Уважаемые клиенты, с 01.01.2024г. мы прекращаем принимать инструменты BOSCH в платный ремонт
Типы изделий:
|
Диагностика и анализ неисправностей:
Повреждение зубчатой пары (Makita LS-1018) Развернуть ▼
|
Торцовочная пила Makita LS-1018 имеет своеобразную конструктивную особенность. Не редким обращением клиентов в СЦ связано с разрушением зубчатого соединения ротор-шестерня.
Вначале о конической передаче. При вращении под нагрузкой (Рис.1) на шестерни передачи действуют несколько сил, одна из которых направлена в противоположную сторону смыканию зубьев (Рис.1_В). В результате получается неполное зацепление зубьев, что неминуемо приводит к их повреждению (Рис.2).
В модели LS-1018, без закрепленной оснастки, шпиндель (Рис.3_А) вместе с шестерней (Рис.3_В) могут сместиться внутрь редуктора (Рис.3_С), тем самым провоцируя неполное зацепление зубьев передачи. Почему это происходит?
Данную модель пилы НЕЛЬЗЯ ВКЛЮЧАТЬ БЕЗ ОСНАСТКИ!!! У шпинделя с конической шестерней есть конструктивная возможность перемещаться в осевом направлении относительно внутренней обоймы подшипника (Рис.4_А). Внутренняя часть шпинделя вращается в подшипнике скольжения (бронзовая втулка). Там есть некоторый зазор по торцевой части. Под нагрузкой шестерня ротора отжимает коническую шестерню в сторону расцепления (Рис.4_В), провоцируя неполное зацепление зубьев с последующим их повреждением.
При установленной оснастке шпиндель с шестерней, через фланцы и диск (Рис.5_А) прижимается
винтом крепления (Рис.5_В) к подшипнику (Рис.5_С), тем самым предотвращая смещение его в сторону расцепления зубчатого соединения.
В противном случае имеется достаточно большой риск получить повреждение зубьев редуктора (Рис.6) Открыть в новой вкладке
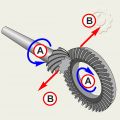 Рис.1 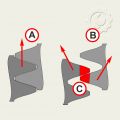 Рис.2 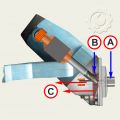 Рис.3 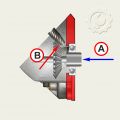 Рис.4 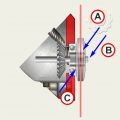 Рис.5 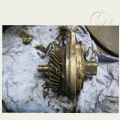 Рис.6
|
Протекает адаптер Развернуть ▼
|
Иногда появляются случаи с протеканием в районе адаптера в очистителях высокого давления у практически новых устройств. В частности это касается моделей ECO HPW-1770 и HPW-1860RSE. Замена адаптера на новый практически не помогает. Проблема в том, что подсоединенный к адаптеру шланг не до конца доходит до упора в адаптере. Шланг вроде как и зафиксировался, но неплотное соединение не позволяет обеспечить надежную герметизацию.
Есть вариант незначительной доработки. Достаточно просто подложить уплотнительное колечко в сам адаптор (Рис.1). На Рис.2 вид сверху и пунктирной линией показано где должно стоять кольцо. На Рис.3 вид в разрезе и место, куда укладывается кольцо.
Отдельно можно добавить, размер кольца внешний 20,7мм, внутренний 14,9мм, толщина 2,9мм. Идеально подходит от поршня перфоратора WORTEX RH-2629 (арт.AB26-41) или WORTEX CRH-1820 (арт.Z0A-ZP-20LI-26). Либо любое, подходящее по размеру. Открыть в новой вкладке
|
AV Engineering, конденсаторы в коробках управления Развернуть ▼
|
В скважинных насосах разных моделей AV Engineering используются фазосдвигающие конденсаторы, которые расположены в коробках управления. Номиналы их отличаются и зависят от того какой мощности используется двигатель. В самих коробках даны параметры двигателя и мощность указана в так называемых электрических лошадиных силах. В энергетике используется электрическая лошадиная сила равная 746 ватт. Ниже приведена таблица с переводом в более привычную систему измерения мощности в ваттах.
Слева внизу на картинках данные указанные на коробках. Справа внизу (красный цвет) перевод данных в ватты. И соответственно к каждому виду двигателя показаны номиналы конденсаторов. Открыть в новой вкладке
|
Заламывание поршневых колец Развернуть ▼
|
Обнаружились случаи заламывания поршневых колец. Это касается поршневых групп мотокос с диаметром цилиндра 40 мм. Причина неисправности в неточности изготовления поршней, а в частности нарушение посадочных размеров для замков поршневых колец. Как можно определить правильность размеров и вычислить заведомо неисправный поршень?
Для начала частично соберем поршень, поставим кольца и палец (стопорные кольца устанавливать не обязательно). Вставим поршень в цилиндр, выровняв по горизонтали, т.е. придадим ему рабочее положение (Рис.1). Во впускном окне будет хорошо видно неисправен поршень или нет (Рис.2). В неисправном поршне кольцо будет выпадать во впускное окно (Рис.3). На Рис.4 более укрупненный участок выпадения кольца.
На конкретном примере были проведены замеры неисправного поршня. С одной стороны замок был расположен относительно оси пальца на удалении 16,3 мм (Рис.5). С другой стороны расстояние между осью пальца и замка было 13,1 мм (Рис.6). Тот замок, у которого получилось большее удаление от оси пальца и выпадал во впускное окно. Впускное окно на Рис.5 и 6 обозначено красным цветом. При сравнении исправного поршня с неисправным заметно существенное смещение в положении замков (Рис.7).
Дополнительно усугубляет ситуацию фаска впускного окна со стороны стенок цилиндра. Само окно в ширину имеет размер в 23 мм, а края фаски 25 мм (Рис.8). Т.е. к тем неточностям в изготовлении поршней добавляется дополнительно по одному миллиметру на каждую сторону. В эту фаску и проваливается край кольца (Рис.9).
Такое явление можно рассмотреть на конкретном примере (Рис.10). Край кольца попадал в фаску, от чего стало образовываться затирание (показано красной стрелкой). На Рис.11 показан путь края кольца. По красной линии видно место заваливания кольца в фаску. На первом этапе работы двигателя заваливания может и не произойти. Но учитывая то, что место для замка поршневого кольца находится на грани фола, т.е. у самого края окна, все может закончится повреждением. Здесь хочется отметить еще один неприятный момент. Поршневое кольцо имеет некоторую осевую подвижность. Это обусловлено температурными требованиями, т.е. имеется необходимый температурный зазор, позволяющий кольцу перемещаться вдоль канавки. Добавим к этому небольшую выработку в процессе притирания ЦПГ, что несомненно увеличит эту подвижность (Рис.12). В результате получаем смещение кольца в сторону окна с возможным повреждением ЦПГ.
На Рис.13 показано такое перемещение по оси поршня. Для наглядности показано проворачивание поршня, кольца при этом находятся неподвижно. В действительности положение поршня ограничено шатуном, а кольца могут смещаться в пределах показанного люфта. На верхнем рисунке палец поршня параллелен цилиндру, на нижнем рисунке видно осевое проворачивание в пределах люфта по кольцам.
Бывают и другие случаи, когда кольцо попадает не во впускное окно, а в боковые, перепускные окна. Для начала следует обратить внимание на Рис.14. На нем видно как исполнен замок поршневых колец. Сам штифт замка, если смотреть на него в радиальном направлении, слишком глубоко посажен и в замковой части выступает лишь незначительная его часть. Выборка в поршневом кольце под штифт слишком большой и не соответствует диаметру самого штифта. Для лучшей наглядности на Рис.15 белой контурной линией показана эта проблема. В результате у поршневого кольца есть дополнительная степень свободы, позволяющая ему перемещаться в пределах канавки поршня, в конкретно взятом случае, на 2,3mm (Рис.16). По итогу видим такую картину (Рис.17).
Провели измерения, по итогу получили такие данные. Края между боковыми перепускными окнами расположены друг от друга на расстоянии 32mm (Рис.18_красные метки). Штифты по габаритным точкам имеют расстояние в 33mm (Рис.18_синие метки). Исходя из этих данных мы понимаем, что кольцо не будет обжато цилиндром по всему своему ходу. И как только попадет в зону перепускного окна, край его сразу зацепится за торцевую часть этого окна. Результат - обламывание кольца с повреждением ЦПГ (Рис.19). Открыть в новой вкладке
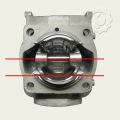 Рис.1 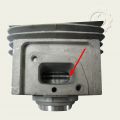 Рис.2 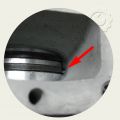 Рис.3 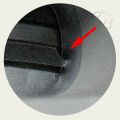 Рис.4 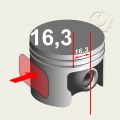 Рис.5 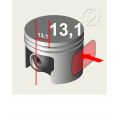 Рис.6 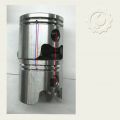 Рис.7  Рис.8 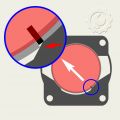 Рис.9 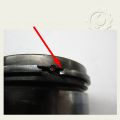 Рис.10 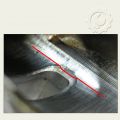 Рис.11 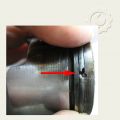 Рис.12 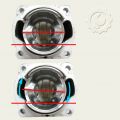 Рис.13 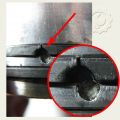 Рис.14 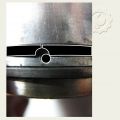 Рис.15 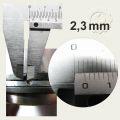 Рис.16  Рис.17 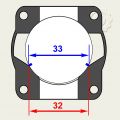 Рис.18 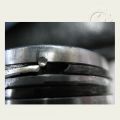 Рис.19
|
Прогар поршня Развернуть ▼
|
Иногда в ремонт потупают двигатели с прогоревшим поршнем. В чем может быть проблема? Есть две причины возникновения такого повреждения.
Бывают поршни прогоревшие по боковой стенке (Рис.1_А) и по днищу (Рис.1_В).
В первом случае причиной может быть некачественное масло в топливной смеси, слишком богатая смесь либо работа в режиме постоянной перегрузки двигателя. Т.е. причины, приводящие к закоксовыванию поршня с залеганием поршневых колец. В двигателях внутреннего сгорания предусмотрен температурный зазор поршня и поршневых колец. При работе двигателя поршень, переходя верхнюю мертвую точку, как бы переваливается в пределах теплового зазора(Рис.2). Образовавшийся зазор, компенсируют поршневые кольца, обеспечивая компрессию в камере сгорания (Рис.2_А). Если же кольца залегли, то в получившийся зазор прорывается газ от сгорания топливной смеси (Рис.3_А). В результате боковая стенка поршня получает мощный тепловой удар. Здесь сказывается большая скорость разогрева и слабое охлаждение поршня в этой зоне, т.к. находится со стороны выхода выхлопных газов. Повреждение поршня, как правило, имеет клиновидную форму (Рис.4_А). Края поврежденного участка имеет ярко выраженные следы оплавления.
Во втором случае это может быть детонация. В этом случае повреждения будут иметь вид механического повреждения и местом разрушения будет дно поршня (Рис.5). Т.е. по краям разлома будет видна кристаллическая структура металла без явных следов оплавления. Что такое детонация и чем она может быть вызвана?
Энциклопедическая формулировка: "Детонация — режим горения, при котором по веществу распространяется ударная волна, инициирующая химические реакции горения. Иногда формулируют как «сгорание во фронте ударной волны».
При нормальной работе двигателя скорость распространения фронта пламени в момент вспышки топлива обычно не более 50 м/сек. При детонации - скорость сгорания топлива происходит со сверхзвуковой скоростью и может превышать скорость звука в несколько раз (скорость звука 330 м/сек). При такой скорости горения появляется ударная волна с выделением большого количества тепла, что и приводит к разрушению поршня.
Основной причиной вызывающей детонацию является применение топлива с низкооктановым числом. Можно возразить, мол где сейчас можно найти низкооктановый бензин? Но тут есть нюанс. В основе любого бензина есть базовый бензин, который изначально получается после ректификации нефти. Он как правило имеет низкое октановое число и составляет около 65 ед. Есть и другие варианты с применением более современных технологий, но это все равно будет бензин с числом около 74-76 ед. Дальше вступают в процесс антидетонационные присадки. Эти присадки имеют свойство улетучиваться. Все зависит от условий хранения. Плюс к этому вы не можете знать насколько свежий бензин был на заправке. Более подробную информацию по этому вопросу можно найти в интернете. Можно только сказать следующее, при неблагоприятном стечении обстоятельств с условиями хранения можно через 3-4 недели получить низкооктановый бензин с выше сказанными неприятностями.
Похожие повреждения, такие как на Рис.5 могут случиться из-за калильного зажигания. Это и некачественный бензин с какими-нибудь особыми присадками и конечно свечи зажигания с неправильно подобранным калильным числом. На слишком "холодных" свечах может образовываться нагар, а слишком "горячие" могут способствовать калильному зажиганию. Т.е. вспышка топлива будет происходить раньше положенного времени, до выхода поршня в ВМТ.
Открыть в новой вкладке
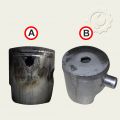 Рис.1 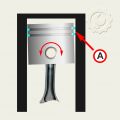 Рис.2 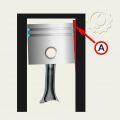 Рис.3 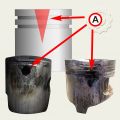 Рис.4 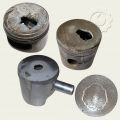 Рис.5
|
Подтекание масла (ASILAK__FERMER) Развернуть ▼
|
Причина частого обращения клиентов с жалобой на подтекание масла из корпуса редуктора в некоторых моделях культиваторов ASILAK и FERMER, является некачественная сварка узлов культиватора.
Редуктор культиватора ASILAK__FM-811MX несколько отличается от предыдущих моделей. Заливная пробка стала выше по уровню. Если в предыдущих моделях заливная пробка под масло располагалась в районе (Рис.1_А), то в FM-811MX она расположена значительно выше (Рис.1_В). Это позволяет пользователю заливать больше масла. В результате появляется возможность выброса масла в верхнюю часть кронштейна рукоятки. К кронштейну приварена пластина крепления механизма переключения передач (Рис.2).
Сварной шов этой пластины оставляет желать лучшего и часто из-под сварки выступают излишки масла, которые негативно влияют на реакцию пользователя. Сразу возникает вопрос об исправности культиватора.
Есть простой способ избавиться от подтеканий масла. Проблемную зону следует очистить от краски, обработать поверхность немного углубив место протекания (сверло, фреза, бормашинка) для лучшего сцепления герметизирующего состава. Затем "холодной сваркой" заделать обработанную поверхность (Рис.4). В конце доработки желательно восстановить покраску изделия (Рис.5). Открыть в новой вкладке
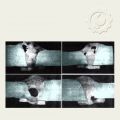 Рис.1 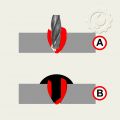 Рис.3  Рис.4 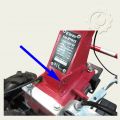 Рис.5 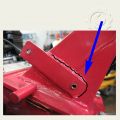 Рис.6 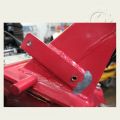 Рис.7 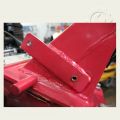 Рис.8
|
Заклинивание шатуна (ошибки при запуске) Развернуть ▼
|
При первом запуске компрессора надо понимать, что масла в большинстве моделей в картере нет. Об этом сигнализирует стикер, наклеенный на кнопку прессостата (Рис.1). Нередко на это некоторые не обращают внимание и ориентируются на окошко уровня масла. Об этом подробнее.
При большой разнообразности конструкций крышек картера (Рис.2) все они имеют схожее конструктивное решение по креплению смотрового окошка через резьбовой канал. Если смотреть на крышку картера изнутри (Рис.3), то можно заменить что этот канал имеет некоторую полость (показано красными стрелками) в которую попадает масло и там удерживается некоторое время. Это обусловлено коэффициентом поверхностного натяжения масла, что может ввести в заблуждение наблюдающего (Рис.4). Для проверки работоспособности устройства на заводе изготовителе заливается масло и после проверки сливается. Некоторое его количество остается в картере, это может быть где-то около 50 мл. Это скопившееся в окошке масло порой и вводит в заблуждение пользователя.
Иногда при продаже изделия продавец, ускоряя процесс продажи, не устанавливает колеса на компрессор. Если такой компрессор установить на ровную поверхность, то мы заметим большой уклон в сторону смотрового окошка (Рис.5) и уровень масла будет обманчивым (Рис.5_А).
Перед первым пуском необходимо соблюдать несложные правила. Установить колеса (Рис.6) или обеспечить нужный уровень, подложив под кронштейны колес какой-нибудь упор нужной высоты. Наклонить компрессор окошком вверх, с тем что бы слить остатки масла. Поставить обратно компрессор по уровню, убедиться по окошку в достаточном количестве масла (уровень должен находиться по середине окошка). При недостаточном количестве долить.
И напоследок о диагностике.
Случай при котором устройство пришло в ремонт с прихваченным шатуном и масло в картере присутствует в полном объеме. Порой бывает такое, что пользователь понял в чем его ошибка и желая скрыть истинную причину неисправности, постфактум доливает масло. Как определить подлог. Если заклинивание шатуна произошло с маслом (заводской дефект), то в нем будет присутствовать алюминиевая пыль и прочие продукты от трения. Алюминиевую пыль легко обнаружить подсветив масло фонариком или на ярком свету (будут заметны блестки). Если масло чистое, можно с большой долей вероятности утверждать, что оно не работало и залито было позднее. Открыть в новой вкладке
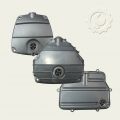 Рис.1 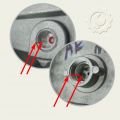 Рис.2 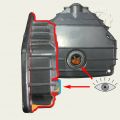 Рис.3 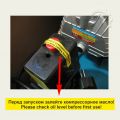 Рис.4 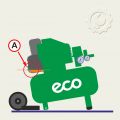 Рис.5 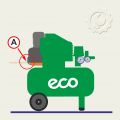 Рис.6
|
Стартер ErgoStart принцип работы Развернуть ▼
|
Стартера с обычной системой и системой ErgoStart принципиально отличаются друг от друга не только конструктивным исполнением, но и приемом запуска двигателя. Очень часто в устройствах, где используется система ErgoStart, клиенты зачастую совершают одну и ту же ошибку, пытаясь применять приемы запуска как с обычными стартерами. Разберем подробнее.
ErgoStart - это запатентованная в 2003 году инновационная технология компании STIHL. Подобная технология значительно облегчает запуск двигателя и не требует от оператора необходимость дергать за ручку стартера. Как это работает? Между стартерной катушкой и коленчатым валом размещена пружина с двумя поводками (Рис.1_А), которая натягивается при плавном вытягивании тросика. В камере сгорания находится воздух, который сжимаясь на каком-то этапе препятствует проворачиванию коленвала. Пружина, сжимаясь, аккумулирует энергию пружины (Рис.2_А). Затем, в какой-то момент усилие пружины преодолевает сопротивление воздушной подушки в камере сгорания и вся энергия, накопленная пружиной, одномоментно передается на коленвал, запуская двигатель (Рис.3). Этим предотвращаются повышенные нагрузки, которые возникают при рывках. Пружина передает коленчатому валу энергию, конвертирует ее в движение, чем обеспечивает правильный безопасный запуск мотора. Оператору нужно всего лишь потянуть за тросик без резких рывков и больших усилий.
На Рис.4 показан сравнительный график запуска двигателя обычным стартером и стартером ErgoStart. График взят с официального сайта компании STIHL. Вертикальные столбцы - это количество тактов двигателя при вытягивании троса стартера. Как видно из графика при вытягивании троса с обычным стартером происходят рывки на каждом такте двигателя, что и передается на руку оператора, вынуждая его прилагать дополнительные усилия в виде резкого дергания на рукоятку стартера. С ErgoStart-ом это не происходит. Оператор плавно вытягивает трос и в какой-то момент происходит запуск двигателя.
Клиенту, который не знакомом с подобной конструкцией, следует объяснить что дергать за рукоятку стартера не только необязательно, но даже вредно для конструкции. Иногда по этой причине происходили поломки в виде повреждения пружины.
Открыть в новой вкладке
|
Доработка заглушки в садовых насосах Развернуть ▼
|
Корпуса насоса в насосных станциях и садовых насосах взаимозаменяемые. Отличие заключается в том, что в насосных станциях присутствует рессиверный баллон (Рис.1_А), а в садовых насосах его нет. В варианте с использованием корпуса в садовом насосе будет отсутствовать трубка соединяющая рессиверный баллон и корпус насоса (Рис.1_В). А отверстие необходимо будет заглушить пробкой с резьбой 1/2 дюйма (Рис.2). В заглушке есть уплотнительное кольцо (Рис.3). И все бы могло решиться просто, но есть небольшой нюанс.
Корпус изначально не был рассчитан на использование заглушки. Торцевая поверхность резьбовово отверстия, куда мы собираемся вкрутить заглушку, имеет корявую поверхность от литья, что не способствует хорошему прилеганию уплотнения и не имеет углубления под уплотнительное кольцо. В результате, после закручивания заглушки, уплотнение просто выползает из-под гайки наружу (Рис.4). Необходимо предусмотреть углубление ввиде фаски, что бы уплотнительное кольцо при закручивании оставалось в этом углублении.
Для операции по снятию фаски мы использовали конусное сверло (Рис.5). По итогу получилась вполне удовлетворительная фаска. Углубление фаски должно быть примерно на толщину уплотнительного кольца. При закручивании заглушки, кольцо внутри уплотниться и надежно перекроет выход давления наружу (Рис.6). Открыть в новой вкладке
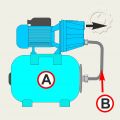 Рис.1 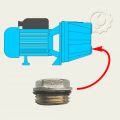 Рис.2 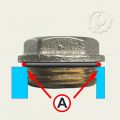 Рис.3 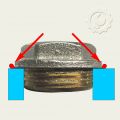 Рис.4 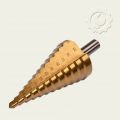 Рис.5 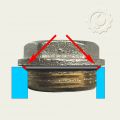 Рис.6
|
Задир ЦПГ, наиболее вероятные причины Развернуть ▼
|
Предварительная оценка повреждений - очень важный этап диагностики. Ошибочное предварительное мнение может сыграть ключевую роль в дальнейшей оценке причин неисправности. Механик может пойти по ложному пути рассуждений и в дальнейшем, подводя под свою первичную оценку, объяснять почему эти повреждения произошли, подтасовывая факты. Человек делает это не осознанно, просто в силу своих убеждений.
Перед нами двигатель с тепловым задиром ЦПГ. По характеру задира на поршне можно определить причины по которым произошло повреждение. Подача топлива и его сгорание происходит от впускного окна (Рис.1_А) до выпускного (Рис.1_В). Следовательно та часть поршня, которая находится к впускному окну всегда будет холоднее чем та, которое направлена к выпускному окну (Рис.2). Через впускное окно постоянно подается топливо, охлаждая эту часть поршня (Рис.2_А). После вспышки, отработанные горячие газы выбрасываются в выпускное окно, разогревая эту часть поршня (Рис.2_В).
Если двигатель перегревается и выходит за температурные расчетные нормы, то происходит локальный срыв масляной пленки и как результат задир. В случаях перегрева задир начинается с самой горячей точки - выпускное окно (почему, говорилось выше). Если вы увидели локальный задир со стороны глушителя (Рис.3), то однозначно это тепловой задир. Задир по перегреву можно получить двумя способами. Ограничить охлаждение двигателя и бедная смесь. На тему бедной смеси есть сопутствующая статья на сайте "Кратко о двухтактных двигателях" http://remont.tools.by/diagnostics/view/1551959975. Отсутствие охлаждения двигателя может быть в случаях когда ребра цилиндра покрыты теплоизолирующей грязью или как в случаях с бензорезами гудроном (при резке асфальта).
Если есть такой же локальный задир со стороны впускного окна (Рис.4) это может свидетельствовать о том, что работали с грязным воздушным фильтром или вовсе без него. Посторонние частицы через впускное окно попадали в камеру сгорания, по пути повреждая поршень на входе.
Если же задир по всей окружности поршня и поршень при этом не имеет замасляности (сухой), это отсутствие смазывающего материала в топливе. Здесь задир начинается со стороны выпуска (Рис.5) и почти сразу распространяется по всей поверхности (Рис.6) как только поршень начнет расширяться и выбирать тепловые зазоры.
Остальные случаи можно отнести к визуально понятным, Рис.7 - обламывание стопорного или поршневого кольца, разрушение сепаратора подшипника коленвала либо попадание постороннего предмета через впускное окно. Здесь надо смотреть по обстоятельствам и внимательно осмотреть картер на наличие осколков и идентификации их. На Рис.8 - разрушение подшипника и характерные вмятины от его шариков. Открыть в новой вкладке
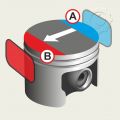 Рис.1 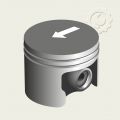 Рис.2 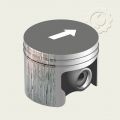 Рис.3 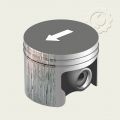 Рис.4 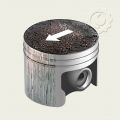 Рис.5 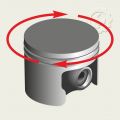 Рис.6 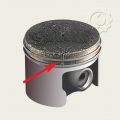 Рис.7 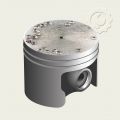 Рис.8
|
Некомплект GS-232 _ GS-282 Развернуть ▼
|
Обнаружены случаи некомплекта в бензопилах моделей GS-232 и GS-282. Отсутствует крепление воздушного фильтра.
В предыдущих моделях бензопил, таких как GS-231, GS-281 и пр., крепление воздушного фильтра осуществлялась внешней гайкой через прижатие крышкой фильтра (Рис.1_А). В моделях GS-232 и GS-282 крепление фильтра реализовано отдельным креплением ввиде барашкового винта и расположен он под крышкой фильтра (Рис.1_В).
Воздушный фильтр крепится барашковым винтом через шайбу (Рис.2). Вот их-то порой и нет в комплекте. Фильтр просто насажен на крепежную шпильку. Так же иногда отсутствует и прокладка между воздушным фильтром и корпусом (Рис.3). Барашковый винт с резьбой М5 и шайба в внутренним отверстием 5мм (Рис.4).
Возможно кому-то пригодятся размеры прокладки. В случае безвыходной ситуации, когда есть желание изготовить из подходящей резины. (Рис.5_А) размеры прокладки с указанием диаметров отверстий. (Рис.5_В) координатные размеры межосевых расстояний отверстий. Открыть в новой вкладке
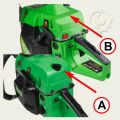 Рис.1 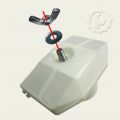 Рис.2 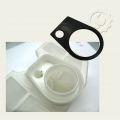 Рис.3 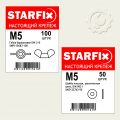 Рис.4 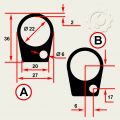 Рис.5
|
Демонтаж крыльчатки AV Engineering ENERGY-II-2700 Развернуть ▼
|
Возможно некоторые механики сталкивались с проблемой демонтажа крыльчатки. Если внимательно присмотреться, то будут заметны 2 резьбовых отверстия (Рис.1). Они-то и являются конструктивными элементами для демонтажа крыльчатки. Достаточно вкрутить два винта М4 и поочередно закручавая (Рис.2), стянуть крыльчатку. Винты должны быть длиной около 30-40мм. При вкручивании они упираются в корпус и повредить сальник не могут. Открыть в новой вкладке
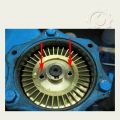 Рис.1 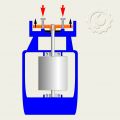 Рис.2
|
Углы заточки пильных цепей Развернуть ▼
|
Остро заточенная цепь обеспечивает эффективную, безопасную и точную работу цепной пилы. В этой статье речь об углах заточки.
Вначале о конструктивном исполнении режущего звена пильной цепи. Режущий зуб состоит из основания зуба (Рис.1_1), лопатки зуба (Рис.1_2), ограничителя глубины реза (Рис.1_3). Лопатка имеет вертикально расположенное торцевое лезвие (Рис.1_4) и спадающее подуглом назад верхнее лезвие (Рис.1_5), расположенное горизонтально.
В вертикальном направлении по срезу зуб (Рис.2_В) погружается на глубину до ограничителя (Рис.2_А). В горизонтальном направлении (Рис.3) дерево срезается боковой (вертикальной) частью зуба. Все режущие кромки должны иметь правильные углы заточки. От правильно заточенной цепи зависит не только точность выполняемой работы, но и значительно уменьшает нагрузку на двигатель.
Задний угол верхнего лезвия (наклон)(Рис.4). Спадающая под углом назад спинка зуба образует задний угол верхнего лезвия. Этот угол необходим для врезания верхнего лезвия в древесину и определен заводом изготовителем.
Задний угол торцевого лезвия (Рис.5). Суживающаяся назад лопатка зуба образует задний угол торцевого лезвия. Угол служит для бокового обрезания стружки и препятствует прихватыванию шины в дереве. Этот угол также остается неизменным и заточке не подлежит.
Передний угол (Рис.6). Кромка торцевого лезвия образует с поверхностью скольжения режущего зуба передний угол. В основной массе цепей этот угол составляет 85 градусов. Исключением являются специальные цепи - с победитовыми напайками (Rapid Duro) 65 градусов и для продольной распиловки 80 градусов.
Задний угол верхнего лезвия (скос)(Рис.7). Этот угол наиболее важен. Он должен быть, в зависимости от типа цепи, от 50 до 60 градусов, но специально его определять при заточке нет необходимости. При соблюдении остальных предписанных величин он должен получиться автоматически.
Угол заточки в плане (угол верхней кромки)(Рис.8). Угол заточки или угол в плане (вид сверху) получается измерением от верхней режущей кромки под прямым углом к направляющей шине цепи. В основной массе цепей этот угол составляет 30 градусов. Исключением являются цепи с победитовыми напайками (типа Rapid Duro) - 25 градусов и для продольной распиловки 10 градусов.
Расстояние ограничителя глубины (Рис.9). В большинстве используемых цепей этот размер равен 0,65 мм. Это цепи с шагом 1/4; 3/8; .325; Для цепей с шагом .404 требуется больший размер для ограничителя - 0,8 мм.
Кратко основные размеры:
* передний угол (Рис.6) - 85 градусов
* угол в плане (Рис.8) - 30 градусов
* ограничитель глубины (Рис.9) - 0,65 мм
Открыть в новой вкладке
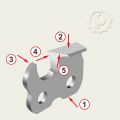 Рис.1 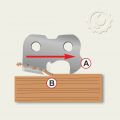 Рис.2 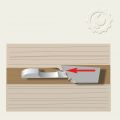 Рис.3 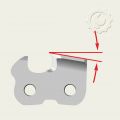 Рис.4 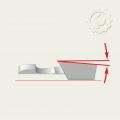 Рис.5 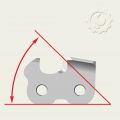 Рис.6 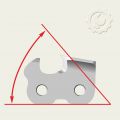 Рис.7 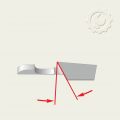 Рис.8 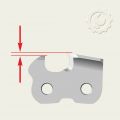 Рис.9
|
Травит воздух Развернуть ▼
|
Такая неисправность как травит воздух в районе прессостата (Рис.1_А) не всегда связана с неисправностью самого прессостата. Проблема может быть в обратном и разгрузочном плапанах. Как разобраться который из них некорректно работает?
На Рис.2 показаны магистрали, которые нас интересуют на данный момент. Красная магистраль (Рис.2_А) от поршневой группы к рессиверному баллону, синяя магистраль (Рис.2_С) связана с разгрузочным клапаном (в данном примере клапан расположен на прессостате), а черным (Рис.2_В) обозначена электрическая цепь управления работой электродвигателем.
В процессе работы компрессора (Рис.3), воздух от поршневой группы закачивается в рессиверный баллон. При этом разгрузочный клапан (Рис.4_А) должен быть закрыт, а обратный клапан (Рис.4_В) открыт.
Как только компрессор достигнет установленного максимального давления, прессостат подаст команду на отключение электродвигателя (Рис.5_А). Обратный клапан, при этом, закроется, препятствуя выходу воздуха из рессиверного баллона в поршневую группу. Одновременно с этим должен сработать разгрузочный клапан (Рис.5_В) для сброса лишнего давления в нагнетающей магистрали. Это предусмотренно для того, что бы поршневая группа не испытывала нагрузку при следующем запуске двигателя. При старте электродвигатель имеет слабый крутящий момент и его может не хватить для преодоления дополнительной нагрузки ввиде избыточного давления в магистрали.
Теперь о том как определить какой из двух клапанов ведет себя некорректно? Если при работающем компрессоре происходит стравливание воздуха, но при отключении стравливание прекращается, то проблема в разгрузочном клапане (Рис.6_А). Возможно он подклинил по какой-то причине. Если же стравливание продолжается и при отключениии компрессора, то проблема в обратном клапане (Рис.6_В). В этом случае воздух через неработающий обратный клапан поступает в магистраль и через разгрузочный клапан, который в данном случае должен быть открыт, выходит наружу.
Открыть в новой вкладке
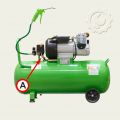 Рис.1 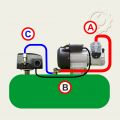 Рис.2 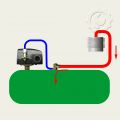 Рис.3  Рис.4 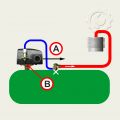 Рис.5 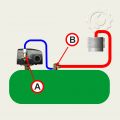 Рис.6
|
Притирание тормозной ленты (Вариант 1) Развернуть ▼
|
Притирание тормозной ленты о цепной барабан может происходить по двум причинам - это дефект крышки тормоза цепи и дефект самой тормозной ленты. Первая причина изложена в этой статье.
Неисправность, о которой пойдет речь, в последнее время приняло довольно массовый характер. У новых пил в большом количестве присутствует такой дефект как притирание тормозной ленты о цепной барабан. Причина - некачественное изготовление корпуса крышки тормоза цепи (Рис.1). Замена на новую крышку не помогает, на складе запчасти с таким же дефектом.
Притирание происходит по нижней части ленты (Рис.2). Если посмотреть внимательно на внутреннюю часть крышки, то заметим что уложеная тормозная лента в отпущенном состоянии не укладывается в окружность, а образует некоторый эллипс. Рис.3_А - фактическое положение ленты. Рис.3_В окружность, в которой теоретически должна находиться тормозная лента. В результате такого положения ленты, происходит ее притирание к цепному барабану (Рис.4_белая стрелка). Нижняя опора тормозной ленты, что является частью корпуса, не дает ленте лежать по окружности. Т.е. корпус выполнен с конструктивным дефектом геометрии.
Случай относится к гарантийным и изделие нуждается в замене, т.к. новые крышки имеют такой же дефект.
Негативные последствия такого притирания тормозной ленты о барабан на Рис.6. Начальная стадия оплавления (Рис.6_А), лента сдвинута для наглядности. Фатальное оплавление (Рис.6_В), тормозная лента снята.
P.S. Можно предложить вариант исправления дефекта путем удаления части корпуса (опорная нижняя часть под тормозную ленту) - Рис.5 Открыть в новой вкладке
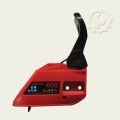 Рис.1 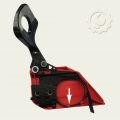 Рис.2 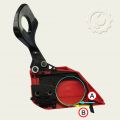 Рис.3  Рис.4 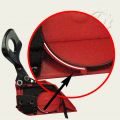 Рис.5 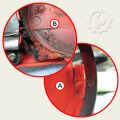 Рис.6
|
Притирание тормозной ленты (Вариант 2) Развернуть ▼
|
Второй вариант притирания тормозной цепи к цепному барабану отличается от предыдущего тем, что в данном случае неисправность касается не дефектного корпуса, а самой тормозной ленты.
В тормозную расстопоренную ленту должна вписываться окружность цепного барабана без какого-либо касания (Рис.1). В исправной крышке тормоза цепи лента лежит ровно и опирается на все ограничители корпуса крышки (Рис.2). Дефект можно обнаружить по опоре (Рис.3). На этом рисунке лента прилегает к опоре, что свидетельствует об исправном устройстве.
Если инструмент с дефектом, то лента, в этом месте, не будет прилегать (Рис.4). На Рис.5 показано в укрупненном плане, где хорошо заметен довольно большой зазор.
Причиной такой неисправности является плохая повторяемость при изготовлении тормозных лент. Как выяснилось, они имеют разную длину. При замерах лент (Рис.6) от точки (А) до точки (В) получались разные результаты.
Решить данную проблему можно заменив ленту на заведомо исправную. Открыть в новой вкладке
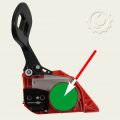 Рис.1 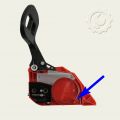 Рис.2 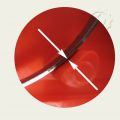 Рис.3 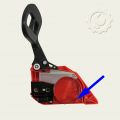 Рис.4 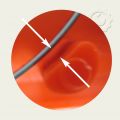 Рис.5 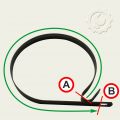 Рис.6
|
Схема электрическая ЕСО_ ОН-15, ОН-30, ОН50 Развернуть ▼
|
Электрическая схема теплогенераторов ЕСО моделей ОН-15, ОН-30, ОН-50.
На Рис.1 электронный модуль, на котором три подключаемых разъема. Обозначены как А1, А2 и А3.
Номера контактов начинаются от единицы, отмеченные цифрой (1). Счет идет порядно, не по кругу.
На Рис.2 наспиновка разъема (А1). Контакты (4) и (10) не задействованы. Снизу таблицы подписаны цвета проводов в оригинальном исполнении. На схеме провода раскрашены условно для простоты восприятия.
На Рис.3 приборы, подлючаемые к разъему (А2). Индикатор, подключенный к контактам (4), (5), представляет собой светодиод красного цвета и находится внутри теплогенератора. Обычно он примотан к жгуту.
На Рис.4 панель управления. В нижней части схемы его внешний вид и выходящие провода по цветам. Вверхней части схемы распиновка этих проводов в разъеме (А3). Открыть в новой вкладке
|
Сопротивление обмоток статора компрессоров (таблица) Развернуть ▼
|
Сводная таблица сопротивлений пусковой и рабочей обмоток статора и пусковых конденсаторов.
Сопротивления обмоток указаны с учетом сопротивления щупов тестера (0,4-0,5 Ом).
По мере поступления в ремонт новых моделей компрессоров таплица будет обновляться. Открыть в новой вкладке
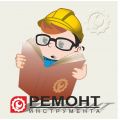 ЛОГО 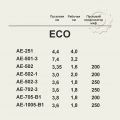 Рис. 1 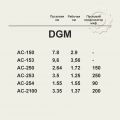 Рис. 2 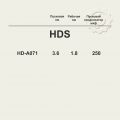 Рис. 3
|
Индикатор срабатывания момента затяжки (разрушение) Развернуть ▼
|
Динамометрический ключ как измерительный инструмент момента затяжки резьбовых соединений (Рис.1). Этот инструмент только так и следует рассматривать. Ни для каких срывов болтов и откручивания "укорчевшего" крепежа он не предназначен. Более того, такие операции зачастую могут привести к поломке инструмента. Один из таких случаев в этой статье.
Устройство такого ключа представлено на Рис.2. Из рисунка понятно как работает механизм срабатывания сигнала при достижении нужного крутящего момента. Вращающаяся по резьбе рукоятка, опирающаяся на цилиндр. Далее идет опорный подшипник, обеспечивающий плавное вращение рукоятки. Следом идут два калиброванных цилиндрика, которые опираются на пружину. После пружины расположен шарнирный механизм. Он и является индикатором предустановленного крутящего момента.
По достижении предустановленного значения (данные видны в окошке на ручке) раздается щелчок. Это сработал шарнирный механизм, говорящий о том, что значение достигнуто. Вращая рукоятку, мы сжимаем пружину, усиливая нагрузку на шарнирный механизм. Этим мы задаем нужное значение крутящего момента, которе хотим проверить.
Теперь о срабатывании механизма. На Рис.3 в верхней части, начальное состояние механизма. Часть (В), под действием пружины, через шарнирное соединение (синяя стрелка), прижимается к части (А). Часть (А) это часть ключа относящаяся к трещоточному механизму. Закручивая гайку, создается боковое усилие (красная стрелка). Обе части механизма начинают перемещаться между собой, показанный на схеме синей стрелкой, преодолевая специальный выступ. В какой-то момент проискодит соскакивание части (А) с этого выступа и механизм как бы "переламывается" (Рис.3_нижняя часть рисунка). При этом раздается щелчок (Рис.3_С), что говорит о том, что предустановленное значение достигнуто.
Если проигнорировать этот момент срабатывания индикатора, или намеренно, или не услышав и продолжить прилагать усилие на рычаг ключа, то этот механизм может быть поврежден. Особенно это касается ключей с большими моментами затяжек, т.к. рычаг этих ключей довольно внушительный. Длина рычага таких ключей порой бывает больше метра. Усилия одного человека вполне достаточно, чтобы сломать такой механизм.
Как правило ломается та часть, которая расположена со стороны трещотки (Рис.4_А). Красной линией показано наиболее вероятное место разрушения рычага. В низней части рисунка 4 показан момент после срабатывания механизма, т.е. после щелчка (Рис.4_В). При этом остается зазор между трубой ключа и рычагом механизма индикации (Рис.4_С). Иными словами есть куда "душить" ключ дальше и как результат... "легким" движением руки ключ превращается в неисправный инструмент (Рис.5).
Очень часто, при такой поломке, можно наблюдать дополнительные признаки превышения нагрузок. Это изгиб трубы самого ключа. На Рис.6 показано место, в котором обычно происходит такой изгиб (красная точка на нижней части рисунка). Проверить это можно, приложив уголок к этому месту. В этом месте обычно находится резиновая заглушка под наклейкой. Перед измерением надо аккуратно снять наклейку и вытащить заглушку, т.к. она будет мешать замеру. Затем приложив уголок (Рис.6_верхняя часть рисунка), попеременно нажимая по краям уголка (красные стрелки) мы сможем обнаружить "перекатывание" как на весах. Место, вокруг которого происходит перекатывание и будет местом изгиба трубы ключа.
Данный случай относится к негарантийным и расценивается как превышение допустимой нагрузки на инструмент.
Открыть в новой вкладке
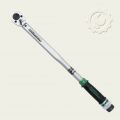 Рис.1 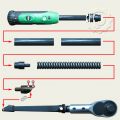 Рис.2 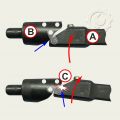 Рис.3 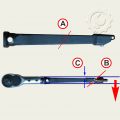 Рис.4 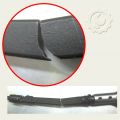 Рис.5 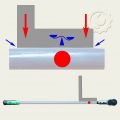 Рис.6
|
Датчик масла, проверка работоспособности (культиваторы, мотопомпы) Развернуть ▼
|
Речь идет о малых 4-х тактных двигателях, используемых в малой сельхозтехнике. Культиваторах, бензогенераторах, мотопомпах и пр. (Рис.1). Прежде чем приступать к диагностике необходимо проверить уровень масла в картере двигателя. Масло должно быть залито по самую горловину. Иногда на двигателе имеется сервисная картинка на которой указан уровень заливки масла (Рис.2). В данной статье описывается ситуация когда двигатель либо не заводится, либо заводится и глохнет. Здесь описан способ как быстро определить неисправность.
Система, которая может влиять на выключение двигателя состоит из 3-х узлов. Это датчик масла (Рис.3,А), электронный блок (Рис.3,В) и выключатель (Рис.3,С). Отдельно по каждой детали.
Выключатель (Рис.4) нормально разомкнутый, при переключении в положение OFF замыкает искру от модуля зажигания на корпус двигателя.
Электронный модуль (Рис.5) так же обрывает искру, но в случае если появится хотя бы одно замыкание искры на корпус. Этот сигнал поступает от датчика масла. Т.е. электронный модуль работает как триггер. Это нужно для того, чтобы исключить неустойчивое, пограничное состояние, когда масла мало и датчик то замыкается на корпус, то опять возвращается в исходное состояние.
И наконец сам датчик масла (Рис.6). Его принцип работы несложно проследить по картинке (Рис7). В датчике реализованы две электрические цепи. Через болт крепления (Рис.7,1) образуется цепь, связанная с корпусом двигателя (оранжевая цепь). В поплавке (желтый) находится стержень, который через скользящий контакт соединен с проводом (красная цепь). При нормальном уровне масла цепи красная и оранжевая разомкнуты (Рис.7,А) - искра от модуля зажигания поступает на свечу. Если уровень масла ниже нормы цепи замыкаются (Рис.7,В). Стержень касается пластины и искра замыкается на корпус (двигатель глохнет).
Типовая схема Рис.8,1, где "С" выключатель, "В" электронный модуль, "А" датчик масла. Сразу исключаем из схемы выключатель просто отсоединив разъем. Мультиметром прозваниваем выключатель в положении ON, на корпус. Если прозванивается - неисправен выключатель. Также поступаем с датчиком масла. отсоединяем разъем и прозваниваем на корпус, если прозванивается - неисправен датчик масла, "завис" в нижнем положении, замкнувшись на корпус.
Если все нормально, двигаемся дальше. Возвращаем контакт выключателя на место и исключаем из схемы электронный блок (Рис.8,2). Отключаем электронный блок (Рис.8,В) и перебрасываем контакт на выход выключателя (красная линия). Запускаем двигатель. Если двигатель работает устойчиво, без перебоев - неисправен электронный блок. Если двигатель работает с перебоями и как бы "чихает" - неисправен датчик масла. Такая неисправность больше проявляется на "холодном" двигателе. В горячем масле поплавок датчика может работать вполне прилично, но стоит двигателю остыть, как датчик начинает "заедать" и неуверенно себя вести, периодически касаясь контактной пластины связанной с корпусом двигателя.
И в заключение. Обязательно выставить обороты двигателя. Особенно это касается мотопомп ECO серии WP. Часто на заводе обороты двигателя не проверяются и приходят с завышенными показателями, как результат повреждение ЦПГ, обрыв шатуна. Винт максимальных оборотов находится под корпусом фильтра (Рис.9, красная стрелка). Обороты должны быть 3600 об/мин. Винт холостого хода находится на самом карбюраторе (Рис.10, красная стрелка). Обороты холостого хода двигателя 1600 об/мин. Открыть в новой вкладке
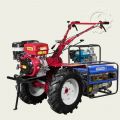 Рис.1 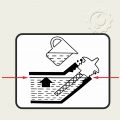 Рис.2 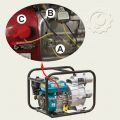 Рис.3 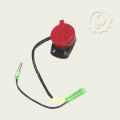 Рис.4 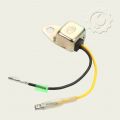 Рис.5 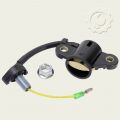 Рис.6 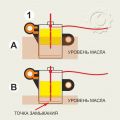 Рис.7 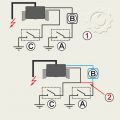 Рис.8 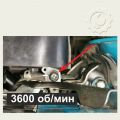 Рис.9 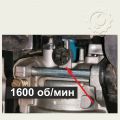 Рис.10
|
Определение момента затяжки (Пневмогайковерт) Развернуть ▼
|
Как определить момент затяжки после закручивания пневмо-ударным гайковертом (Рис.1)? Можно предложить один из вариантов проверки. Он прост и не требует дорогостоящего, специального оборудования.
Для этой процедуры нам понадобится динамометрический ключ с функцией контроля момента затяжки. Т.е. ключ со шкалой отображения момента затяжки. На рынке представлено большое количество подобного инструмента как электронные, так и механические (Рис.2). В нашем случае сгодится в любом исполнении.
Суть проверки проста. Закручиваем гайку ударным гайковертом (Рис.3_А). Затем тонким маркером ставим метку на гайке и на прилегающей поверхности (Рис.3_В). Откручиваем гайку и закручиваем ее уже с использованием динамометрического ключа, совмещая метки (Рис.3_С). В тот момент, когда совместятся метки, показания на шкале ключа будут соответствовать данным момента затяжки. Это мы говорим о моменте затяжки, который обеспечил наш ударный гайковерт, т.е. проверили с каким усилием гайковерт может максимально создать крутящий момент.
Если надо проверить соответствуют ли данные гайковерта с паспортными данными, то проверку стоит произвести несколько иначе, в обратном порядке (Рис.4). Сначала выставляем необходимый момент затяжки на динамометрическом ключе и закручиваем гайку до сигнала на ключе (Рис.4_А). Т.е. мы закрутили гайку с таким моментом затяжки, который прописан в паспорте к гайковерту. Ставим метку, как и в предыдущем случае, на гайке и на прилегающей поверхности (Рис.4_В). Откручиваем и гайковертом пытаемся опять закрутить гайку (Рис.4_С). Если метки совместились, то данные гайковерта соответствуют паспортным характеристикам. Если метки не совместились, т.е. не дотянули друг до друга, то это может говорить о том, что данные гайковерта несколько завышены в паспортном описании.
Но такое понятие как соответствуют ли полученные данные с теми, которее указаны в паспорте к инструменту, следует отдельно оговорить.
Например в паспорте к гайковерту присутствуют такие данные:
Максимальное рабочее давление - 6,3 бар
Расход воздуха - 200-400 л/мин
Число оборотов холостого хода - 7000 об/мин
Максимальный крутящий момент - 569 Н/м
Рекомендуемый диаметр воздушного шланга - Ø 9 мм
Т.е. максимальный крутящий момент будет достигнут только в том случае, если будут соблюдены все вышеперечисленные условия. Замечу, все без исключения! Часто бывает так, что клиент заявляет, мол компрессор обеспечивает нужное давление и шланг у него соответствующего диаметра, но гайковерт не обеспечивает нужный момент затяжки. Т.е. не так как сказано в паспорте.
Тут надо понимать что данные, указанные в паспорте, получены при соблюдении идеальных условий тестирования на заводе. Момент затяжки указан как ударный момент в короткий промежуток времени, который распределяется на количество ударов. Более подробно о силе удара описывалось в статье https://remont.tools.by/diagnostics/view/1619718745. В конце статьи было отмечено что усилие с которой будет закручена гайка или болт зависит от суммарной величины ударов - ∑=(m*v²/2)*n, где n количество ударов. Т.е. сила закручивания будет увеличиваться с количеством ударов.
Конечно, не все СЦ могут обеспечить все условия для тестирования подобного инструмента. В таких случаях можно прибегнуть к сравнительному анализу. Т.е. сравнить с новым, заведемо исправным инструментом.
В таких (спорных с клиентом) случаях выписывается акт диагностики с предлагаемой формулировкой:
"На данный момент СЦ не имеет технической возможности для измерения пиковых значений моментов затяжки данного инструмента. Опираясь на сравнительный анализ подобных изделий, диагностика показала, что технически инструмент исправен и работает аналогично таким же изделиям, которые не были в эксплуатации." Открыть в новой вкладке
|
Проскакивает оснастка, срабатывает муфта, треск в редукторе Развернуть ▼
|
Заявление клиента на неисправность: «При незначительной нагрузке слышен характерный треск и не вращается оснастка».
Причиной таких жалоб является срабатывание предохранительных узлов, которые предназначены для фиксирования оснастки с редукторным механизмом. Предохранительные механизмы, в таких устройствах как перфоратор, шуруповерт и им подобные, предназначены для безопасности оператора. Иногда перфоратор может заклинить в пробиваемом отверстии. Это состояние чревато поломкой насадки, самого перфоратора или нанесением травмы рабочему вследствие резкого рывка инструмента, возникающего при мгновенной остановке бура. Для этого перфораторы снабжены предохранительной муфтой, которая служит для остановки вращения патрона при заклинивании инструмента в отверстии. Надо понимать, что это случай аварийный и частое срабатывание весьма не желательно. И вот почему.
Работа предохранительной муфты видна на Рис.1, где А1-прижимная гайка, А2-прижимной механизм, А3-опорная шайба, прижимающая шарики, А4-сепаратор с шариками, А5-шестерня с углублениями под шарики. Роль прижимного механизма на рисунке выполняют пружинные тарельчатые шайбы. Иногда в конструкции может быть использована витая пружина. В качестве блокирующего элемента могут быть шарики, ролики или две сопряженные детали с трапецевидными выступами, которые входят в зацепление между собой.
Рис.2 - под воздействием внешней силы шарик упирается в препятствие (Рис.2_В). Механизм заблокирован и редуктор вращает оснастку. Как только оснастка застрянет в материале при вращающемся редукторе, нагрузка на шарик возрастет и при превышении какого-то значения пружина (Рис.2_А) будет не в состоянии удерживать шарик в заблокированном положении, она сожмется. Шарик при этом перепрыгнет через препятствие (Рис.2_красная стрелка). Наглядно это можно увидеть на Рис.3_GIF. В результате таких перескакиваний, шарик ударяется о препятствие, вызывая срабатывание прилегающих поверхностей. Появляются зазоры (Рис.4_отмечены красным), усиливающие люфты в механизме. При появлении люфтов дальше процесс разрушения будет происходить лавинообразно, т.к. в зазорах появится дополнительный ударный момент. Рис.5- выработка на шестерне, между углублениями под шарики образовалась "дорожка"; Рис.6- "дорожка на опорной шайбе".
Даже незначительные повреждения граней в сопряженных узлах, в данных механизмах, НЕ ДОПУСТИМЫ (!), от слова "совсем". На Рис.7 блокировочный узел в стволе инструмента WORTEX RH-3239. Он не относится к предохранительной муфте, но и тут все грани зацепления должны быть просто идеальными. Грани отмечены красными стрелками.
Чуть подробнее о причине такого требования к этим узлам (для терпеливых и желающих подробно разобраться). Под шариками образуется, пусть и незначительная на первый взгляд, выработка (Рис.8). Для примера деталь от шуруповерта (Рис.9) с подобной "дорожкой". На Рис.10 красная стрелка- внешняя сила, приложенная к шарику и заставляющая его двигаться слева на право (по схеме). Белыми стрелками, вертикальная- прижимающая сила, это действие пружины на шарик и наклонная- противодействующая реакция опоры. Между этими стрелками образуется некий угол. На нижней схеме угол меньше, т.к. точка опоры стала ниже из-за выработки грани.
Рис.11- схема из которой понятно все выше сказанное. От угла между вектором прижимающей силы (N) и обратным вектором реакции опоры (Rp) есть вектор (Ft) обратный внешней силе (P). Этот вектор называется сила трения качения. Он и препятствует перемещению шарика. И чем эта сила больше, тем больше шансов удержать шарик на месте. Конструктивным решением эта сила имеет определенное значение и малейшее отклонение от этих расчетов неминуемо обернется выше описанными проблемами. Открыть в новой вкладке
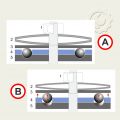 Рис.1 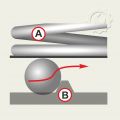 Рис.2 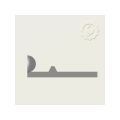 Рис.3_GIF 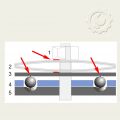 Рис.4 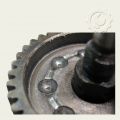 Рис.5 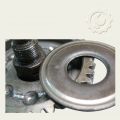 Рис.6 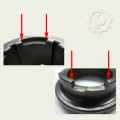 Рис.7 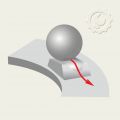 Рис.8 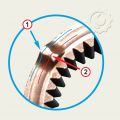 Рис.9 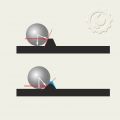 Рис.10 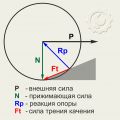 Рис.11
|
Перегорание предохранителей в автомобильных компрессорах Развернуть ▼
|
Перегорание предохранителей в новых автомобильных насосах часто происходит по причине закорачивания питающего провода на корпус насоса. На фотографиях показана модель бренда ЕСО, но подобная неисправность имеет место быть и в моделях DGM. Разборка изделия от DGM может отличаться конструктивно, но суть проблемы и метод ее устаранения тот же.
1. Снимаем крышку с выключателем (фото 1), видим провод с необжатым термокембриком (фото 3).
2. Обжимаем с помощью фена (фото 4).
3. Меняем перегоревший предохранитель (фото 2) и собираем изделие. Открыть в новой вкладке
|
Давление, регулировка (насосная станция) Развернуть ▼
|
О давлении в насосных станциях и регулировке прессостата.
Работа насостной станции (Рис.1) заключается в том, что бы поддерживать рабочее давление в водопроводной системе в установленных значениях. Ее функция начинать работать тогда, когда давление в системе упаден до нижнего порога (около 1,5 bar) и выключаться, когда давление дойдет до верхнего предела (около 2,8 bar).
В конструкции насосной станции предусмотрен баллон, выполняющий роль гидроаккумулятора. Его устройвство на Рис.2. При подключении насоса к водопроводной системе, резиновая груша заполняется водой (Рис.2_В). Рис.2_А - это ресиверный баллон, который выполняет роль противодействующей пружины на воду. В баллоне изначально должно быть давление около 1,5 bar (точные значения в прилагаемых инструкциях). Это давление соответствует нижнему значению в водопроводной системе. Если давление в баллоне будет отсутствовать или будет его недостаточное количество, то насос будет работать не выключаясь.
Для контроля давления и при необходимости его добавления, с торца баллона есть заглушка (Рис.3), открутив которую мы обнаружим ниппель (Рис.4). Для контроля, к нему можно подсоединить манометр или насос с намометром для докачки автомобильных колес. Давление при отключенной насосной станции должно быть 1,5 bar.
Теперь о регулировке прессостата, который выполняет роль управления двигателем насосной станции (Рис.5). Сняв верхнюю крышку с прессостата мы увидим две регулирующие пружины. Большая пружина (Рис.6_А) отвечает за общую регулировку давления, маленькая пружина (Рис.6_В) устанавливает дифференциальное значение давлений, т.е. увеличивает или уменьшает разницу между максимальным и минимальным значением.
Регулируя большую пружину мы изменяем общее давление. Иными словами увеличивая максимальное давление мы одновременно увеличиваем и минимальное давление срабатывания прессостата. Процесс изменения хорошо понятен на Рис.7_GIF.
Маленькой пружиной мы можем регулировать разницу между максимальным и минимальным давлением (Рис.8_GIF).
На практике регулировка сводится к следующим действиям. Большой пружиной устанавливаем максимальное давление, давление при котором прессостат будет отключаться. Затем маленькой пружиной устанавливаем минимальное значение, давление при котором прессостат будет включаться. В заключении операции по настройке следует перепроверить максимальное давление, оно может немного измениться. Если это произошло, то следует повторить операцию (скорректировать максимальное давление и проверить минимальное).
Здесь на примерах показаны условные значения давлений для наглядности. Давление, на которое следует настраивать, указано в паспорте к устройству.
Реле давления в насосной станции имеет заводские установки 1,5 bar для пускового давления и 2,8 bar давления для остановки. По мнению производителя, это наиболее приемлемые значения для преобладающего большинства подобных установок. Открыть в новой вкладке
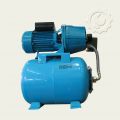 Рис.1 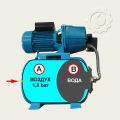 Рис.2 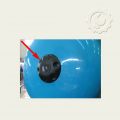 Рис.3 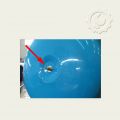 Рис.4 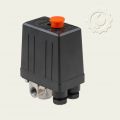 Рис.5 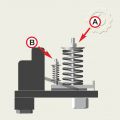 Рис.6 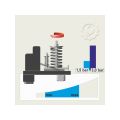 Рис.7_GIF 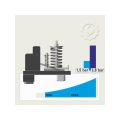 Рис.8_GIF
|
Кривой рез (лобзик) Развернуть ▼
|
Не редки случаи обращения клиентов с жалобой на кривой рез у такого инструмента как лобзик. Сразу следует оговориться, лобзик - это инструмент для криволинейного реза. Для прямых продольных или поперечных резов, там где требуется точность, следует применять другой инструмент, специально предназначенный для таких операций.
Для того, чтобы получить точный рез по вертикали, неоходимо прилагать усилие идеально по центру реза пилки (Рис.1). На практике такое получить довольно сложно и зависит от опыта и способностей пользователя. Достаточно приложить незначительное усилие в сторону относительно линии реза (Рис.2_А), даже если мы будем вести пилку точно по резу (Рис.2_В), пилка в нижней части пропила уйдет в сторону (Рис.3_В). Получится рез примерно такой, какой показан на Рис.4_А.
Второй момент, при котором пилку уводит в сторону от линии пропила - это естественный конструктивный люфт штока. Пилка при этом имеет некоторую подвижность, что является нормальным явлением. Так же на увод в сторону может влиять неравномерная острота зубьев пилки. К примеру в какой-то момент пилка попала одной стороной на твердый предмет и слегка подтупилась. В результате линия реза будет уходить в сторону затупленной стороны (Рис.5).
Открыть в новой вкладке
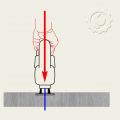 Рис.1 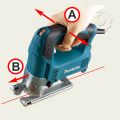 Рис.2 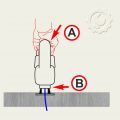 Рис.3 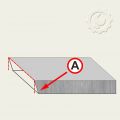 Рис.4 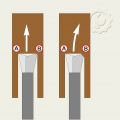 Рис.5
|
Регулировка клапанов (двигатель 4-х тактный) Развернуть ▼
|
Как правильно отрегулировать зазоры клапанов в четырех-тактном одноцилиндровом двигателе (Рис.1_GIF)?
Действия по настройке зазоров заключаются в следующем:
!!! Регулировку клапанов следует выполнять только на холодном двигателе.
--- для начала следует отсоединить стакан с масляной ванной от воздушного фильтра и фильтрующего элемента
--- с помощью ключа открутить четыре болта крепления клапанной крышки
--- после данных действий необходимо снять стартер и защитный кожух маховика
--- проворачивая маховик, выставить в верхнюю мертвую точку поршень. При этом коромысла клапанов должны быть расслаблены, проверить можно слегка подвигав их рукой
--- зазор замеряется между коромыслом и клапаном (Рис.2), (Рис.3), для этого используется щуп (Рис.4) Следует помнить, что входной клапан размещается возле фильтра (Рис.5_А), а выходной – возле глушителя (Рис.5_В).
Чтобы проверить интервалы, нужно вставить щуп между коромыслом и клапаном.
Зазоры клапанов для бензиновых двигателей мотоблоков должны быть:
--- впускной клапан 0,15мм
--- выпускной клапан 0,20мм
Удовлетворительным результатом будет считаться такой зазор, при котором больший щуп не проходит. Например зазор 0,15мм - щуп 0,15мм в зазоре можно двигать, а щуп 0,20мм уже не проходит и зазор 0,20мм: щуп 0,20мм проходит, а 0,25мм нет.
Если расстояние отклоняется от допустимого, нужно отрегулировать зазоры накидным ключом или отверткой. После зажатия контрирующей гайкой надо перепроверить зазор, т.к. за счет люфтов резьбового соединения зазор может измениться.
При правильной регулировке клапанов двигатель будет работать бесшумно, без каких-либо рывков и сбоев.
Открыть в новой вкладке
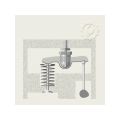 Рис._GIF 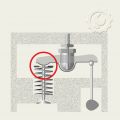 Рис.2 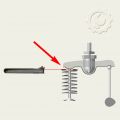 Рис.3 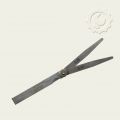 Рис.4 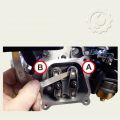 Рис.5
|
Лубрикатор - важная деталь (пневмоинструмент) Развернуть ▼
|
При пользовании пневмоинструментом одним из главных узлов является лубрикатор. Игнорировать его использование нельзя. Основная задача лубрикатора - снизить износ трущихся узлов. Дополнительно обеспечивается компенсация технологических зазоров в инструменте.
Существует два вида лубрикаторов, магистральный и линейный. Линейный устанавливается непосредственно между шлангом и инструментом и часто прилагается в комплектации к инструменту (Рис.1). Это касается в основном бытовой линейки.
Для более крупных задач потребуется применение магистрального лубрикатора (Рис.2). Устанавливать его надо после воздушного фильтра и после влагоотделителя.
После воздушного фильтра по причине того, что фильтр моментально пропитается маслом и потеряет свои функциональные свойства.
После влагоотделителя для того, что бы не образовывалась эмульсия вместо масляной смеси. Лубрикатор должен располагаться от инструмента не более чем 8 - 10 метров. Это для того чтобы масло не осело полностью на стенках шланга.
Открыть в новой вкладке
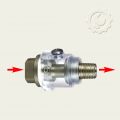 Рис.1 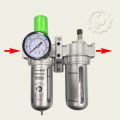 Рис.2
|
Нет всасывания (мотопомпы) Развернуть ▼
|
Иногда поступают в ремонт мотопомпы с жалобой от клиентов, что слабое отрицательное давление на всасывании. Т.е. мотопомпа не захватывает воду, либо слабо захватывает. Иногда при осмотре деталей во время ремонта обнаружить неистравность сходу не получается. Все детали как новые и повреждений не видно.
Наиболее вероятная причина - неисправное мехуплотнение (Рис.2). В 90% случаев замена этого узла приводила к положительным результатам.
Если повреждений керамических уплотнений, типа абразивного износа, не обнаружено, то случай можно считать гарантийным. Открыть в новой вкладке
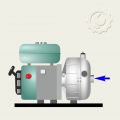 Рис.1 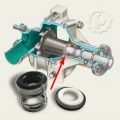 Рис.2
|
Не отключается двигатель (ЕСО HPW_все модели) Развернуть ▼
|
Ранее была написана статья "Не отключается двигатель (ECO HPW-1720Si_очиститель высокого давления)", где описывалась неисправность с блоке TSS. Здесь описывается схожая неисправность, но с несколько другой причиной.
В данной статье описывается причина неотключающегося двигателя - выпадение стопорной шайбы фиксирующей обратный клапан. Отличить неисправность, от описанной в прошлой статье, несложно.
Когда причина неисправности связана с блоком TSS, двигатель ОВД (очиститель высокого давления) не вращается, но гудит - как бы не может стартонуть. Насос при этом не работает. В случае выпадения обратного клапана, двигатель, как ни в чем не бывало продолжает активно вращаться. Если в первом случае гудение двигателя плохо слышно, а в шумном помещении можно и вовсе не заметить, то в описываемом случае, не заметить работу двигателя сложно. Двигатель начинает громко гудеть, пытаясь преодолеть давление запертой воды. Обнаружить выпадение клапана можно следующим образом.
Внутри выходного канала (Рис.1_А), тот к которому прикручивается шланг с пистолетом, расположен обратный клапан. Он фиксируется стопорной шайбой в виде "звездочки". Если открутить высоконапорный шланг и заглянуть внутрь канала, то можно увидеть эту шайбу (Рис.2_А). Она должна плотно сидеть в своем штатном положении, прижимая обратный клапан. Были случаи на новых мойках, когда эта шайба криво стояла, а то и вовсе отсутствовала.
Если пришла мойка в ремонт с отсутствующей шайбой и самим клапаном, не торопитесь обвинять пользователя в попытках самостоятельного вмешательства в насосный узел. Очень часто происходит так. Криво стоящая шайба не удерживает обратный клапан. Клиент об этом может не подозревать. Если он (клиент) включит ОВД без шланга (например попытается принудительно удалить воду из насоса для постановки ОВД на хранение), то под давлением клапан просто выстрелит и улетит в неизвесном направлении. Этот клапан вместе с шайбой (Рис.3_А, Рис.3_В) клиент потом может и не найти.
Случай этот считаем гарантийным. Открыть в новой вкладке
|
Разрушение кулачков (динамометрический ключ TOPTUL ANA*) Развернуть ▼
|
Иногда приходится сталкиваться с таким повреждением, как разрушение, скол кулачков.
Конструкция ключа довольно проста. Эксцентриком (Рис.1_А) перемещаются подпружиненные кулачки, блокирующие посадочный квадрат под накидную головку. Кулачок, блокирующий ключ при закручивании (Рис.1_В), обозначен значком "+", блокирующий при откручивании (говорим о правой резьбе) значком "-" (Рис.1_С). Кулачки блокируют через зубчатую конструкцию посадочный квадрат ключа (Рис.1_D).
Если использовать ключ как силовой, откручивая болты-гайки, то будет повреждаться кулачок "-" Рис.1_С. Это явное нарушение условий эксплуатации. Динамометрический ключ предназначен ТОЛЬКО для контроля усилия затяжки крепления! Использовать его как силовой НЕЛЬЗЯ!
Другой момент скалывания кулачка. Это может произойти с любым кулачком, особенно при больших усилиях. Это неполное зацепление кулачка с зубчатым колесиком. Как это происходит? Переключение с прямого вращения на реверс осуществляется рычажком с эксцентриком (Рис.3). Если рычажок переключается правильно, до упора в крайние положения (Рис.4_1и2), то зацепление кулачка и зубчатой детали будет полным. Рис.4_А - при откручивании, Рис.5_А при закручивании. Если рычажок не довести до конца (Рис.6_А), то зацепление будет неполным и вся нагрузка придется на малую часть кулачка (Рис.6_В), и как результат его разрушение (Рис.7). На Рис.8 вид поврежденного кулачка.
Все выше перечисленные случаи не являются гарантийными, т.к. возникли по вине пользователя, который не соблюдал элементарные условия эксплуатации инструмента. Открыть в новой вкладке
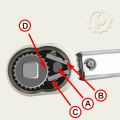 Рис.1 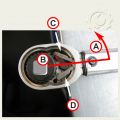 Рис.2 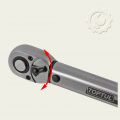 Рис.3 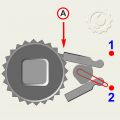 Рис.4 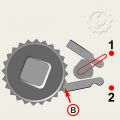 Рис.5 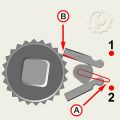 Рис.6 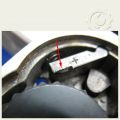 Рис.7 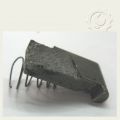 Рис.8
|
|
|
|