Уважаемые клиенты, с 01.01.2024г. мы прекращаем принимать инструменты BOSCH в платный ремонт
Типы изделий:
|
Диагностика и анализ неисправностей:
Двигатель 2-х тактный, первичная диагностика ''на слух'' Развернуть ▼
|
По характеру работы двигателя можно предварительно определить проблему. Важно понимать как это работает.
~~ Запустили двигатель, холостые не держит или неустойчивы, на газу работает без проблем.
Вопрос к байпасу карбюратора. В более ранней статье "Карбюратор для любознательных. Для чего ''дырочки'' в диффузоре" описывалось смысловое значение жиклеров холостого хода. На холостом ходу именно они отвечают за работу двигателя. При засоренных каналах холостой ход может даже присутствовать, но при нажатии на газ начинают падать обороты и двигатель глохнет. Это происходит в тот момент когда дроссельная заслонка приоткрыта, начинает подаваться дополнительный воздух, а главный топливный жиклер еще не вступил в работу. На Рис.1_GIF показан такой момент (моргает красным). И если удалось проскочить провал (быстренько схватить ручку газа и нажать на нее), то в дальнейшем в работу вступает главный жиклер и производительность жиклеров холостого хода игнорируется (большая разница в топливоподаче).
~~ Двигатель запустили, холостой нормальный, на газу либо не набирает обороты, либо совсем глохнет - вариантов несколько.
1. забит топливный фильтр в баке (всасывающая головка), менять даже если внешне похож на чистый.
2. неисправность в главном топливном жиклере (Рис.2) или в забитых каналах обеспечивающих подачу топлива к жиклеру. Демонтировать его можно аккуратно выбив латунной выколоткой (Рис._3). Устройство жиклера понятно из Рис.4. Через сквозное боковое отверстие топливо подается в карбюратор через обратный клапан.
~~ У работающего двигателя на холостых плавают обороты, на газу так же наблюдается неравномерность оборотов. Наиболее вероятная причина негерметичность двигателя по любым узлам с уплотнениями.
1. Сальники коленвала. Если они старые (укорчевшие), поврежденные либо криво установленные будет происходить подсос воздуха и как следствие дополнительная (не предусмотренная) добавка воздуха к уже готовой топливной смеси.
2. Поврежденные прокладки между карбюратором, соединительным коленом, цилиндром.
3. Поврежденный топливный шланг.
~~ Двигатель после запуска работает около 10 мин., затем глохнет и не запускается. Возможная причина - неисправность системы вентиляции бака (сапун). Происходит следующее. При работе двигателя объем выработанного топлива должен замещаться таким же объемом воздуха, который поступает в бак через сапун. Если он не работает, к примеру забит мусором, то в баке будет создаваться разрежение, которое будет препятствовать поступлению топлива в карбюратор. Принцип проверки прост. Как только двигатель заглохнет нужно открутить крышку топливного бака. Если будет слышно легкое шипение воздуха, значит в баке пониженное давление и дело определенно в сапуне. Поможет чистка или замена. Сам клапан может быть установлен как отдельно, так и интегрирован в пробку топливного бака.
Пробка с встроенным клапаном, ее устройство и принцип работы.
На Рис.5 детали пробки. (А)- сама пробка, (В)- уплотнительная прокладка, (С)- корпус сапуна, (D)- сапун, (Е)- ограничитель от выпадения пробки. В данном случае нас интересует сам клапан-сапун (Рис.6). Выполнен он по примеру ниппеля (стрелкой показаны сомкнутые половинки проходного канала). Демонтаж заключается в снятии плоским предметом, типа отвертки, ограничителя (Рис.5_Е).
На Рис.7 красной стрелкой показан путь воздуха в бак.
Еще очень много может сказать о работе двигателя свеча зажигания. Подробно об этом в статье "Кратко о свечах зажигания" http://remont.tools.by/diagnostics/view/1551960047.
Ну и конечно настройка карбюратора (при условии исправности всех перечисленных выше узлов). Статьи "Карбюратор настройка" http://remont.tools.by/diagnostics/view/1583157826, "Карбюратор настройка - нюансы" http://remont.tools.by/diagnostics/view/1583412753. Открыть в новой вкладке
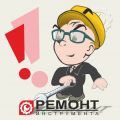 Лого 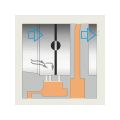 Рис. 1_GIF 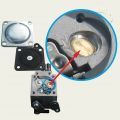 Рис. 2 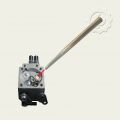 Рис. 3 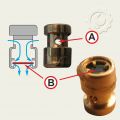 Рис. 4 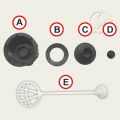 Рис. 5 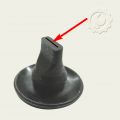 Рис. 6 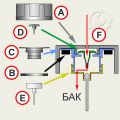 Рис. 7
|
Залегание колец Развернуть ▼
|
Залегание колец, как один из опасных повреждений двигателя. Из-за чего происходит и чем это опасно?
Основные причины образования нагара это неподходящее масло, добавляемое к топливной смеси и работа двигателя на пониженных оборотах (Рис.1).
В первом случае масло не соответствует температурному режиму и просто пригорает, накапливаясь в камере сгорания и в кольцевых углублениях в поршне (Рис.2).
На Рис.3 показан процесс залегания кольца. Красными зонами показаны места образования нагара (Рис.3_А). При разогретом двигателе поршень расширяясь, прижимается к стенкам цилиндра. Кольца при этом утапливаются в поршневые углубления (Рис.3_В). Охлаждаясь, поршень сжимается и кольца должны выйти из углублений. Но при достаточно сильной закоксованности, нагар не позволяет это сделать и кольца остаются зажатыми внутри поршневых углублений (Рис.3_С). Получилось залегание колец. При попытке дальнейшей работы, избыточная часть нагара отрывается и попадает между поршнем и стенками цилиндра с образованием последующих задиров.
Во втором случае (низкие обороты двигателя) происходит неполное сгорание топливной смеси. В результате масло, как медленнее испаряемая часть топливной смеси, в избыточном количестве прогорает в камере сгорания. Не происходит самоочищения зоны горения. Накапливается нагар с закоксовыванием. А дальше происходит тоже, о чем говорилось выше.
Дополнительно следует отметить следующее. Нагар может накапливаться до определенного момента, не вызывая залегания колец. И при избыточном его количестве, отрывается и попадает между стенками поршня и цилиндра в районе перепускных окон. По своему составу нагар имеет очень твердую структуру схожую со стеклом. Такие частицы становятся причиной сильных задиров с частичным смещением кромок поршня и блокируя кольца (Рис.4).
Случай не является гарантийным и относится к эксплуатационным повреждениям. Открыть в новой вкладке
|
BULL SC-1804 _ крышка и корпус не подходят по посадочным размерам Развернуть ▼
|
В модели гайковерта BULL SC-1804 появилась нестыковка с заменой некоторых запчастей. В частности это касается корпуса (Рис.1_А) и крышки редуктора (Рис.1_В).
В штатных изделиях посадочные места между собой 54мм. Полученные запчасти имеют меньший посадочный размер и он равен 53мм. В результате при замене одного из этих узлов получится нестыковка. На Рис.2 слева крышка редуктора установленного на заводе, справа полученная запчасть. В комплекте с корпусами на 53мм были получены и крышки, которые также имеют посадочный размер 53мм.
По этому при необходимости замены одного из этих узлов следует менять их в комплекте крышка-корпус. Открыть в новой вкладке
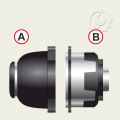 Рис 1 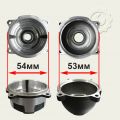 Рис. 2
|
Масляный привод и насос, замена (ECO_CSP-165) Развернуть ▼
|
Несмотря на то, что масляный привод и насос в бензопиле CSP-165 внешне и по посадочным параметрам схож с аналогичными деталями к бензопилам типа CSP-153, CSP-164, имеет определеное отличие - это шаг резьбы червяка привода и соответственно насоса. По этому, при замене какой-то из этих деталей, следует учитывать этот факт и менять узел в комплекте (привод + насос + цепной барабан). Открыть в новой вкладке
|
Смазка для редукторов УШМ Развернуть ▼
|
В углошлифовальных машинках (УШМ) (Рис.1) основным узлом, подвергающимся наибольшим нагрузкам при работе, является редуктор, состоящий из косозубых шестерен. Правильно подобранная смазка значительно снижает силу трения и нагрев узлов редуктора. Производители инструмента таких брендов как Makita, Bosch, DeWalt, Metabo настаивают на применении смазки строго оговоренной в инструкции. Это политика производителя и применение других смазочных материалов может служить причиной отказа в гарантийном обслуживании. Но что делать если инструмент бюджетный и в инструкции ничего не сказано о том какую смазку использовать для обслуживания инструмента? К тому же некоторые модели УШМ, из разряда недорогих, могут иметь изначально неправильно подобранную смазку.
Мы понимаем, что редуктор УШМ требует периодической замены смазки. Необходимость замены смазки можно определить косвенным путем по износу щеток. Чем интенсивнее используется инструмент, тем чаще требуется замена смазки. Еще одним из признаков необходимости замены может служить повышенный шум редуктора.
Проверить состояние смазки можно сняв крышку редуктора (Рис.2). Обычно это происходит в период поступления инструмента в ремонт. Старая смазка (Рис.3) имеет темный грязный цвет, загустевший вид, распределена ко краям корпуса редуктора или сбивается комками. Шестерни как правило сухие. Если внимательно осмотреть зубья шестерен, то можно заметить пятно контакта с отсутствием смазывающего материала (Рис.4).
Старая смазка удаляется полностью (Рис.5), редуктор и шестерни тщательно промываются (Рис.6). Для промывки можно использовать керосин, бензин либо автомобильные средства для прочистки двигателя.
Теперь о смазке. Смазка должна соответствовать основным требованиям:
- иметь динамическую вязкость не более 800 Па*с;
- температуру каплепадения не менее +120ºС;
- предел прочности не менее 120 Па.
В нашем сервисе мы используем смазку AGIP (Azienda Generale Italiana Petroli) коммерческий бренд итальянской группы Eni S.p.A. (Рис.7). Есть несколько типов смазок отличающихся по вязкости и обозначаются по классификации NLGI как:
- EP2 (мягкая)
- ЕР1 (очень мягкая)
- ЕР0 (полужидкая)
- ЕР00 (жидкая).
Из всех перечисленных типов смазок любая укладывается в требования к использованию в редукторе, но есть нюансы. Чем более оборотистый редуктор, тем более жидкая смазка необходима в использовании. Таким образом для низкооборотистых редукторов типа миксер-дрель, сабельная пила, электролобзик и пр. может использоваться смазка класса ЕР2, ЕР1. Для высоко скоростных редукторов, типа УШМ, нужна будет более жидкая смазка класса ЕР0, ЕР00.
В крайнем случае можно применить смазку для ШРУС-ов, используемой в автомобильной технике, но при этом следует понимать, что густая смазка будет оказывать сопротивление вращению узлов редуктора, вызывая при этом повышенную температуру и нагрузку на электродвигатель. Для достижения нужной консистенции смазки можно добавить масло МС-20.
Количество смазки в редуктор УШМ закладывается на 1/3 заполнения всего объема (Рис.8). Если заложить лишнее количество смазки, то при температурном расширении она начнет выдавливаться через уплотнения и подшипники, при этом редуктор будет сильно нагреваться. При недостатке смазки ее масса распределится по стенкам редуктора и не будет подхватываться для смазки узлов, что в скором времени вызовет быстрый износ деталей. Это справедливо практически для всех редукторов подобного типа.
Проконтролировать объем смазки можно пробным включением собранной УШМ-ки на непродолжительное время в холостом режиме. Если редуктор начал греться, из сальников и прокладок появляются следы вытекания смазки, то это говорит о том что смазки слишком много. Если смазки мало, то редуктор будет работать с повышенным шумом. После пробного включения, сняв крышку редуктора, мы должны увидеть хорошо смазанные шестерни (Рис.9). Лишнюю смазку следует удалить, недостающую доложить.
И на всякий случай, на Рис.10 приведена таблица выпускающихся смазок отечественным производителем. Открыть в новой вкладке
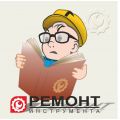 Лого 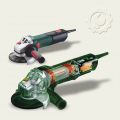 Рис. 1 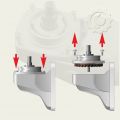 Рис. 2 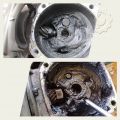 Рис. 3 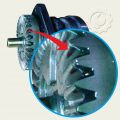 Рис. 4 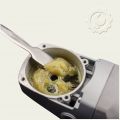 Рис. 5 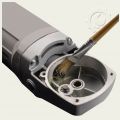 Рис. 6 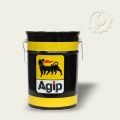 Рис. 7 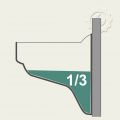 Рис. 8 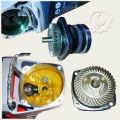 Рис. 9 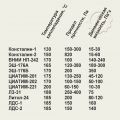 Рис. 10
|
Не удерживает давление Развернуть ▼
|
Одной из причин того, что домкрат не удерживается под нагрузкой может быть повреждение манжеты поршня (Рис.1_А). Причиной является не совсем качественное изготовление цилиндра (Рис.1_В).
При изготовлении разгрузочных каналов в цилиндре, иногда могут оставаться заусенцы от обработки металла ввиде острых краев (Рис.2_А). В итоге, после такого небрежного изготовления, происходит повреждение манжеты насосного поршня (Рис.3_А).
Простая замена поврежденного узла, в данном случае, не поможет. Необходимо устранить первопричину повреждения, а именно устранить заусенец. С этим успешно справится шлифовальный лепестково-радиальный круг мелкой зернистости (Рис.4_А). Достаточно немного, без фанатизма, обработать внутреннюю поверхность цилиндра (Рис.5). Зернистость может быть около 420-600 единиц. Открыть в новой вкладке
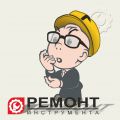 Logo 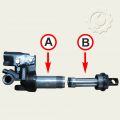 Рис. 1 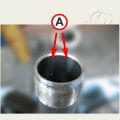 Рис. 2 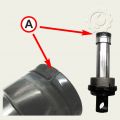 Рис. 3 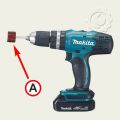 Рис. 4  Рис. 5
|
Сваливание ремня со шкива (бетоносмеситель ЕСО серии СМА) Развернуть ▼
|
В бетоносмесителях ЕСО серии СМА наблюдалось такое явление как сваливание ремня со шкивов Рис.1. Конструктивно механизм привода представляет собой электродвигатель со шкивом (Рис.2_А), который связан ручейковым ремнем (Рис.2_В) с ведомым шкивом (Рис.2_С). Вал ведомого шкива вращается во втулке (Рис.2_D). Электродвигатель закреплен к плите моторного блока через кронштейн (Рис.2_Е).
Причина сваливания ремня заключается в том, что шкивы находятся не в одной плоскости вращения. В первом случае это может быть что оси шкива и двигателя параллельны, но центра ручейкового канала смещены относительно друг друга (Рис.3_А). Ремень в этом случае смещается к краю шкива, упирается в ограничительный буртик. В этом случае ремень, наползая на буртик сваливается, либо трением об этот буртик оплавляет его.
Во втором случае оси шкива и двигателя могут быть не параллельны (Рис.3_В) и тогда ремень просто съезжает со шкива. Решать проблему следует творчески либо методом подкладывания регулировочных шайб, либо заменой неисправных деталей. В узле есть три места из-за которых появляется рассматриваемая проблема - это разбитая втулка ведомого шкива (Рис.4_А), кронштейн крепления электродвигателя (Рис.4_В) и нижний болт крепления плиты моторного блока (Рис.4_С).
В случаях непараллельности осей шкива и двигателя может быть износ втулки (Рис.4_А). В этом случае ремень будет соскальзывать в сторону двигателя (Рис.5). Тут нужна будет замена плиты моторного блока.
Если ремень уходит в сторону от двигателя (Рис.6), то вероятнее всего ось шкива электродвигателя повернута (по рисунку) по часовой стрелке, т.е. задняя часть двигателя как бы опущена. В этом случае можно подложить регулировочные шайбы между стойкой бетоносмесителя и плитой моторного блока (Рис.4_С). Это касается случаев непараллельности осей шкивов (Рис.3_В).
В случаях когда плоскости шкивов параллельны, но не совпадают между собой, как бы смещены (Рис.3_А) можно подложить шайбы между плитой моторного блока и кронштейном крепления электродвигателя (Рис.4_В). В этом случае мы можем сместить шкив электродвигателя в сторону от плиты обеспечив плоскостность с ведомым шкивом. Открыть в новой вкладке
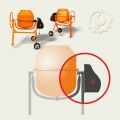 Рис. 1 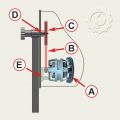 Рис. 2 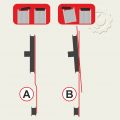 Рис. 3 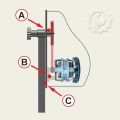 Рис. 4 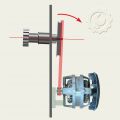 Рис. 5 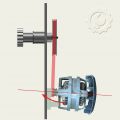 Рис. 6
|
Не качает воду, завоздушивание (ЕСО серии DP) Развернуть ▼
|
Статья о ситуации когда при визуально исправном насосе нет подачи воды. Т.е. электромотор работает, крыльчатка вращается, поплавок включает и выключает двигатель, но подачи воды нет. Основные узлы насоса на Рис.1. Это верхняя крышка с электрической частью (Рис.1_1), электромотор (Рис.1_2), открытое многолопастное рабочее колесо, далее будем называть его крыльчаткой (Рис.1_3) и нижняя часть корпуса для забора воды (Рис.1_4). При погружении насоса нижняя часть корпуса должна наполниться водой (Рис.2_1) о чем будут свидетельствовать поднимающиеся пузыри воздуха. Вращающаяся от электродвигателя крыльчатка за счет центробежной силы втягивает воду в нижней части насоса (Рис.2_2) и выбрасывает в боковой канал (Рис.2_3). Далее по шлангу вода под давлением поступает наружу. Для того чтобы полость заполнилась водой предусмотрено дренажное отверстие в нижней части корпуса (Рис.3). Отверстие реализовано в виде клапана и состоит из металлического шарика (Рис.4_1) и удерживающей его пластинки (Рис.4_2). Работает это так. При пустой полости нижней части корпуса шарик под своим весом опускается вниз и удерживается от выпадения пластинкой. В этом случае вода будет поступать в образовавшееся отверстие в полость (Рис.5_А), а воздух вытесняться (Рис.5_В). Когда насос начнет работать, то внутри полости возникнет повышенное давление от нагнетаемой воды и шарик под напором поднимается вверх (Рис.5_С) и перекрывает дренажное отверстие, препятствуя ненужной утечке воды. В случае засорения канала шарик не сможет вернуться в исходное нижнее положение и останется вверху, перекрыв дренажное отверстие (Рис.6). В этом случае при погружении насоса вода не будет заполнять насосную полость и вращающаяся крыльчатка будет просто гонять воздух по кругу. Нагнетание воды в этом случае происходить не будет. Открыть в новой вкладке
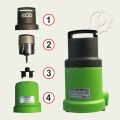 Рис. 1 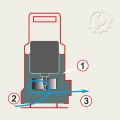 Рис. 2 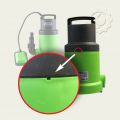 Рис. 3 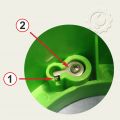 Рис. 4 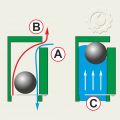 Рис. 5 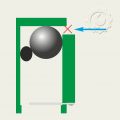 Рис. 6
|
Коленвал со шпонкой и без (AE 705-3_AE 502-3, AC 252, AC 253) Развернуть ▼
|
Все эти модели имеют схожую конструкцию и по тому представлены на сайте одним чертежом, но есть некоторые отличия в исполнении коленвалов. В старых моделях, для позиционирования коленвала на ведущем валу, использовалась шпонка (Рис.1_А). На более новых моделях вместо шпонки используется винт (Рис.1_В). Винт позиционирования определяет положение коленвала на ведущем валу (Рис.2_А), а винт (Рис.2_В) фиксирует коленвал, обжимая его в направлении синих стрелок (Рис.2). На Рис.3 вид со стороны резьб - винт позиционирования (Рис.3_А) и фиксирующий винт (Рис.3_В). Открыть в новой вкладке
|
Лайфхак, приспособление для испытаний Развернуть ▼
|
Для проверки работоспособности мотокосы иногда приходится запускать двигатель без приводной трубы. Это бывает в случаях, когда необходимо проверить устройство на биение и определить что вызывает вибрацию - приводной вал, оснастка или сам двигатель. Для этого нам необходимо отключить дополнительные узлы и методом исключения определить неисправный узел. Запустить двигатель мотокосы без приводного вала у нас не получится, т.к. отсутствие барабана в приводном валу не сможет ограничить вылет кулачков муфты сцепления. Нам надо чем-то заменить приводной вал. Для этого можно использовать отдельно тестовый корпус муфты сцепления с барабаном, насаженный на небольшой отрезок приводной трубы (Рис.1). Открыть в новой вкладке
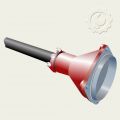 Рис.1
|
Поршень. Какой стороной устанавливать? Развернуть ▼
|
Иногда возникает вопрос, какой стороной установить поршень? Где у него передняя, а где задняя части? Попробуем разобраться.
Как правило, осевое положение пальца поршня несколько смещено в одну из сторон относительно оси самого поршня. На слабонагруженной технике встречаются поршни с пальцами, расположенными на одной оси с осью поршня. В этом случае нет разницы какой стороной устанавливать поршень. Для поршней со смещенным пальцем разница есть и о ней поговорим подробнее.
На (Рис.1_А) ось вращения коленвала, (Рис.1_В) ось вращения шатуна относительно коленвала. Во время работы двигателя (красной стрелкой показано направление вращения коленвала) шатун постоянно находится под некоторым углом к оси цилиндра, причем этот угол постоянно изменяется. Поэтому сила, приложенная к поршневому пальцу, раскладывается на две. Эти силы назовем Fшатуна (Fш) и Fпоршня (Fп) (Рис.2). В результате действия этих сил возникает третья сила, воздействующая на поршень и направленная перпендикулярно оси цилиндра. Назовем ее Fрезультирующая (Fрез.). Чем больше силы Fш и Fп, тем больше будет сила Fрез.
В ВМТ и НМТ вектора Fш и Fп складываются и Fрез. в этом случае будет равна нулю (Рис.3).
После прохождения ВМТ происходит вспышка топливной смеси и поршень перекладывается, т.к. меняется направление силы вектора шатуна (Fш) (Рис._4_А). И в этом цикле сила эта намного больше той силы, что была при сжатии. Если верить справочникам, то боковая сила, прижимающая поршень к стенке цилиндра приблизительно равна 10% — 12% процентов, от силы, действующей в направлении оси цилиндра. У автомобиля это около нескольких сотен килограмм. Из-за скоротечности процесса такое перекладывание поршня можно сравнить с ударом.
Для уменьшения силы удара, при перекладке поршня, ось поршневого пальца (вернее ось отверстия в бобышках поршня под поршневой палец) смещена в сторону основной упорной поверхности, т.е. вперед по направлению движения газов (Рис._5). Дополнительно на днище поршня ставится отметка (Рис.6_А).
По итогу нужно запомнить следующее. Метка на поршне всегда стоит со стороны где палец ближе к стенке поршня (Рис.7_А) и направлена должна быть против хода вращения коленвала (Рис.7_В).
Возникли вопросы, пришлось дополнить статью и разложить более подробно.
На Рис.8 поршни с центральным расположением пальца (слева) и со смещенным (справа).
Вертикальная сила (Рис.8_1), действующая на поршень, раскладывается на две разнонаправленные (Рис.8_2) и (Рис.8_3). Это происходит потому, что вектор шатуна (Рис.8_2) смещен относительно вертикали и направлен на точку опоры шатуна и шейки коленвала. Эти силы прижимают поршень к одной из сторон цилиндра (Рис.8_4). В данном примере вращение коленвала против часовой стрелки.
По мере вращения коленвала шатун принимает противоположные углонаправленные положения, заставляя поршень перекладываться с одной стороны на другую. При скоротечности процесса такие перекладывания сродни ударам. Все эти силы и при цикле сжатия, и при цикле вспышки. Но вертикальная сила, действующая на поршень при вспышке, гораздо больше этой же силы при цикле сжатия. По-этому и сила прижатия к стенке цилиндра при вспышке будет больше. Такое явление негативно сказывается на износостойкости и общей работе двигателя. Чтобы уменьшить такие нагрузки палец смещается относительно оси поршня. Такое смещение обычно с пределах 1-2,5 мм. Теперь о том что происходит.
Если палец расположен по центру и совпадает с осью поршня, то вертикальная сила действующая на поршень будет поровну распределена как на переднюю часть дна поршня (Рис.9_1), так и на заднюю (Рис.9_2). При смещении пальца вертикальная сила будет распределена на дно поршня не равномерно. Это можно с некоторой натяжкой сравнить с коромыслом, где точка переваливания будет на оси поршневого пальца. И чтобы при вспышке топлива уменьшить силу прижатия поршня к стенке цилиндра смещают ось пальца относительно оси поршня против хода вращения коленвала и по ходу отработанных газов.
Получается что на переднюю часть дна поршня приходится меньшая сила (Рис.9_5) чем на заднюю (Рис.9_4) и сила прижатия при этом соответственно уменьшится (Рис.9_6) против варианта с центральным расположением пальца (Рис.9_3). Это происходит потому, что бОльшая сила (Рис.9_4), частично преодолевая меньшую силу (Рис.9_5) пытается удержать поршень в вертикальном положении и значительно снимает нагрузку давления на стенку цилиндра (Рис.9_6) Открыть в новой вкладке
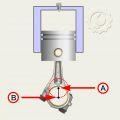 Рис.1 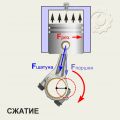 Рис.2 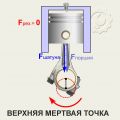 Рис.3 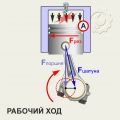 Рис.4 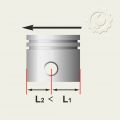 Рис.5 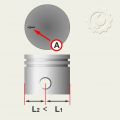 Рис.6 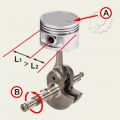 Рис.7 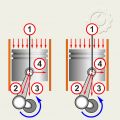 Рис.8 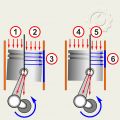 Рис.9
|
Ремонт клапана горелки (сварочный аппарат) Развернуть ▼
|
Ремонт клапана горелки (сварочный аппарат)
Нередкий случай неисправности: "Горелка не держит газ. При отпущенной клавише, газ все равно травит." Причина - неисправность клапанного механизма. Устранить неисправность легко.
Общий вид клапана на Рис.1. С одной стороны корпуса выступает шток на который нажимает рычаг рукоятки горелки. Он подпружинен и легко нажимается пальцем. С противоположной стороны мы можем заметить заглушку. Для разборки клапана нам понадобятся тиски и маленький молоточек. Ставим клапанный механизм на тиски (Рис.2) и слегка ударяем по штоку. Заглушка выпадает, а вместе с ней пружинка и шток. Желательно снизу что-то подложить, т.к. заглушка выскочив из отверстия освободит пружинку, которая может потеряться. На Рис.3 (сверху) показано положение узлов клапанного механизма. Снизу (Рис.3) детали механизма: шток (он выполняет роль золотника), пружина, заглушка и сам корпус. После демонтажа клапанного механизма оцениваем состояние уплотнительных колец (Рис.4). В случаях повреждений (закусаны при сборке, порваны и пр.) меняем на новые. Чаще наблюдается целостность колец, но при этом они "сухие". В данном случае достаточно смазать уплотнения силиконовой смазкой (Рис.5) и собрать клапан. Забив заглушку в штатное положение, можно по стыку (корпус-заглушка) слегка накернить.
Эту неисправность можно рассматривать как гарантийный случай. Открыть в новой вкладке
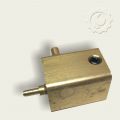 Рис.1 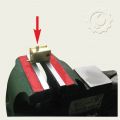 Рис.2 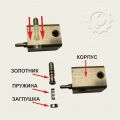 Рис.3 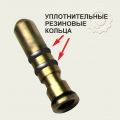 Рис.4 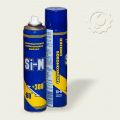 Рис.5
|
Диагностика AVR Развернуть ▼
|
Для регулировки выходного напряжения в генераторе используется регулятор напряжения (Рис. 1), который соединяется с силовой обмоткой, обмоткой возбуждения и обмоткой ротора через контактные кольца и щетки. Контролируемое напряжение силовой обмотки измеряется и сравнивается с базовым напряжением, которое устанавливается регулировочным винтом (Рис.2_красная стрелка). Если контролируемое напряжение ниже базового (низкое напряжение в розетке), регулятор автоматически увеличивает ток в роторе. Если контролируемое напряжение выше рекомендуемого (высокое напряжение в розетке), регулятор уменьшает силу тока в роторе, и выходное напряжение уменьшается. Постоянный контроль над силой тока в роторе позволяет поддерживать стабильное выходное напряжение.
Корректировка регулятора напряжения:
ВНИМАНИЕ: Корректировка должна производиться при включении электростанции и со снятой крышкой генератора. Избегайте контакта с горячей выхлопной трубой и электрическими проводами. Перед тем как корректировать регулятор напряжения, убедитесь, что частота вращения двигателя в норме.
1. Запустите двигатель и дайте ему прогреться в течение нескольких минут.
2. Используйте точный вольтметр для измерения напряжения в розетке.
3. Отрегулируйте напряжение регулировочным винтом, как показано на рисунке 1, используя отвертку.
Диагностика и поиск неисправностей AVR:
Запустить двигатель и проверить частоту вращения, при необходимости отрегулировать.
Предварительная проверка - замерить выходное напряжение непосредственно в розетке, используя вольтметр.
ВНИМАНИЕ: Нулевое напряжение свидетельствует о разрыве цепи или о полной потере остаточного магнетизма ротора. (Восстановление остаточного магнетизма в статье https://remont.tools.by/diagnostics/view/1682690091).
При неправильных показателях проводим дальнейшую диагностику, используя метод исключения.
1. Подаем постоянный ток в обмотку ротора. Для этого необходимо подсоединить аккумулятор
12В непосредственно к плюсовому и минусовому проводам щеток на коллекторе ротора. Для этого надо снять заднюю крышку (Рис.3_В) и подключиться к щеткам ротора (Рис.4_С)
2. Измеряем выходное напряжение обмотки возбуждения (должно быть 200-250В)
3. Измеряем напряжение основной обмотки (примерно 110-130В)
Если при тестировании, мы получили значения напряжения указанные выше, то неисправность связана с неработающим AVR.
К такому выводу мы пришли, исключив заведомо исправные узлы. Данные тесты подтвердили, что обмотка возбуждения и силовая обмотка исправны. Наличие выходного напряжения в розетке подтверждает исправность щеток, контактных колец и ротора. Следовательно, неисправен регулятор напряжения.
Регулятор меняется целиком и ремонту не подлежит. Открыть в новой вкладке
|
Редуктор. Повреждение зубчатой передачи Развернуть ▼
|
При повреждениях передаточных узлов в редукторе в первую очередь следует обратить внимание на прицепное устройство (Рис.1). А именно на отверстия под палец для крепления навесного оборудования (Рис.2). Отверстие должно быть ровным без эллипса и наклепов (Рис.3).
Если имеются повреждения, такие или похожие как на Рис.3, то это может свидетельствовать только о том, что клиент использовал культиватор как средство для перемещения прицепа. Пример на Рис.4. Такое использование культиватора недопустимо. Об этом прямо сказано в прилагаемой к изделию инструкции на первой странице.
Выдержка из инструкции: "Культиватор – это компактное, многофункциональное устройство для обработки и культивации земли в садах и на приусадебных участках и других целей, при наличии дополнительного оборудования. В устройстве отсутствует вал отбора мощности (ВОМ), т.е.
культиватором не предусмотрена буксировка прицепов, грузов и работа с орудиями с приводом от ВОМ. Производитель не несет ответственности за использование культиватора не по назначению".
Проблема с прицепами заключается в следующем. Прицеп имеет значительную собственную массу и при транспортировке появляются переменные ударные нагрузки на редуктор. Это движение под горку и на горку, по ухабам, ямам и пр. неровностям дороги. Эллипс и наклеп на прицепном устройстве могут только свидетельствовать о том, в каких условиях эксплуатировался культиватор.
Эти случаи не являются гарантийными и относятся к эксплуатации изделия с нарушением условий инструкции. Открыть в новой вкладке
|
Управляющий клапан DGM Water 140/160 Развернуть ▼
|
Для очистителей высокого давления DGM WATER 140/160 поставлялись управляющие клапана под резьбовое соединение (Рис.1). После 2022 года стали выпускаться модели с креплением клапанов под скобу (Рис.2). Сейчас мы имеем управляющие клапана двух видов. При ремонтах и заказе з/ч это следует учитывать, т.к. они не взаимозаменяемые. Открыть в новой вкладке
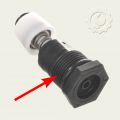 Рис.1 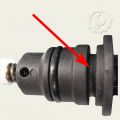 Рис.2
|
Заклинивание муфты Развернуть ▼
|
Иногда появляются случаи заклинивания муфты сцепления в мотокосах. Пользователь нажимает на газ, а редуктор не вращается. Сразу на ум приходит наиболее вероятная причина подобной неисправности - это либо слизывание шлицев на ведущем валу, либо разрушение зубчатой пары редуктора. Но все может оказаться проще. Не работает муфта сцепления. Т.е. инерционные кулачки находятся в заблокированном состоянии и не расходятся при увеличении оборотов двигателя.
Причина в зажатых болтах, на которых крепится муфта (Рис.1). Механизм крепления муфты устроен следующим образом. Под муфтой устанавливаются опорныя шайбы (Рис.2_А). Внутренний диаметр их отверстий 8,5мм. Крепежные болты имеют резьбу М8 и свободно входят в это отверстие, но затем упираются безрезьбовой частью, которая имеет диаметр 9,7мм, на шайбу. Таким образом дальше вкрутиться болт не может. Длина безрезьбовой части болта 10мм, а длина втулки муфты, в которую вставлен болт, 9,2мм (Рис.3).
Если вставить болт в муфту без пружинной шайбы, то получится что болт выступает за кромку муфты (Рис.4_А). Таким образом при зажатии болта в корпус маховика появляется осевая подвижность муфты сцепления примерно около одного миллиметра. Этот зазор компенсируется пружинной шайбой (Рис.2_В) и не мешает подвижности кулачков в радиальном направлении.
Основная причина неисправности такого типа - это изнашивание опорной шайбы, изнашивание опорной части болта, либо просто отсутствие по какой-либо причине этой опорной шайбы. Открыть в новой вкладке
|
Аккумулятор, перенос наклейки Развернуть ▼
|
При замене аккумуляторов иногда приходится сталкиваться с такой ситуацией, когда вместо оригинального аккумулятора вынуждены менять на аналог. Такое решение не противоречит требованиям производителя, но иногда вызывает негативную реакцию у клиента. Человек, не вникая в технические подробности, требует установки "оригинального" аккумулятора, тот что был при комплектации. Убеждать его в правомерности такой замены порой бывает бесполезно, т.к. мыслит он скорее ассоциативно нежели рационально.
Аккумуляиоры BULL (Рис.1) и аккумуляторы от WORTEX (Рис.2) в принципе идентичны (Рис.3) и замена одного на другой вполне оправдано. В таких случаях необходимо перенести наклейку со старого аккумулятора на новый. Сделать это легко с помощью технического фена (Рис.4). Слегка подогрев наклейку аккуратно ножиком поддеваем старую наклейку и снимаем ее со старого аккумулятора. Клейкий слой при этом должен остаться на наклейке. Если этого не произошло и что-то пошло не так, можно применить двусторонний, тонкий скотч.
Снятую наклейку аккуратно криклеиваем на новый аккумулятор (Рис.5). Полученный результат внешне не будет отличаться от "оригинального".
Такая операция обязательна при замене аккумуляторов даже в пределах одного бренда если дело касается сохранения серийного номера изделия. Серийный номер на аккумуляторе должен совпадать с серийными номерами на инструменте и на зарядном устройстве. Открыть в новой вкладке
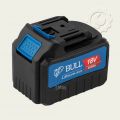 Рис.1 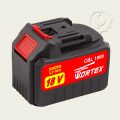 Рис.2 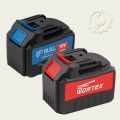 Рис.3 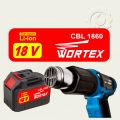 Рис.4 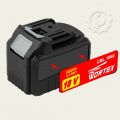 Рис.5 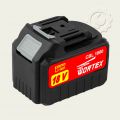 Рис.6
|
Повреждение щеткодержанелей, щеток MAKITA BO 5031 Развернуть ▼
|
Иногда поступают в ремонт эксцентриковые шлифмашины с замятыми щеткодержателями. В данной статье разговор пока про модель MAKITA BO5031. В результате деформированных щеткодержателей, щетки теряют свою подвижность и в процессе эксплуатации разрушаются. Попытаемся разобраться в чем причина такого повреждения.
Если снять верхнюю крышку инструмента, то увидим щетки в резиновых аммортизаторах (Рис.1). На Рис.2_А щеткодержатель, который вставлен в резиновый аммортизатор (Рис.2_В). Резиновый аммортизатор вместе с щеткодержателем вставлен в направляющие корпуса самой машинки (Рис.3_А - вид сверху), (Рис.3_В - вид в плане). При монтаже щеткодержателя (Рис.4_А) может так получиться, что резиновый аммортизатор не сядет на место. Пойдет с перекосом или еще как и упрется в направляющие (Рис.4_В). Иными словами не дойдет до конца.
Если механик не проявит должного внимания к данной ситуации, то в дальнейшем произойдет следующее. Сверху будет установлена крышка, у которой есть выступы, предназначенные для фиксации щеткодержателя (Рис.5). Фиксируя крышку винтами, механик принудительно пытается затолкнуть щеткодержатели на свое место. Но этого не происходит. Резину аммортизатора раздавливает и она еще плотнее цепяется за направляющие. Такую ситуацию несложно заметить. Крышка в этом случае не сядет на место. Она должна мягко, от руки сесть на место, без зазоров и пр. перекосов до закручивания винтов.
Если не обратить на это внимание, то дальнейшее закручивание крепежных винтов крышки приведет к деформации самого щеткодержателя (Рис.6) и прижмет щетку, лишив ее подвижности. Результат такой невнимательности на Рис.7, где (А) промятый корпус щеткодержателя и (В) разрушенные щетки. Открыть в новой вкладке
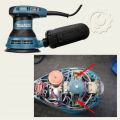 Рис.1 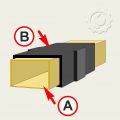 Рис.2 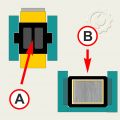 Рис.3 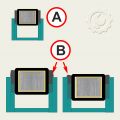 Рис.4 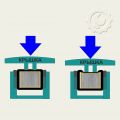 Рис.5 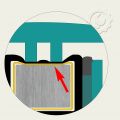 Рис.6 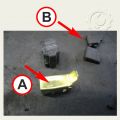 Рис.7
|
Не работает маятниковый ход в лобзике ST 1301 BULL Развернуть ▼
|
В ремонт поступило несколько лобзиков BULL ST 1301 c заявленной неисправностью «не работает маятниковый ход».
Проблема подтвердилась, был выявилен неправильный алгоритм движения механизма подкачки опорного ролика. Производителю об этом сообщили. Пока идёт согласование по возможному устранению неисправности. При поступлении в ремонт лобзика с данной неисправностью, будет выписан акт на замену.
Также при диагностике в некоторых лобзиках не удалось установить в пилкодержатель пилку Bosch T 101D с толщиной хвостовика 1,49мм. При выявлении такой неисправности необходимо менять шток.
Все перечисленные случаи относятся к гарантийным. Открыть в новой вкладке
|
Редуктор. Треск в редукторе, отсутствует вращение (шуруповерт) Развернуть ▼
|
На шуруповёрте имеется шкала, с помощью которой можно регулировать непосредственную силу вращения. Поворачивая регулятор, вы выбираете нужный вам режим. Этим же регулятором можно выбрать режим сверления.
Есть несколько правил, которые позволяют значительно продлить срок службы устройства.
1.Избегать сверления шуруповертом твёрдые, бетонные и каменные поверхности, прилагая чрезмерное усилие (для этого есть другие устройства)
2.Не переключать регулятор во время работы шуруповерта
3.После переключения скорости необходимо убедиться что шестерни-сателлиты зашли плотно в зацепление, включив шуруповерт без нагрузки.
Частым повреждением является износ блокировочных зубьев на подвижной шестерне переключения скоростей. На рис.1 пример такого повреждения. При не полностью включенном переключателе (спешка, неаккуратность, невнимательность) происходит проскальзывание зубьев. При неоднократном проскальзывании получается износ зубьев шестерни (Рис.2) - редуктор разрезан для наглядности. В дальнейшем, даже при незначительной нагрузке, редуктор начинает трещать и устройство становится не пригодным для эксплуатации.
Такие повреждения носят эксплуатационный характер и являются результатом либо неаккуратного, либо интенсивного использования инструмента и гарантийным случаем не являются.
В пластиковом исполнении блокировочных зубьев, повреждение происходит на ответной части (Рис.3). Открыть в новой вкладке
|
Карбюратор настройка (2-х тактные двигатели) Развернуть ▼
|
Существует несколько вариантов исполнения безпоплавковых карбюраторов. Некоторые модели карбюраторов, в целях удешевления товара, исполнены в нерегулируемом варианте. Такие карбюраторы, в случаях каких-нибудь неисправностей, просто меняются на новый. В нашей статье мы рассмотрим карбюратор, который поддается полной регулировке как по качеству смеси, по ее количеству, так и по режиму холостого хода (ХХ).
Такие карбюраторы имеют три регулировочных винта. Винт качества смеси (Рис.1_А), обозначается буквой "L". Он расположен всегда ближе к цилиндру. Винт количества смеси (Рис.1_В) или винт максимальных оборотов, обозначается буквой "H". И винт регулировки холостого хода (Рис.1_С). На Рис.1_D - условно обозначен главный жиклер.
В первую очередь необходимо настроить качество смеси. Идеальным соотношением воздуха к топливу (по весу) 14,7/1 (14,7кг воздуха к 1кг топлива). Такое соотношение называют стехиометрической. При таком соотношении коэффициент избытка воздуха равен единице (обозначается буквой лямбда), т.е. лямбда равна единице.
Если вращать винт в сторону откручивания, то этим самым мы, добавляя топливо, обогащаем смесь и лямбда становится меньше единицы (лямбда - соотношение воздуха к топливу, а не наоборот). На Рис.2_GIF понятна закономерность обогащения смеси и реакция двигателя.
Вращение винта в обратную сторону приводит к противоположному результату (Рис.3_GIF). Смесь обедняется и коэффициент избытка воздуха (лямбда) становится больше (много воздуха - мало топлива).
В обоих случаях обороты двигателя падают. Наша задача добиться максимальных оборотов двигателя, найдя такое положение винта качества смеси, при котором это требование будет выполняться (Рис.4_GIF).
После того как мы выставили максимальные обороты двигателя, винтом холостого хода (подпирает дроссельную заслонку, может обозначаться LD) (Рис.1_С) добиваемся такого положения при котором обороты двигателя будут на 300 об/мин больше нормальных оборотов холостого хода. В нашем случае ХХ 2800 об/мин. Мы докручиваем до 3100 об/мин (Рис.5_GIF).
Возвращаемся к винту качества смеси "L" (Рис.1_А) и вращаем в сторону ОТКРУЧИВАНИЯ (встречаются карбюраторы с левой резьбой). При этом обороты начнут падать. Доводим обороты двигателя до нужных нам 2800 об/мин (Рис.6_GIF).
Завершаем настройку карбюратора винтом количества смеси "Н" (Рис.1_В). Выжимаем полный газ и по тахометру выставляем необходимое количество максимальных оборотов.
Если ориентироваться "на слух", то придется ориентироваться по реакции двигателя. Если при резком нажатии на газ происходит провал (двигатель как бы "душится"), то это означает обеднение топлива в переходный момент (винтом "Н" добавить, открутить). Если максимальные обороты недостаточны, двигатель не набирает нужные обороты - смесь богатая. Винт "Н" закрутить для уменьшения подачи топлива. Открыть в новой вкладке
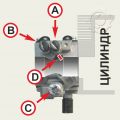 Рис.1 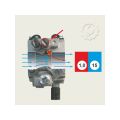 Рис.1_GIF 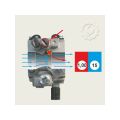 Рис.2_GIF 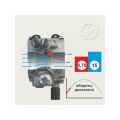 Рис.3_GIF 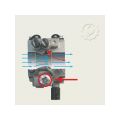 Рис.4_GIF 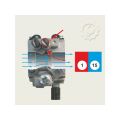 Рис.5_GIF
|
Выдвижение штока (погружной вибрационный насос) Развернуть ▼
|
В погружных насосах иногда происходит такое явление как выдвижение штока. Насос в результате перестает работать. Основные узлы насоса на Рис.1. Более детально можно рассмотреть на Рис.2
Насос относится к устройствам вибрационного типа. Принцип работы основан на периодическом примагничивании якоря к катушке с частотой, обусловленной нашей сетью, т.е. 50 Гц (Рис.5).
На Рис.3_А цикл всасывания, Рис.3_В режим прокачивания воды из насоса.
Якорь напрессован на шток (Рис.2) и удерживается двумя контргайками(Рис.5_А) через шайбы (Рис.4_B). Конструкция насосного механизма на Рис.6.
При ударах якоря о катушку статора, вся нагрузка приходится на резьбовое соединение двух гаек и штока. При ослаблении гаек (Рис.7_А), от вибрации, шток по инерции может выдвинуться вниз (Рис.7_В) и работа насоса при этом прекратится. Ремонт в таком случае сводится к тому, что достаточно вернуть шток на место и затянуть гайки. Гайки обязательно посадить на фиксирующий резьбовой состав.
В случаях когда сорвана резьба - меняется шток и гайки на новые. Открыть в новой вкладке
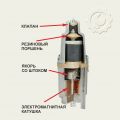 Рис.1 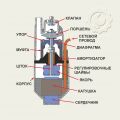 Рис.2 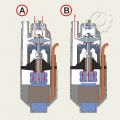 Рис.3 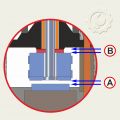 Рис.4 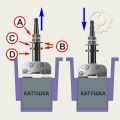 Рис.5 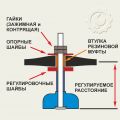 Рис.6 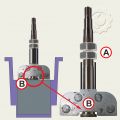 Рис.7
|
Обслуживание теплогенератора Развернуть ▼
|
Принцип работы дизельных теплогенераторов (Рис.1) везде имеет схожую схему. Топливо из бака (Рис.2_1) поступает через топливный фильтр (Рис.2_2) в насос (Рис.2_3) и под давлением подается дальше по магистрали (Рис.2_4). В магистраль высокого давления включены электромагнитный клапан (Рис.2_5) и распыляющая форсунка (Рис.2_6). Искра для поджига топлива создается модулем высокого напряжения (Рис.2_7) и подается на электроды (Рис.2_8). Излишки топлива сбрасываются насосом обратно в бак (Рис.2_9).
Топливные насосы бывают роторного и шестеренного типа и между собой также имеют схожие схемы. Нагнетающей системой в насосах шестеренного типа являются эксцентриковая шестерня и ответная рабочая камера (Рис.3_1). Снаружи насос имеет входной канал (Рис.4_1), выходной канал (Рис.4_2), канал сброса избытка топлива, "обратка" (Рис.4_3). Так же имеется выход на манометр для проверки давления (Рис.4_4), закрыт заглушкой. Давление регулируется винтом (Рис.4_5). Сверху корпуса фильтр тонкой очистки (Рис.5_1) под заглушкой (Рис.5_2).
Первичный топливный фильтр состоит из колбы отстойника (Рис.6_1), фильтрующего элемента (Рис.6_2) и самого корпуса (Рис.6_3). Топливо засасывается в колбу (Рис.6_4), далее через фильтр поступает на вход насоса (Рис.6_5).
Самым последним барьером для нежелательных примесей в топливе является узел форсунки (Рис.7_1). В форсунку ввернут фильтрующий элемент (Рис.7_2) который выполнен из мелких спрессованных шариков.
Теперь о правилах обслуживания теплогенератора и поддержке его в рабочем состоянии:
- чистить первичный топливный фильтр руководствуясь визуальным осмотром на отсутствие мусора в колбе (Рис.6_1), при необходимости заменить фильтрующий элемент (Рис.6_2)
- после каждых 300 часов эксплуатации очистить топливный фильтр насоса (Рис.5_1), осмотреть форсунку, ее фильтрующий элемент (Рис.7_2) и при необходимости (Рис.7_3) заменить.
Можно попытаться очистить фильтр форсунки используя средство для очистки карбюраторов или ацетон. Для этого следует поместить фильтр в промывочное средство на несколько часов и затем продуть сжатым воздухом. Но из практики следует отметить, что подобными процедурами редко удается достичь хорошего результата. Как правило меняется форсунка целиком.
- через каждые 500 часов промыть топливный бак чистым дизельным топливом (нельзя использовать для промывки воду). Сливное отверстие находится внизу бака под заглушкой (Рис.8)
- дважды в сезон очистить вентилятор и камеру сгорания сжатым воздухом, сняв верхнюю крышку
- раз в сезон проверить зазор между электродами, целостность трансформатора и высоковольтных проводов, надежность крепежных соединений, целостность электрических контактов и клемм.
Соблюдение этих простых правил позволит значительно увеличить срок службы теплогенератора.
И последнее что хотелось бы отметить. Винт регулировки давления насоса (Рис.4_5) настраивается в сервисном центре на определенное давление, которое оговорено инструкцией для данной модели теплогенератора. Нельзя его использовать как винт для увеличения или уменьшения получаемого тепла. Это часто приводит к нарушению нормальной работы устройства и возможному выходу его из строя. Для исключения соблазна покрутить винт, рекомендуется в сервисном центре установить какую-нибудь пломбу-заглушку (Рис.9), можно просто капнуть герметиком. Открыть в новой вкладке
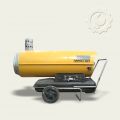 Рис.1 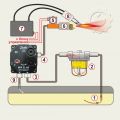 Рис.2 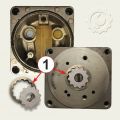 Рис.3 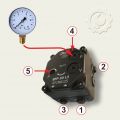 Рис.4 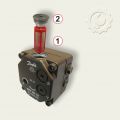 Рис.5 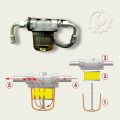 Рис.6 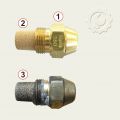 Рис.7 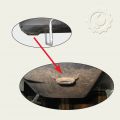 Рис.8 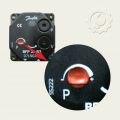 Рис.9
|
LG-634_задир ЦПГ Развернуть ▼
|
В модели газонокосилок ECO LG-634 обнаружен неприятный момент с конструктивным решением воздушного фильтра (Рис.1). Внешний вид фильтрующего узла на Рис.2.
Под крышкой, внутри корпуса фильтра, находится 3 паролоновые пластинки (Рис.3). Две из них стоят на пути всасывания воздуха (Рис.4_А), одна непосредственно перед карбюратором (Рис.4_В). Кусочки паролона просто лежат в предусмотренных нишах корпуса фильтра и разделены перегородками. Воздух, поступая снизу, проходит через 2 крайних паролоновых фильтра (Рис.5_А). Далее, огибая перемычки, поступает через центральный паролоновый фильтр в карбюратор и далее в камеру сгорания двигателя (Рис5_В).
В этой схеме есть существенный изъян. Разрежение, создаваемое двигателем, заставляет паролоновую вставку прогибаться. В процессе эксплуатации фильтр деформируется и перестает плотно прилегать к краям перегородок. При частичном засорении фильтра такое происходит намного быстрее, т.к. сопротивление потоку увеличивается и воздух ищет более легкие пути. Этим путем становится образовавшаяся щель (Рис.6). Так же бывали случаи несоответствия размеров фильтров с самим корпусом. Они были короче нужных размеров, где так же образовывалась щель между корпусом и фильтром.
В этом случае воздух уже проходит не через фильтр, а мимо него (Рис.7_А) и беспрепятственно, вместе с абразивной пылью, поступает в цилиндр двигателя (Рис.7_В).
Результат можно увидеть на Рис.8. Грязь в полости карбюратора (Рис.8_А) и абразивный износ цилиндра двигателя (Рис.8_В).
В большинстве случаев это признается как гарантия, т.к. клиент не в состоянии контролировать воздушный фильтр на предмет его деформации. Открыть в новой вкладке
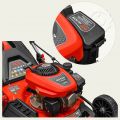 Рис.1 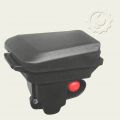 Рис.2 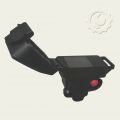 Рис.3 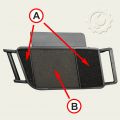 Рис.4 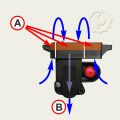 Рис.5 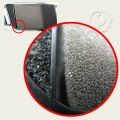 Рис.6 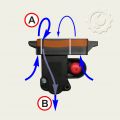 Рис.7 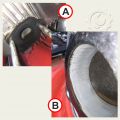 Рис.8
|
Клапана, большой зазор и в чем опасность Развернуть ▼
|
Общая работа клапанного механизма на Рис.1_GIF. Нас интересует место взаимодействия клапана с рычагом механизма газораспределения (Рис.2).
Для наглядности на Рис.3 удалена возвратная пружина клапанной тарелки. На схеме рычаг (Рис.3_1), хвостовик клапана (Рис.3_2) и клапанная тарелка (Рис.3_3). Клапанная тарелка, через возвратную пружину, обеспечивает прижатие клапана к седлу в цилиндре, закрывая каналы впуска-выпуска. При работе хвостовик клапана опирается на рычаг, который и управляет клапаном. Между клапаном и рычагом должен быть температурный зазор, который составляет в большинстве случаев 0,15 - 0,2 мм.
При эксплуатации происходит износ узлов хвостовика клапана (Рис.4_1), клапанной тарелки (Рис.5_1) и контактного места на рычаге. Клапанная тарелка вырабатывается в месте контакта с клапаном (Рис.6). При больших износах этих узлов (Рис.7_1) появляется такой момент при котором хвостовик клапана уже не достает до рычага и рычаг начинает опираться о тарелку (Рис.7_2). Результат такого касания на Рис.8 где виден износ контактной площадки рычага. Синим овалом обозначена контактная площадка такой, какой она должна быть изначально (Рис.8_красная стрелка).
Что происходит в этом случае и чем это опасно? Рычаг опираясь на тарелку отжимает возвратную пружину и освобождает клапан. Клапан выпадает из зацепления тарелки и отправляется в "свободное путешествие" (Рис.9_GIF). Часто это заканчивается встречей с поршнем, повреждая его вплоть до пробивания насквозь.
Из выше сказанного вывод - игнорирование такого состояния клапанов может обернуться большими проблемами с двигателем. Открыть в новой вкладке
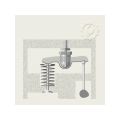 Рис.1_GIF 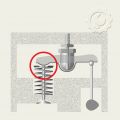 Рис.2 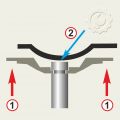 Рис.3 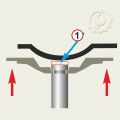 Рис.4 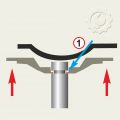 Рис.5 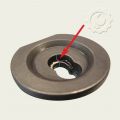 Рис.6  Рис.7 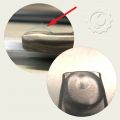 Рис.8 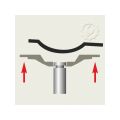 Рис.9_GIF
|
Принцип работы перфоратора, про отверстия в цилиндре (часть 2) Развернуть ▼
|
В некоторых поршнях цилиндрического типа имеются отверстия (Рис.1). Это характерно для перфораторов с качающимся подшипником, где электродвигатель расположен по одной оси со стволом. Аналогичные отверстия есть и в перфораторах с шатунно-кривошипным механизмом. Там они расположены в самом стволе. Для чего нужны эти отверстия?
Отверстие (Рис.2_В) предназначено для дросселирования полости воздуха между поршнем и тараном (Рис.2_А). При отсутствии такого отверстия таран не смог бы перемещаться по цилиндру и не выполнял бы своих функций по обеспечению удара (Рис.3_GIF).
Второе отверстие (Рис.4_В) необходимо для того, что бы при отсутствии насадки (бура) не было бесконтрольного перемещения тарана по цилиндру. Без нагрузки такое перемещение может вызвать сильные ударные моменты на переднюю часть ствола. При нормальной работе вся ударная нагрузка от тарана приходится на ударник или боек, который в свою очередь опирается на бур. При отсутствии насадки ударник будет утоплен в переднюю часть ствола и вся ударная нагрузка будет приходиться на узлы ствола, которые не предназначены для этого.
Отверстие (Рис.4_В) соединяет воздушную полость цилиндра (Рис.4_А) с атмосферой. При отсутствии насадки боек будет перемещен в переднюю часть ствола, а таран "запаркуется" в конечном цикле своего перемещения. При работающем перфораторе воздух будет свободно засасываться и также выходить из цилиндра не перемещая таран (Рис.5_GIF). Для удержания тарана на месте предусмотрена проточка в передней его части, которая прихватывается резиновым кольцом.
Для приведения ударного механизма в рабочее положение достаточно установить бур и надавить на него. Этим самым мы вытолкнем таран из "парковки" и он, перекрыв дроссельное отверстие, подхватится поршнем (Рис.6_GIF). И дальше уже будет происходить работа в штатном режиме (Рис.7_GIF). Таран не проваливается так как постоянно ударяется о боек.
Как только мы снимем оснастку таран дойдет до крайнего переднего положения и прихватится резиновым кольцом. Дроссельное отверстие не позволит тарану сняться с "парковки" (Рис.8_GIF). Открыть в новой вкладке
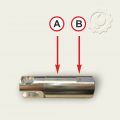 Рис.1 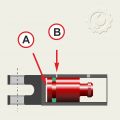 Рис.2 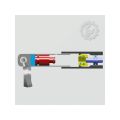 Рис.3_GIF 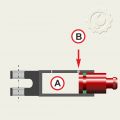 Рис.4 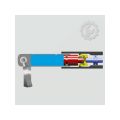 Рис.5_GIF 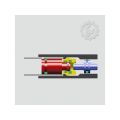 Рис.6_GIF 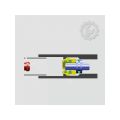 Рис.7_GIF 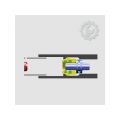 Рис.8_GIF
|
Принцип работы перфоратора (часть 1) Развернуть ▼
|
Большинство перфораторов имеют основные сходные по назначению узлы. Рассмотрим работу узлов в перфораторе с кривошипно-шатунным механизмом. Ударный механизм состоит из бойка или ударника (Рис.1,1), тарана (Рис.1,2) и поршня (Рис.1,3). Во всех этих узлах имеются уплотнительные кольца. Благодаря им создаются две независимые воздушные полости. Одна между ударником и тараном. Вторая между тараном и поршнем.
В статичном положении давление в обоих полостях одинаковое (Рис.1,А). При вращении приводной шестерни поршень начинает смещаться назад, создавая между собой и тараном полость с пониженным давлением (Рис.1,В). Уплотнение и масса тарана несколько придерживает его от перемещения. И когда давление понизится достаточно для преодоления сопротивления уплотнителя, таран рывком перемещается в сторону поршня (Рис.1,С), который к тому времени уже начинает двигаться навстречу. Давление в полости таран-поршень повышается, замедляя ход тарана. На встречном движении получается максимальное давление в этой полости и таран начинает двигаться в одном направлении с поршнем (Рис.2,А). Какое-то время они двигаются синхронно, но затем таран начинает двигаться быстрее поршня. На него действует поступательная сила поршня и давление между ними. В конце своего движения таран бьет по ударнику (Рис.2,В). Сила удара передается дальше через ударник к буру (Рис.2,С). Возвращаясь назад поршень потянет за собой таран. Цикл повториться (Рис.1,В). Следует добавить что таран, перемещаясь к поршню, за собой так же оставляет зону пониженного давления между собой и ударником (Рис.1,С), позволяя ударнику вернуться в исходное состояние. Проще понять принцип работы можно в динамике движения этих узлов, где изменение цвета в полостях показывает уплотнение воздуха (Рис.3_GIF).
В перфораторах, в которых применяется качающийся подшипник в качестве узла ударного механизма, принцип тот же самый. Здесь качающийся подшипник (Рис.4_1) выполняет ту же задачу что и кривошипно-шатунный узел. При вращении ведущего вала качающийся подшипник своим рычагом, связанным с внешней обоймой, приводит в поступательное движение поршень (Рис.4_2). В таких типах перфораторов поршень выполнен в форме глухого цилиндра, в котором перемещается таран (Рис.4_3). Таран толкает боек (Рис.4_4), а тот в свою очередь бур (Рис.4_5).
Механизм действия тут такой. Поршень совершает возвратно-поступательные движения, внутри которого находится таран. Если бы не было уплотнения, то имея некоторую массу таран находился бы в статичном состоянии (Рис.5_GIF). С уплотнением таран отделяет воздушную полость в глухой части поршня-цилиндра. И теперь таран уже не может находится в статичном состоянии, он вынужден перемещаться вместе с поршнем, а воздух играет роль пружины, как было описано в начальной части статьи (Рис.6_GIF). Общий механизм работы перфоратора на (Рис.7_GIF).
Из всего сказанного можно сделать определенный вывод. Для хорошего удара необходимы новые уплотнения и идеальная внутренняя поверхность цилиндров по которым двигаются узлы с этими уплотнениями. Особое внимание следует уделить смазке узла поршень-таран. Смазка должна быть достаточно жидкая, что бы не блокировать таран и достаточно вязкой, что бы сохраняться на стенках узлов. Густая смазка может блокировать дроссельные отверстия и таран "зависнет" в цилиндре поршня (Рис.8_GIF). Открыть в новой вкладке
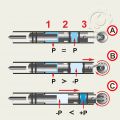 Рис.1 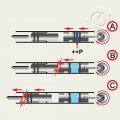 Рис.2 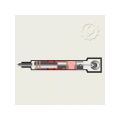 Рис.3_GIF 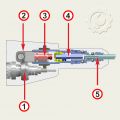 Рис.4 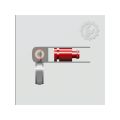 Рис.5_GIF 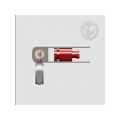 Рис.6_GIF 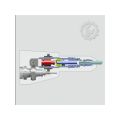 Рис.7_GIF 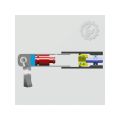 Рис.8_GIF
|
Стартер, вырывает из рук (двигатели 4-х тактные) Развернуть ▼
|
Во многих 4-х тактных двигателях, для облегчения запуска, применяется центробежный декомпрессор.
Работает это следующим образом. В статичном состоянии клапан, через толкатель, подпирается механизмом декомпрессора. Клапан двигателя при этом находится в приоткрытом состоянии, снижая компрессию двигателя. Как только мы начинаем вращать стартерной рукояткой двигатель, центробежный механизм отходит в сторону, смещая при этом упор под клапаном. Клапан возвращается в нормальное положение и двигатель работает в штатном режиме. На Рис.1_GIF видно как центробежный механизм, смещаясь по синей стрелке, перемещает поводок подпора клапана (Рис.1_GIF, красный цвет).
Это же самое мы можем посмотреть в другом ракурсе (Рис.2_GIF). Подпор клапана, под действием центробежного механизма (Рис.2_GIF,1), смещается (Рис.2_GIF,2) освобождая клапан. Клапан возвращается в штатное положение (Рис.2_GIF,3).
При повреждении подпора клапана (Рис.3 )пропадает декомпрессия двигателя. В результате при попытке завести такой двигатель стартерную рукоятку просто вырывает из рук. Рис.4_1 - зона прилегания клапанного толкателя, Рис.4_2 - повреждение.
В таких ситуациях меняется распредвал на новый. Открыть в новой вкладке
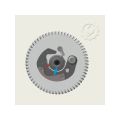 Рис.1_GIF 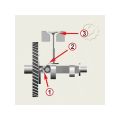 Рис.2_GIF 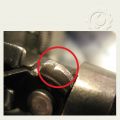 Рис.3 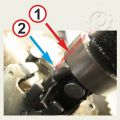 Рис.4
|
Гайковерт пневматический (принцип работы) Развернуть ▼
|
Для надежной работы пневмоинструмента необходимо соблюдать некоторые правила. После компрессора (Рис.1-1) должен стоять влагоотделитель (Рис.1-2) или более простой (Рис.1-2а). Далее между влагоотделителем и гайковертом должен стоять лубрикатор (Рис.1-3).
Пневматический гайковерт (Рис.2) и его внутреннее устройство (Рис.3). Воздух под давлением раскручивает ротор через лопатки, который передает вращение на дальнейшие узлы. Ударный механизм гайковерта (Рис.4) состоит из 6-ти основных узлов, рамка, 2 молотка, 2 штифта и упорный вал. Молотки имеют особую конструкцию (Рис.5). Относительно одного штифта (Рис.5-А) молоток смещаться в сторону не может, а относительно второго (Рис.5-В) может перемещаться в некоторых пределах (указано стрелками).
Принцип действия следующий (Рис.6). Вращение от ротора передается на рамку. В рамку вставлены штифты которые, в свою очередь, вращают молотки. Молотки имеют выступы и на валу также имеются соответствующие выступы. Войдя в зацепление друг с другом (Рис.6-А) вращение передается дальше на вал (Рис.6-В). Если гайка/болт не поддаются вращению (Рис.7), то вал останавливается, а молоток соскакивает с выступа вала (Рис.7-А) и продолжает дальнейшее вращение (Рис.7-В) Следующий выступ, ударяясь о выступ вала, возвращает молоток в исходное положение. При дальнейшем вращении выступ молотка встречается с выступом вала и происходит удар (Рис.7-С). Если болт/гайка не поддались откручиванию цикл повторяется с позиции (Рис.7-А). Реверсивное вращение обеспечивается перенаправлением воздуха переключающим золотником.
Наглядно работу ударного механизма можно понять по Рис.8_GIF. Открыть в новой вкладке
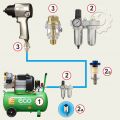 Рис.1 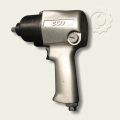 Рис.2 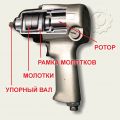 Рис.3 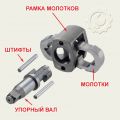 Рис.4 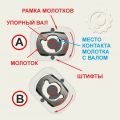 Рис.5 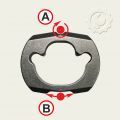 Рис.6 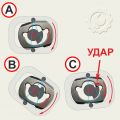 Рис.7 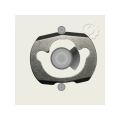 Рис.8_GIF
|
Цепи, заточка (цепные пилы) Развернуть ▼
|
Эта статья для тех у кого-то возникнет необходимость правильно либо заточить цепь, либо объяснить клиенту как грамотно это сделать. Если подобная задача стоит в условиях сервисного центра и заточки цепей носят не единичный характер, то лучший вариант это приобретение заточного станка (Рис.1).
Заточка цепи не совсем простая задача. Здесь надо учитывать одновременно несколько углов положения заточного инструмента, а заточка разно направленных зубьев должна быть произведена под одинаковыми углами. В противном случае цепь постоянно будет уходить в сторону, а шина изнашиваться неравномерно.
Для заточки лезвия режущего зуба понадобится специальный круглый напильник (Рис.2). Эти напильники разделяются по размерам. Диаметр напильника напрямую зависит от шага цепи.
• Шаг 1/4″ – диаметр 4,0 мм;
• Шаг 0,325″ — 4,8 мм;
• Шаг 3/8″ — 5,2 мм;
• Шаг 0,404″ — 5,5 мм.
Выше было сказано о не совсем простой задаче при заточке и вот в чем она заключается. Цепь, во время заточки при помощи напильника, должна быть натянута. Затачиваемый зуб, должен располагаться примерно посредине шины, это необходимо для удобства проведения работ. В процессе заточки нужно продвигать цепь по шине, не забывая при этом каждый раз устанавливать тормоз в рабочее положение. Напильник следует держать перпендикулярно вертикальной плоскости шины под углом 90 градусов (Рис.3) и одновременно выдерживать угол в 30 градусов относительно перпендикулярной линии к линии шины (Рис.4_А). В большинстве своем на режущем зубе имеется сервисная метка. Она указывает направление заточки и предел до которого можно точить цепь (Рис.5). Заточка цепи производится движениями напильника изнутри зуба наружу.
Значительно упростить задачу помогут несложные приспособления. Для правильного угла заточки используют специальные шаблоны (Рис.6). Пример использования на Рис.7_А. Шину необходимо лишить ненужной подвижности. Для этого можно воспользоваться способом с подкладыванием между цепью и шиной штатного свечного ключа (Рис.7_В), либо воспользоваться струбциной (Рис.8).
Стачиваясь зуб как бы уходит виз. Это обусловлено конструкцией режущего зуба, задняя часть режущей полки ниже режущей ее части. Соответственно количество захватываемой древесины уменьшается, что существенно сказывается на производительности. За глубину реза отвечает ограничительный зуб (Рис.9). После заточки режущей части необходимо подточить и ограничительный зуб. Он должен быть утоплен на 0,65 мм. Для этого может пригодиться еще один шаблон (Рис.10) и плоский напильник (Рис.11). Приложив шаблон на цепь можно заметить выступающий ограничитель (Рис.12). Плоским напильником его следует спилить вровень с шаблоном (Рис.13).
(!!!) Работу по заточке цепи, нужно обязательно проводить с использованием перчаток из грубого материала. В противном случае можно достаточно легко себя травмировать, т.к. рабочая поверхность зубьев очень острая.
Углы заточки цепей подробно оговорены в предыдущей статье "Углы заточки пильных цепей", https://remont.tools.by/diagnostics/view/1652518345 Открыть в новой вкладке
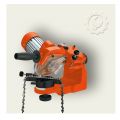 Рис.1 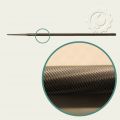 Рис.2 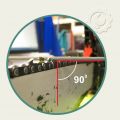 Рис.3 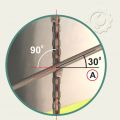 Рис.4 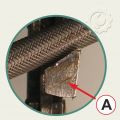 Рис.5 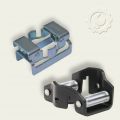 Рис.6 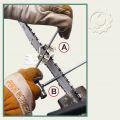 Рис.7 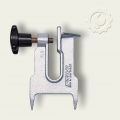 Рис.8 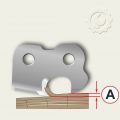 Рис.9 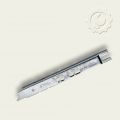 Рис.10 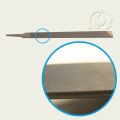 Рис.11 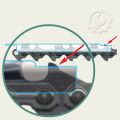 Рис.12 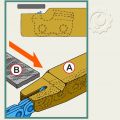 Рис.13
|
|
|
|