атмосферный канал карбюратора (Рис.2_А) упирается в корпус фильтра выгибая его. Эта кривизна так же не позволяет плотно прилегать к воздушному колену карбюратора (Рис.2_В). Из-за неплотного прилегания воздушного колена к корпусу фильтра между ними появляется щель (Рис.3_А) и пыль беспрепятственно, минуя фильтр через карбюратор попадает в поршневую группу. Учитывая условия работы бензореза через очень короткое время получается абразивный износ поршневой группы.
Суть доработки состоит в следующем. Вначале в нижней части корпуса фильтра проделываем отверстие (Рис.4). Можно воспользоваться сверлом или фрезой диаметром 6 мм. Затем необходимо изготовить резиновую прокладку по размерам указанным на рисунке (Рис.5). Резину можно использовать от камеры грузового автомобиля. Если нет подходящей по толщине резины можно использовать две прокладки меньшей толщины. Важно что бы общая толщина не превышала 3 мм. Прокладку приклеиваем на герметик к корпусу фильтра (Рис.6). Если посмотреть с обратной стороны, то должно получиться примерно как на Рис.7.
Теперь о сборке. На приклеенную прокладку (Рис.8_А) устанавливаем воздушный фильтр (Рис.8_В) и прижимаем крышкой (Рис.8_С). Здесь следует отметить, что при установленной крышке, до фиксации ее крепежными винтами, должен быть зазор между самой крышкой и нижней частью корпуса (Рис.9_А). Этот зазор должен быть не более 3-х миллиметров. В противном случае фиксируя крышку винтами (Рис.9_В) можно сильно прижать фильтр, что может вызвать его деформацию.
P.S. (обновление 10.04.2020) В настоящее время получены запчасти с измененным, улучшенным конструктивом. При их наличии отпадает необходимость доработки.
Артикулы и наименование узлов:
YD650.3-15201 верх корпуса GC 3540
YD650.3-15202 прокладка крышки верхн. корпуса GC 3540
YD650.3-16212_set фильтр возд. предв. (комплект) GC 3540
Открыть в новой вкладке
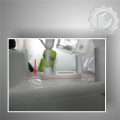 Рис.1 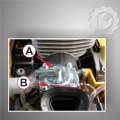 Рис.2 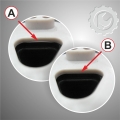 Рис.3 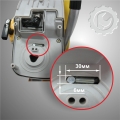 Рис.4 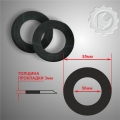 рис.5 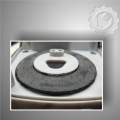 Рис.6 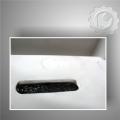 Рис.7 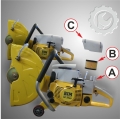 Рис.8 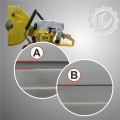 Рис.9
|
Повреждение крышки травосборника (газонокосилка LG-633/733) Развернуть ▼
|
Поломка задней крышки (возле оси крепления) закрывающей отверстие для выброса травы признаётся гарантийным случаем. Это относится к газонокосилкам с сравнительно небольшим сроком эксплуатации. Открыть в новой вкладке
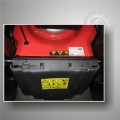 Рис.1 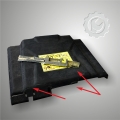 Рис.2
|
Износ зубчатой пары (SR 1590 E) Развернуть ▼
|
В данных моделях сабельных пил были обращения с претензией на то, что не работает режущая гарнитура. Причина в отсутствии зацепления зубчатой пары, ведомой шестерни и червяка ротора. Общий вид редуктора на Рис.1. Ведомая шестерня опирается на подшипник. Подшипник крепится к валу ведомой шестерни винтом с шайбой. Этим самым образуется жесткая связка подшипника с шестерней. При условии стабильной фиксации подшипника в корпусе, ведомая шестерня надежно зафиксирована в штатном положении и зазор зубчатого соединения обеспечивается. Фиксация подшипника обеспечивается стопорным кольцом, которое вставляется в проточку в корпусе редуктора (Рис.2). Проблема в том, что проточка имеет завышенные размеры (Рис.2_А) и позволяет при нагрузке перемещаться подшипнику по осевой линии (Рис.3_А).В этом случае зазор между зубьями шестерни и червяка ротора увеличится (Рис.3_В) и приведет либо к слабому зацеплению зубьев, либо к полному отсутствию сопряжения между собой. На Рис.4 показана проточка под стопорное кольцо. Решить эту проблему можно подложив регулировочную шайбу между стопорным кольцом и подшипником. Стопорное кольцо и размеры регулировочной шайбы на Рис.5. На Рис.6 результат работы где черным цветом обозначено стопорное кольцо, а синим шайба. На схемах (Рис.2,3,6) шестерня ротора смещена не в штатное положение для наглядности и лучшего понимания принципа доработки. Открыть в новой вкладке
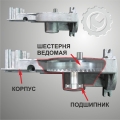 Рис.1 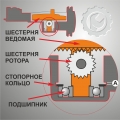 Рис.2 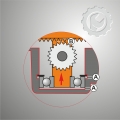 Рис.3 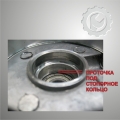 Рис.4 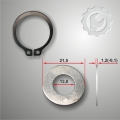 рис.5 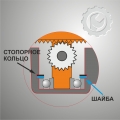 Рис.6
|
Резкий шум в редукторе (повреждение гайки ротора) Развернуть ▼
|
Причиной резкого шума в редукторе может быть касание большой шестерни о гайку ротора. Редуктор УШМ состоит из основных узлов (Рис.1). Гайка крепления малой конической шестерни на валу ротора конструктивно может быть исполнена как в обычном варианте (Рис.2_А), так и с проточенным скосом (Рис.2_В). Не путать видимый скос на гайке "А" (Рис.2) - это самоконтрящая система гайки против откручивания от вибрации. Чаще в УШМ применяются гайки со скосом (Рис.2_В), реже, если позволяет конструкция редуктора, гайка "А"(Рис.2). Гайка "А" устанавливается как обычно (Рис.3). Гайка "В" устанавливается скосом в сторону конической шестерни ротора (Рис.4). Так же задевание большой шестерни о гайку может появиться при выработке подшипников шпинделя или ротора. В этом случае появляется нежелательная подвижность узлов, которая приводит к нарушению зазоров между шестерней и гайкой. Так же нарушается зазор зубчатого соединения и как следствие быстрый износ зубчатой пары. Открыть в новой вкладке
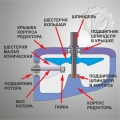 Рис.1 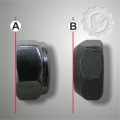 Рис.2 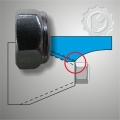 Рис.3 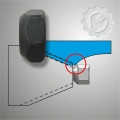 Рис.4 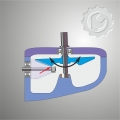 рис.5
|
Коробка передач, посторонний шум ( культиватор FM-1617MXL) Развернуть ▼
|
Шум в коробке передач в новом культиваторе. Наиболее вероятная причина такой неисправности - повышенный зазор (Рис.1) между ведущей шестерней вторичного вала (Рис.2_А) и конической ведомой шестерней (Рис.2_В). Такое состояние зубчатой пары приведет к повышенному износу шестерен и даже к сколу зубьев (Рис.3). Корпус механизма собран из двух корпусных деталей, корпуса коробки передач (Рис.2_1, оранжевый) и корпуса редуктора (Рис.2_2, красный). Шестерня вторичного вала (Рис.2_А) конструктивно связана с корпусом коробки передач (Рис.2_1), а коническая ведомая шестерня (Рис.2_В) с корпусом редуктора (Рис.2_2). Между ними стоит прокладка (Рис.4), иногда на заводе ставят две (Рис.5_С). Наша задача уменьшить зазор между шестернями. Сделать это можно убрав обе прокладки и заменив их на более тонкую. В этом случае корпус коробки передач, вместе с шестерней вторичного вала, сядет глубже (Рис.6) и зазор в зубчатой паре уменьшится.Если этого недостаточно, можно добавить шайбу под ведомую шестерню (Рис.7_С), (Рис.8). Этим самым мы поднимем шестерню, что так же уменьшит зазор зубчатой пары (Рис.9) Открыть в новой вкладке
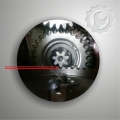 Рис.1 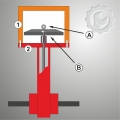 Рис.2 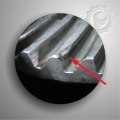 Рис.3 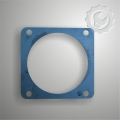 Рис.4 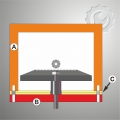 рис.5 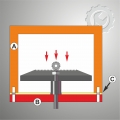 Рис.6 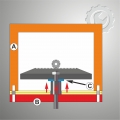 Рис.7 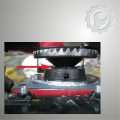 Рис.8 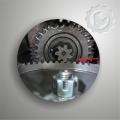 Рис.9
|
Регулировка зазора (погружной вибрационный насос) Развернуть ▼
|
Внутреннюю конструкцию насоса можно условно разделить на две части – механическую и электрическую. Главным компонентом электрической части является электромагнит, представляющий П-образный сердечник с магнитными свойствами. Он состоит из стальных пластин с одетыми электромагнитными катушками. Все элементы катушки залиты компаундом.
Устройство насоса показано на Рис.1. Механическую часть именуют вибратором, она состоит из штока, якоря и амортизатора. В основе якоря лежит электротехническая сталь, функцию амортизаторов выполняют резиновые шайбы. Муфта предназначена для изоляции камеры, где находится вода, от электрического сектора механизма.
Диафрагма внутри муфты оказывает на шток направляющее и фиксирующее действие. Вода из источника поступает через всасывающую в нагнетающую камеру, откуда впоследствии перемещается в трубопровод. Обратный клапан имеет форму гриба, он пропускает жидкость внутрь насоса и не дает ей вылиться обратно. После включения насоса в электросеть катушка создает магнитное поле. За счет действующих магнитных сил вибратор притягивается (Рис.2_А). Процесс способствует образованию во всасывающей камере разряженной атмосферы и снижению там давления. Через обратный клапан начинает поступать вода, заполняя всасывающую камеру. При следующем такте переменного тока магнитное поле исчезает, шток занимает исходную позицию. Поршень давит на воду во всасывающей камере, обратный клапан не выпускает ее наружу, поэтому она движется в нагнетающую камеру(Рис.2_В). При следующем такте цикл повторяется.
Зазор между сердечником катушки и якорем (Рис.3_А) регулируется шайбами (Рис.3_В). Суть регулировки сводится к следующему. Штатное количество шайб в наборе составляет около 3-3,5 мм. Но это не всегда является правильным. Из-за неповторяемости отдельных узлов изделия порой приходится изменять штатное количество шайб.
Специалисты завода изготовителя рекомендуют ориентироваться на звук работы насоса. При достаточном опыте можно легко определить 3 основных состояния работы насоса. Очень "мягкий" - это когда слышна вибрация, но нет соприкосновения якоря с сердечником катушки. Слишком "жесткий" - слышен резкий, очень громкий треск. И среднее состояние когда насос трещит в умеренном режиме. При "мягком" звуке зазор маленький (шайбы уменьшить). При "жестком" - зазор очень большой и необходимо добавить шайбы, этим самым уменьшив зазор. Открыть в новой вкладке
|
Дымит двигатель после 10-15 мин. работы (LG-733) Развернуть ▼
|
В некоторых газонокосилках, в частности ECO LG-733, наблюдалась такая картина. Двигатель запускается хорошо, прекрасно работает, но спустя минут 10-15 начинает дымить.
Для начала о схеме работы механизма очистки картерных газов. Под маховиком находится клапанный механизм (Рис.1). Там имеется отверстие связанное с полостью картера, которое перекрывается клапаном. Отсекающий фильтр (на Рис.1 показана полость для фильтра). На Рис.2_А канал отвода картерных газов, которые возвращаются через карбюратор обратно в камеру сгорания двигателя.
На Рис.3 упрощенная (для наглядности) схема работы такого механизма. Картерные газы вместе с парами масла попадают через канал (Рис.3_А) под клапан (Рис.3_В). Клапан (красный) подпружинен. При избыточном давлении открывается, пропуская картерные газы. Далее картерные газы вместе с парами масла попадают в фильтр-отделитель (Рис.3_С). Масло на нем абсорбируется и стекает вниз, собираясь в углублении и через отверстие возвращается обратно в картер (Рис.3_D). Очищенный от масла картерный газ проходит дальше (Рис.3_Е) и попадает в двигатель.
В случае если масло не стекает в картер (Рис.4_D), происходит переполнение полости фильтра и накопленное масло, перетекая через перегородку попадает в канал отвода газов (Рис.2_А Рис.4_Е). В результате картерные газы вместе с маслом попадают в камеру сгорания, вызывая горение масла с дымом. Причина простая. Отверстие которое нас интересует на Рис.5 или Рис.6 (со стороны внутренней части картера). Оно должно быть 2-2,5 мм (определено эмпирическим путем). На данных моделях (оговаривалось выше) отверстие около 1-1,5 мм, что явно мало для надежного удаления излишков масла. Больше 3 мм отверстие делать не стоит, т.к. возможно прорывание картерных газов уже мимо клапана и отсекающего фильтра. В этом случае эффективность их работы может заметно ухудшиться.
Теперь о клапане (Рис.7), отмечен красной стрелкой. Края клапанной пластинки имеют шероховатости (Рис.8_А). Их следует зашлифовать наждачной бумагой до приемлемого состояния (Рис.8_В). Это связано с тем, что при работе подпружиненная клапанная пластина может цепляться за края направляющего канала и зависнуть в открытом состоянии. Клапан способствует дополнительному удалению масла из полости механизма очистки картерных газов. В момент прохождения поршня в цикле сжатия в картере создается пониженное давление. Клапан закрывается и разрежением оттягивается масло через отверстие слива (Рис.3_D, Рис.5, Рис.6).
И наконец о маслоотделяющем фильтре. Конструктивно он выполнен избыточно плотным. Из-за плотной укладки масло не стекает, а накапливается внутри самого фильтра. Картерными газами масло срывается дальше по каналу и попадает в канал отвода. Исправляем это следующим образом. Фильтр разрезаем пополам (Рис.9_вверху) и укладываем следующим способом (Рис.9_красная стрелка). Сложенный фильтр освобождает сливное отверстие и не препятствуют сливу масла в картер. Открыть в новой вкладке
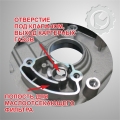 Рис.1 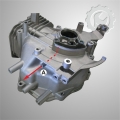 Рис.2 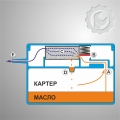 Рис.3 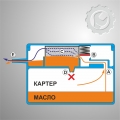 Рис.4 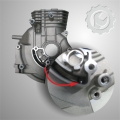 рис.5 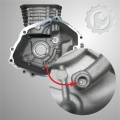 Рис.6 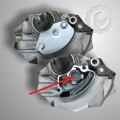 Рис.7 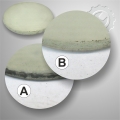 Рис.8 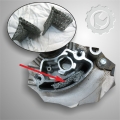 Рис.9
|
Демонтаж насосного механизма (краскораспылитель) Развернуть ▼
|
Порой очень сложно достать насосный механизм краскопульта из-за подсохшей краски или лака. Есть простой способ как с этим справиться. В комплекте краскораспылителя имеется дополнительная насадка (Рис.1). Раскручиваем, нам понадобится распылитель деталь "А" на Рис.1. Затем откручиваем рассеиватель от краскопульта (Рис.2) и вместо него вкручиваем распылитель "А", ранее снятый с дополнительной насадки. За этот распылитель вытаскиваем весь насос в сборе (Рис.3). Открыть в новой вкладке
|
Схемы типовые. Подключение коллекторных двигателей (диагностика) Развернуть ▼
|
Есть разные схемы подключения электродвигателей переменного тока коллекторного типа. Различия в том, что иногда добавляются всевозможные дополнительные узлы для лучшего комфорта пользователя. К ним относятся термопредохранители, тахогенераторы, датчики Холла, схемы плавного пуска, различные индикаторы и пр. Визуально это усложняет схему, но в основе все равно это можно представить как типовое подключение.
На Рис.1 подключение с одной обмоткой статора, т.е. обе обмотки статора внутри завязаны кольцом и на выходе два провода. На Рис.2 подключение в двумя обмотками и на выходе статора вы видим четыре провода. Понимая это, легко провести диагностику всех узлов двигателя, не прибегая к попеременной замене узлов наугад.
ПРИМЕР: Имеется УШМ с электроблоком плавного пуска.
НЕИСПРАВНОСТЬ: Не включается
1. Отсоединяем выключатель от схемы и прозваниваем (работает-не работает)
2. Отсоединяем эл/блок и подключаем двигатель напрямую по схеме (Рис.1, Рис.2) работает-не работает.
И уже по этим результатам можем сказать многое. И если все плохо - проверяем статор (сравниваем сопротивление обмоток) и ротор. В нашем случае это не КЗ (было бы заментно визуально), а скорее всего обрыв. Т.е. действуем методом исключения от простого к сложному. Это экономит и время, и качество ремонта, т.к. чем сложнее путь тем больше возможных ошибок. Открыть в новой вкладке
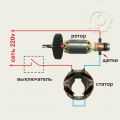 Рис.1 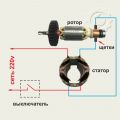 Рис.2
|
Срабатывание предохранительной муфты (перфоратор) Развернуть ▼
|
Заявление клиента на неисправность: «Срабатывает предохранительная муфта даже при незначительной нагрузке. Слышен характерный треск. Недавно куплена». Претензия на гарантийный ремонт.
Сразу оговоримся, это не гарантия и вот почему. Иногда перфоратор может заклинить в пробиваемом отверстии. Это состояние чревато поломкой насадки, самого перфоратора или нанесением травмы рабочему вследствие резкого рывка инструмента, возникающего при мгновенной остановке бура. Для этого перфораторы снабжены предохранительной муфтой, которая служит для остановки вращения патрона при заклинивании инструмента в отверстии. Это случай аварийный и нельзя рассматривать срабатывание муфты как трещотки в шуруповерте.
Частое срабатывание предохранительной муфты приводит к преждевременному износу узлов самого механизма. Поврежденные узлы (Рис.1) опорная шайба и шестерня предохранительной муфты. Хорошо заметны выработки на обоих узлах. Принцип работы муфты понятен из представленных схем (Рис.2,Рис.3,Рис.4).
Муфта в заблокированном положении(Рис.2). Это рабочий режим перфоратора. Муфта в состоянии срабатывания (Рис.3). Шарики выходят из зацепления и перескакивают в следующее гнездо, пытаясь восстановить блокировку муфты. На Рис.4 показан результат частого срабатывания муфты. Происходит выработка выступов между углублениями в шестерне, выработка на опорной шайбе и проседание пружинных шайб. Места износа узлов показаны красными зонами. Открыть в новой вкладке
|
Электродвигатель. Пробой изоляции обмотки статора (компрессор) Развернуть ▼
|
При диагностике обнаружен электрический пробой изоляции обмотки статора (см. фото).
Данная поломка вызвана наличием в этом месте нарушения изоляционного слоя проводов, что привело к межвитковому замыканию обмотки статора, а следовательно к выходу из строя электродвигателя. Повреждение носит локальный характер (см. фото 2).
Данная поломка является гарантийным случаем и устраняется безвозмездно для владельца. Открыть в новой вкладке
|
Перегорание дорожки на плате (TOPMIG-223) Развернуть ▼
|
Случаются перегорания на основной плате дорожек (Рис.1). Перегоревшая дорожка восстанавливается путем напайки. Причина неисправности в отсутствии надежной изоляции в рукоятке горелки (Рис.2). Оголенные провода (Рис.2,А) закорачиваются на корпус рукава. Обеспечив надежную изоляцию электропроводов (Рис.2,В) мы предотвратим повторное выгорание дорожек. Открыть в новой вкладке
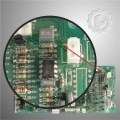 Рис.1 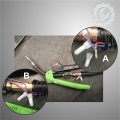 Рис.2
|
Повреждение оси крепления коромысла клапана (4-х тактный двигатель) Развернуть ▼
|
При диагностике двигателя культиватора обнаружено, что шпилька крепления коромысла обломана (см. фото).
Необходимо открутить часть шпильки и удалить все повреждённые детали. Установить новый, есть комплект деталей (см. фото). Отрегулировать клапана.
Данный вид поломки признается гарантийным , так как действия пользователя при эксплуатации не могли привести к поломке. Открыть в новой вкладке
|
Поломка оси шкива стартера (цепная пила) Развернуть ▼
|
При диагностике обнаружена поломка оси шкива стартера в месте соединения её с корпусом стартера (см. фото).
Данная поломка вызвана наличием в этом месте внутренней полости в результате чего произошло снижение прочности конструкции. Образование этой полости является дефектом возникшим при изготовлении данной детали.
Денная поломка является гарантийным случаем и устраняется безвозмездно для владельца. Открыть в новой вкладке
|
Абразивный износ поршня (2-х тактный двигатель) Развернуть ▼
|
При диагностике обнаружен износ поршня, особенно сильный со стороны впускного окна (см. фото).
Данное повреждение вызвано попаданием абразивных частиц во впускной тракт двигателя (отсутствовал воздушный фильтр тонкой очистки).
В данном случае требуется замена цилиндра и поршня, а также проверка состояния остальных деталей ЦПГ. Ремонт проводится за счёт владельца инструмента, так как неисправность носит эксплуатационный характер и не является гарантийным случаем. Открыть в новой вкладке
|
Нет подачи масла на цепь (CSP-150) Развернуть ▼
|
Иногда масляный шланг переламывается пополам из-за тонких стенок трубки (Рис.1). Можно применить способ доработки узла, поместив масляную трубку в пружинку подходящего диаметра, тем самым создав ей каркас (Рис.2). Открыть в новой вкладке
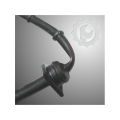 Рис.1  Рис.2
|
Сломана ось вращения колеса (газонокосилка) Развернуть ▼
|
При диагностике обнаружена поломка оси вращения колеса в месте её крепления к кронштейну (фото 1).
Данная неисправность является гарантийным случаем так как вызвана дефектом изготовления этого узла (частичный провар места соединения (фото 2)).
Неисправность устраняется путём сварки заново, либо путём замены этого узла. Открыть в новой вкладке
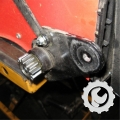 Рис.1 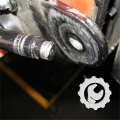 Рис.2
|
Подшипники вала привода колёс (газонокосилка) Развернуть ▼
|
При диагностике обнаружено отсутствие вращения подшипников вала привода задних колёс (фото 1). Вал вращается во внутренней обойме подшипников. Газонокосилка не имеет следов продолжительной эксплуатации и была куплена недавно (фото 2).
Данная неисправность является гарантийным случаем так как вызвана дефектом изготовления подшипников.
Неисправность устраняется путём замены подшипников. Открыть в новой вкладке
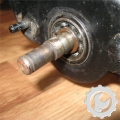 Рис.1 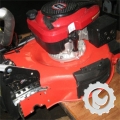 Рис.2
|
Отсутствует стопорный штифт (газонокосилка) Развернуть ▼
|
При диагностике обнаружено отсутствие стопорного штифта вала привода колёс внутри редуктора (фото 1; фото 2).
Данная неисправность является гарантийным случаем так как вызвана дефектом сборки редуктора.
Неисправность устраняется путём установки нового штифта. Открыть в новой вкладке
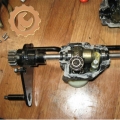 Рис.1 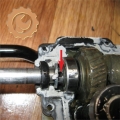 Рис.2
|
Распредвал, дефект кулачков (культиватор) Развернуть ▼
|
В культиваторе FERMER FM-1617MXL был обнаружен дефект кулачков распредвала (Рис.1). Следующие два рисунка (Рис.2) и (Рис.3) даны для сравнения. На Рис.2 кулачок нормального размера. На Рис.3 размер занижен почти на 4мм. В двигателе на холостых оборотах был слышен стук и на управление рычагом газа не реагировал. Открыть в новой вкладке
|
Проверка давления (насосные станции) Развернуть ▼
|
Для испытания насосной станции на давление необходимы емкость с водой (Рис.1), манометр на 10bar (1МПа или 1000кПа), запорный вентиль и шланги всасывания и слива воды. Шланг всасывания должен быть снабжен обратным клапаном для предотвращения опорожнения полости шланга. Обратный клапан (Рис.2) имеет примерно такой вид, фильтрующая сетка и сам механизм запирания. Принцип работы такого клапана на Рис.3. Клапан закрыт (Рис.3,А) и открыт (Рис.3,В). Проверка происходит следующим образом. Собираем испытательную модель как на Рис.1. Где всасывающий шланг с обратным клапаном (Рис.1,1), манометр (Рис.1,А), вентиль (Рис.1,В) и сливной шланг (Рис.1,2). Перед включением заполняем водой полость насоса через специальный болт-пробку. Включаем насосную станцию с открытым вентилем и ждем когда из сливного шланга польется вода. Если этого не происходит, выключаем станцию и опять заполняем полость насоса водой. Эту операцию возможно будет необходимо повторить несколько раз. Убедившись что вода уверенно циркулирует по кругу, закрываем вентиль и наблюдаем за показаниями манометра. По показаниям давления на манометре можем судить о примерном водяном столбе. Так при показаниях (например) 7bar, 0,7МПа либо 700кПа высота водяного столба будет составлять примерно 70м. Открыть в новой вкладке
|
|
|
|