Уважаемые клиенты, с 01.01.2024г. мы прекращаем принимать инструменты BOSCH в платный ремонт
Типы изделий:
|
Диагностика и анализ неисправностей:
Сваливание ремня со шкива (бетоносмеситель ЕСО серии СМА) Развернуть ▼
|
В бетоносмесителях ЕСО серии СМА наблюдалось такое явление как сваливание ремня со шкивов Рис.1. Конструктивно механизм привода представляет собой электродвигатель со шкивом (Рис.2_А), который связан ручейковым ремнем (Рис.2_В) с ведомым шкивом (Рис.2_С). Вал ведомого шкива вращается во втулке (Рис.2_D). Электродвигатель закреплен к плите моторного блока через кронштейн (Рис.2_Е).
Причина сваливания ремня заключается в том, что шкивы находятся не в одной плоскости вращения. В первом случае это может быть что оси шкива и двигателя параллельны, но центра ручейкового канала смещены относительно друг друга (Рис.3_А). Ремень в этом случае смещается к краю шкива, упирается в ограничительный буртик. В этом случае ремень, наползая на буртик сваливается, либо трением об этот буртик оплавляет его.
Во втором случае оси шкива и двигателя могут быть не параллельны (Рис.3_В) и тогда ремень просто съезжает со шкива. Решать проблему следует творчески либо методом подкладывания регулировочных шайб, либо заменой неисправных деталей. В узле есть три места из-за которых появляется рассматриваемая проблема - это разбитая втулка ведомого шкива (Рис.4_А), кронштейн крепления электродвигателя (Рис.4_В) и нижний болт крепления плиты моторного блока (Рис.4_С).
В случаях непараллельности осей шкива и двигателя может быть износ втулки (Рис.4_А). В этом случае ремень будет соскальзывать в сторону двигателя (Рис.5). Тут нужна будет замена плиты моторного блока.
Если ремень уходит в сторону от двигателя (Рис.6), то вероятнее всего ось шкива электродвигателя повернута (по рисунку) по часовой стрелке, т.е. задняя часть двигателя как бы опущена. В этом случае можно подложить регулировочные шайбы между стойкой бетоносмесителя и плитой моторного блока (Рис.4_С). Это касается случаев непараллельности осей шкивов (Рис.3_В).
В случаях когда плоскости шкивов параллельны, но не совпадают между собой, как бы смещены (Рис.3_А) можно подложить шайбы между плитой моторного блока и кронштейном крепления электродвигателя (Рис.4_В). В этом случае мы можем сместить шкив электродвигателя в сторону от плиты обеспечив плоскостность с ведомым шкивом. Открыть в новой вкладке
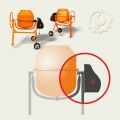 Рис. 1 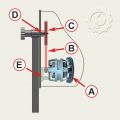 Рис. 2 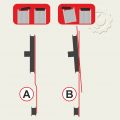 Рис. 3 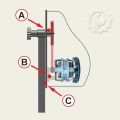 Рис. 4 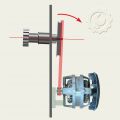 Рис. 5 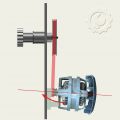 Рис. 6
|
Не качает воду, завоздушивание (ЕСО серии DP) Развернуть ▼
|
Статья о ситуации когда при визуально исправном насосе нет подачи воды. Т.е. электромотор работает, крыльчатка вращается, поплавок включает и выключает двигатель, но подачи воды нет. Основные узлы насоса на Рис.1. Это верхняя крышка с электрической частью (Рис.1_1), электромотор (Рис.1_2), открытое многолопастное рабочее колесо, далее будем называть его крыльчаткой (Рис.1_3) и нижняя часть корпуса для забора воды (Рис.1_4). При погружении насоса нижняя часть корпуса должна наполниться водой (Рис.2_1) о чем будут свидетельствовать поднимающиеся пузыри воздуха. Вращающаяся от электродвигателя крыльчатка за счет центробежной силы втягивает воду в нижней части насоса (Рис.2_2) и выбрасывает в боковой канал (Рис.2_3). Далее по шлангу вода под давлением поступает наружу. Для того чтобы полость заполнилась водой предусмотрено дренажное отверстие в нижней части корпуса (Рис.3). Отверстие реализовано в виде клапана и состоит из металлического шарика (Рис.4_1) и удерживающей его пластинки (Рис.4_2). Работает это так. При пустой полости нижней части корпуса шарик под своим весом опускается вниз и удерживается от выпадения пластинкой. В этом случае вода будет поступать в образовавшееся отверстие в полость (Рис.5_А), а воздух вытесняться (Рис.5_В). Когда насос начнет работать, то внутри полости возникнет повышенное давление от нагнетаемой воды и шарик под напором поднимается вверх (Рис.5_С) и перекрывает дренажное отверстие, препятствуя ненужной утечке воды. В случае засорения канала шарик не сможет вернуться в исходное нижнее положение и останется вверху, перекрыв дренажное отверстие (Рис.6). В этом случае при погружении насоса вода не будет заполнять насосную полость и вращающаяся крыльчатка будет просто гонять воздух по кругу. Нагнетание воды в этом случае происходить не будет. Открыть в новой вкладке
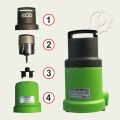 Рис. 1 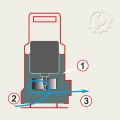 Рис. 2 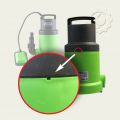 Рис. 3 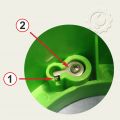 Рис. 4 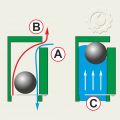 Рис. 5 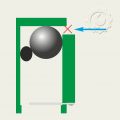 Рис. 6
|
Коленвал со шпонкой и без (AE 705-3_AE 502-3, AC 252, AC 253) Развернуть ▼
|
Все эти модели имеют схожую конструкцию и по тому представлены на сайте одним чертежом, но есть некоторые отличия в исполнении коленвалов. В старых моделях, для позиционирования коленвала на ведущем валу, использовалась шпонка (Рис.1_А). На более новых моделях вместо шпонки используется винт (Рис.1_В). Винт позиционирования определяет положение коленвала на ведущем валу (Рис.2_А), а винт (Рис.2_В) фиксирует коленвал, обжимая его в направлении синих стрелок (Рис.2). На Рис.3 вид со стороны резьб - винт позиционирования (Рис.3_А) и фиксирующий винт (Рис.3_В). Открыть в новой вкладке
|
Лайфхак, приспособление для испытаний Развернуть ▼
|
Для проверки работоспособности мотокосы иногда приходится запускать двигатель без приводной трубы. Это бывает в случаях, когда необходимо проверить устройство на биение и определить что вызывает вибрацию - приводной вал, оснастка или сам двигатель. Для этого нам необходимо отключить дополнительные узлы и методом исключения определить неисправный узел. Запустить двигатель мотокосы без приводного вала у нас не получится, т.к. отсутствие барабана в приводном валу не сможет ограничить вылет кулачков муфты сцепления. Нам надо чем-то заменить приводной вал. Для этого можно использовать отдельно тестовый корпус муфты сцепления с барабаном, насаженный на небольшой отрезок приводной трубы (Рис.1). Открыть в новой вкладке
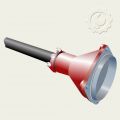 Рис.1
|
Поршень. Какой стороной устанавливать? Развернуть ▼
|
Иногда возникает вопрос, какой стороной установить поршень? Где у него передняя, а где задняя части? Попробуем разобраться.
Как правило, осевое положение пальца поршня несколько смещено в одну из сторон относительно оси самого поршня. На слабонагруженной технике встречаются поршни с пальцами, расположенными на одной оси с осью поршня. В этом случае нет разницы какой стороной устанавливать поршень. Для поршней со смещенным пальцем разница есть и о ней поговорим подробнее.
На (Рис.1_А) ось вращения коленвала, (Рис.1_В) ось вращения шатуна относительно коленвала. Во время работы двигателя (красной стрелкой показано направление вращения коленвала) шатун постоянно находится под некоторым углом к оси цилиндра, причем этот угол постоянно изменяется. Поэтому сила, приложенная к поршневому пальцу, раскладывается на две. Эти силы назовем Fшатуна (Fш) и Fпоршня (Fп) (Рис.2). В результате действия этих сил возникает третья сила, воздействующая на поршень и направленная перпендикулярно оси цилиндра. Назовем ее Fрезультирующая (Fрез.). Чем больше силы Fш и Fп, тем больше будет сила Fрез.
В ВМТ и НМТ вектора Fш и Fп складываются и Fрез. в этом случае будет равна нулю (Рис.3).
После прохождения ВМТ происходит вспышка топливной смеси и поршень перекладывается, т.к. меняется направление силы вектора шатуна (Fш) (Рис._4_А). И в этом цикле сила эта намного больше той силы, что была при сжатии. Если верить справочникам, то боковая сила, прижимающая поршень к стенке цилиндра приблизительно равна 10% — 12% процентов, от силы, действующей в направлении оси цилиндра. У автомобиля это около нескольких сотен килограмм. Из-за скоротечности процесса такое перекладывание поршня можно сравнить с ударом.
Для уменьшения силы удара, при перекладке поршня, ось поршневого пальца (вернее ось отверстия в бобышках поршня под поршневой палец) смещена в сторону основной упорной поверхности, т.е. вперед по направлению движения газов (Рис._5). Дополнительно на днище поршня ставится отметка (Рис.6_А).
По итогу нужно запомнить следующее. Метка на поршне всегда стоит со стороны где палец ближе к стенке поршня (Рис.7_А) и направлена должна быть против хода вращения коленвала (Рис.7_В).
Возникли вопросы, пришлось дополнить статью и разложить более подробно.
На Рис.8 поршни с центральным расположением пальца (слева) и со смещенным (справа).
Вертикальная сила (Рис.8_1), действующая на поршень, раскладывается на две разнонаправленные (Рис.8_2) и (Рис.8_3). Это происходит потому, что вектор шатуна (Рис.8_2) смещен относительно вертикали и направлен на точку опоры шатуна и шейки коленвала. Эти силы прижимают поршень к одной из сторон цилиндра (Рис.8_4). В данном примере вращение коленвала против часовой стрелки.
По мере вращения коленвала шатун принимает противоположные углонаправленные положения, заставляя поршень перекладываться с одной стороны на другую. При скоротечности процесса такие перекладывания сродни ударам. Все эти силы и при цикле сжатия, и при цикле вспышки. Но вертикальная сила, действующая на поршень при вспышке, гораздо больше этой же силы при цикле сжатия. По-этому и сила прижатия к стенке цилиндра при вспышке будет больше. Такое явление негативно сказывается на износостойкости и общей работе двигателя. Чтобы уменьшить такие нагрузки палец смещается относительно оси поршня. Такое смещение обычно с пределах 1-2,5 мм. Теперь о том что происходит.
Если палец расположен по центру и совпадает с осью поршня, то вертикальная сила действующая на поршень будет поровну распределена как на переднюю часть дна поршня (Рис.9_1), так и на заднюю (Рис.9_2). При смещении пальца вертикальная сила будет распределена на дно поршня не равномерно. Это можно с некоторой натяжкой сравнить с коромыслом, где точка переваливания будет на оси поршневого пальца. И чтобы при вспышке топлива уменьшить силу прижатия поршня к стенке цилиндра смещают ось пальца относительно оси поршня против хода вращения коленвала и по ходу отработанных газов.
Получается что на переднюю часть дна поршня приходится меньшая сила (Рис.9_5) чем на заднюю (Рис.9_4) и сила прижатия при этом соответственно уменьшится (Рис.9_6) против варианта с центральным расположением пальца (Рис.9_3). Это происходит потому, что бОльшая сила (Рис.9_4), частично преодолевая меньшую силу (Рис.9_5) пытается удержать поршень в вертикальном положении и значительно снимает нагрузку давления на стенку цилиндра (Рис.9_6) Открыть в новой вкладке
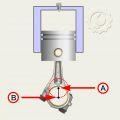 Рис.1 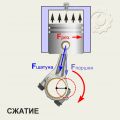 Рис.2 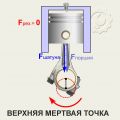 Рис.3 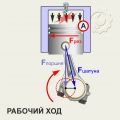 Рис.4 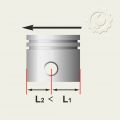 Рис.5 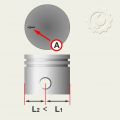 Рис.6 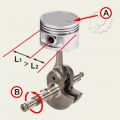 Рис.7 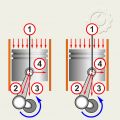 Рис.8 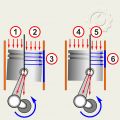 Рис.9
|
Ремонт клапана горелки (сварочный аппарат) Развернуть ▼
|
Ремонт клапана горелки (сварочный аппарат)
Нередкий случай неисправности: "Горелка не держит газ. При отпущенной клавише, газ все равно травит." Причина - неисправность клапанного механизма. Устранить неисправность легко.
Общий вид клапана на Рис.1. С одной стороны корпуса выступает шток на который нажимает рычаг рукоятки горелки. Он подпружинен и легко нажимается пальцем. С противоположной стороны мы можем заметить заглушку. Для разборки клапана нам понадобятся тиски и маленький молоточек. Ставим клапанный механизм на тиски (Рис.2) и слегка ударяем по штоку. Заглушка выпадает, а вместе с ней пружинка и шток. Желательно снизу что-то подложить, т.к. заглушка выскочив из отверстия освободит пружинку, которая может потеряться. На Рис.3 (сверху) показано положение узлов клапанного механизма. Снизу (Рис.3) детали механизма: шток (он выполняет роль золотника), пружина, заглушка и сам корпус. После демонтажа клапанного механизма оцениваем состояние уплотнительных колец (Рис.4). В случаях повреждений (закусаны при сборке, порваны и пр.) меняем на новые. Чаще наблюдается целостность колец, но при этом они "сухие". В данном случае достаточно смазать уплотнения силиконовой смазкой (Рис.5) и собрать клапан. Забив заглушку в штатное положение, можно по стыку (корпус-заглушка) слегка накернить.
Эту неисправность можно рассматривать как гарантийный случай. Открыть в новой вкладке
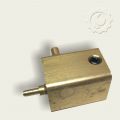 Рис.1 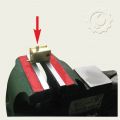 Рис.2 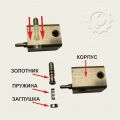 Рис.3 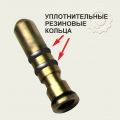 Рис.4 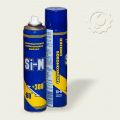 Рис.5
|
Диагностика AVR Развернуть ▼
|
Для регулировки выходного напряжения в генераторе используется регулятор напряжения (Рис. 1), который соединяется с силовой обмоткой, обмоткой возбуждения и обмоткой ротора через контактные кольца и щетки. Контролируемое напряжение силовой обмотки измеряется и сравнивается с базовым напряжением, которое устанавливается регулировочным винтом (Рис.2_красная стрелка). Если контролируемое напряжение ниже базового (низкое напряжение в розетке), регулятор автоматически увеличивает ток в роторе. Если контролируемое напряжение выше рекомендуемого (высокое напряжение в розетке), регулятор уменьшает силу тока в роторе, и выходное напряжение уменьшается. Постоянный контроль над силой тока в роторе позволяет поддерживать стабильное выходное напряжение.
Корректировка регулятора напряжения:
ВНИМАНИЕ: Корректировка должна производиться при включении электростанции и со снятой крышкой генератора. Избегайте контакта с горячей выхлопной трубой и электрическими проводами. Перед тем как корректировать регулятор напряжения, убедитесь, что частота вращения двигателя в норме.
1. Запустите двигатель и дайте ему прогреться в течение нескольких минут.
2. Используйте точный вольтметр для измерения напряжения в розетке.
3. Отрегулируйте напряжение регулировочным винтом, как показано на рисунке 1, используя отвертку.
Диагностика и поиск неисправностей AVR:
Запустить двигатель и проверить частоту вращения, при необходимости отрегулировать.
Предварительная проверка - замерить выходное напряжение непосредственно в розетке, используя вольтметр.
ВНИМАНИЕ: Нулевое напряжение свидетельствует о разрыве цепи или о полной потере остаточного магнетизма ротора. (Восстановление остаточного магнетизма в статье https://remont.tools.by/diagnostics/view/1682690091).
При неправильных показателях проводим дальнейшую диагностику, используя метод исключения.
1. Подаем постоянный ток в обмотку ротора. Для этого необходимо подсоединить аккумулятор
12В непосредственно к плюсовому и минусовому проводам щеток на коллекторе ротора. Для этого надо снять заднюю крышку (Рис.3_В) и подключиться к щеткам ротора (Рис.4_С)
2. Измеряем выходное напряжение обмотки возбуждения (должно быть 200-250В)
3. Измеряем напряжение основной обмотки (примерно 110-130В)
Если при тестировании, мы получили значения напряжения указанные выше, то неисправность связана с неработающим AVR.
К такому выводу мы пришли, исключив заведомо исправные узлы. Данные тесты подтвердили, что обмотка возбуждения и силовая обмотка исправны. Наличие выходного напряжения в розетке подтверждает исправность щеток, контактных колец и ротора. Следовательно, неисправен регулятор напряжения.
Регулятор меняется целиком и ремонту не подлежит. Открыть в новой вкладке
|
Управляющий TSS-клапан DGM Water 140/160 Развернуть ▼
|
Для очистителей высокого давления DGM WATER 140/160 поставлялись управляющие клапана под резьбовое соединение (Рис.1). После 2022 года стали выпускаться модели с креплением клапанов под скобу (Рис.2). Сейчас мы имеем управляющие клапана двух видов. При ремонтах и заказе з/ч это следует учитывать.
О взаимозаменяемости TSS-клапанов, как вариант, было предложено в отдельной статье https://remont.tools.by/diagnostics/view/1724930068.
Открыть в новой вкладке
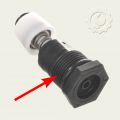 Рис.1 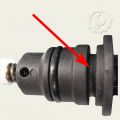 Рис.2
|
Заклинивание муфты Развернуть ▼
|
Иногда появляются случаи заклинивания муфты сцепления в мотокосах. Пользователь нажимает на газ, а редуктор не вращается. Сразу на ум приходит наиболее вероятная причина подобной неисправности - это либо слизывание шлицев на ведущем валу, либо разрушение зубчатой пары редуктора. Но все может оказаться проще. Не работает муфта сцепления. Т.е. инерционные кулачки находятся в заблокированном состоянии и не расходятся при увеличении оборотов двигателя.
Причина в зажатых болтах, на которых крепится муфта (Рис.1). Механизм крепления муфты устроен следующим образом. Под муфтой устанавливаются опорныя шайбы (Рис.2_А). Внутренний диаметр их отверстий 8,5мм. Крепежные болты имеют резьбу М8 и свободно входят в это отверстие, но затем упираются безрезьбовой частью, которая имеет диаметр 9,7мм, на шайбу. Таким образом дальше вкрутиться болт не может. Длина безрезьбовой части болта 10мм, а длина втулки муфты, в которую вставлен болт, 9,2мм (Рис.3).
Если вставить болт в муфту без пружинной шайбы, то получится что болт выступает за кромку муфты (Рис.4_А). Таким образом при зажатии болта в корпус маховика появляется осевая подвижность муфты сцепления примерно около одного миллиметра. Этот зазор компенсируется пружинной шайбой (Рис.2_В) и не мешает подвижности кулачков в радиальном направлении.
Основная причина неисправности такого типа - это изнашивание опорной шайбы, изнашивание опорной части болта, либо просто отсутствие по какой-либо причине этой опорной шайбы. Открыть в новой вкладке
|
Аккумулятор, перенос наклейки Развернуть ▼
|
При замене аккумуляторов иногда приходится сталкиваться с такой ситуацией, когда вместо оригинального аккумулятора вынуждены менять на аналог. Такое решение не противоречит требованиям производителя, но иногда вызывает негативную реакцию у клиента. Человек, не вникая в технические подробности, требует установки "оригинального" аккумулятора, тот что был при комплектации. Убеждать его в правомерности такой замены порой бывает бесполезно, т.к. мыслит он скорее ассоциативно нежели рационально.
Аккумуляиоры BULL (Рис.1) и аккумуляторы от WORTEX (Рис.2) в принципе идентичны (Рис.3) и замена одного на другой вполне оправдано. В таких случаях необходимо перенести наклейку со старого аккумулятора на новый. Сделать это легко с помощью технического фена (Рис.4). Слегка подогрев наклейку аккуратно ножиком поддеваем старую наклейку и снимаем ее со старого аккумулятора. Клейкий слой при этом должен остаться на наклейке. Если этого не произошло и что-то пошло не так, можно применить двусторонний, тонкий скотч.
Снятую наклейку аккуратно криклеиваем на новый аккумулятор (Рис.5). Полученный результат внешне не будет отличаться от "оригинального".
Такая операция обязательна при замене аккумуляторов даже в пределах одного бренда если дело касается сохранения серийного номера изделия. Серийный номер на аккумуляторе должен совпадать с серийными номерами на инструменте и на зарядном устройстве. Открыть в новой вкладке
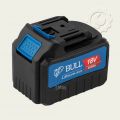 Рис.1 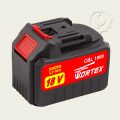 Рис.2 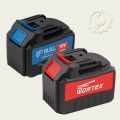 Рис.3 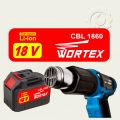 Рис.4 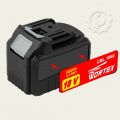 Рис.5 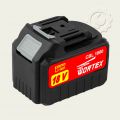 Рис.6
|
Повреждение щеткодержанелей, щеток MAKITA BO 5031 Развернуть ▼
|
Иногда поступают в ремонт эксцентриковые шлифмашины с замятыми щеткодержателями. В данной статье разговор пока про модель MAKITA BO5031. В результате деформированных щеткодержателей, щетки теряют свою подвижность и в процессе эксплуатации разрушаются. Попытаемся разобраться в чем причина такого повреждения.
Если снять верхнюю крышку инструмента, то увидим щетки в резиновых аммортизаторах (Рис.1). На Рис.2_А щеткодержатель, который вставлен в резиновый аммортизатор (Рис.2_В). Резиновый аммортизатор вместе с щеткодержателем вставлен в направляющие корпуса самой машинки (Рис.3_А - вид сверху), (Рис.3_В - вид в плане). При монтаже щеткодержателя (Рис.4_А) может так получиться, что резиновый аммортизатор не сядет на место. Пойдет с перекосом или еще как и упрется в направляющие (Рис.4_В). Иными словами не дойдет до конца.
Если механик не проявит должного внимания к данной ситуации, то в дальнейшем произойдет следующее. Сверху будет установлена крышка, у которой есть выступы, предназначенные для фиксации щеткодержателя (Рис.5). Фиксируя крышку винтами, механик принудительно пытается затолкнуть щеткодержатели на свое место. Но этого не происходит. Резину аммортизатора раздавливает и она еще плотнее цепяется за направляющие. Такую ситуацию несложно заметить. Крышка в этом случае не сядет на место. Она должна мягко, от руки сесть на место, без зазоров и пр. перекосов до закручивания винтов.
Если не обратить на это внимание, то дальнейшее закручивание крепежных винтов крышки приведет к деформации самого щеткодержателя (Рис.6) и прижмет щетку, лишив ее подвижности. Результат такой невнимательности на Рис.7, где (А) промятый корпус щеткодержателя и (В) разрушенные щетки. Открыть в новой вкладке
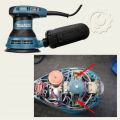 Рис.1 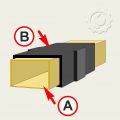 Рис.2 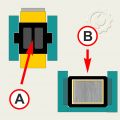 Рис.3 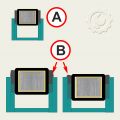 Рис.4 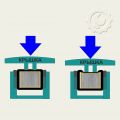 Рис.5 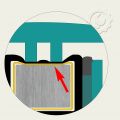 Рис.6 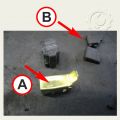 Рис.7
|
Не работает маятниковый ход в лобзике ST 1301 BULL Развернуть ▼
|
В ремонт поступило несколько лобзиков BULL ST 1301 c заявленной неисправностью «не работает маятниковый ход».
Проблема подтвердилась, был выявилен неправильный алгоритм движения механизма подкачки опорного ролика. Производителю об этом сообщили. Пока идёт согласование по возможному устранению неисправности. При поступлении в ремонт лобзика с данной неисправностью, будет выписан акт на замену.
Также при диагностике в некоторых лобзиках не удалось установить в пилкодержатель пилку Bosch T 101D с толщиной хвостовика 1,49мм. При выявлении такой неисправности необходимо менять шток.
Все перечисленные случаи относятся к гарантийным. Открыть в новой вкладке
|
Редуктор. Треск в редукторе, отсутствует вращение (шуруповерт) Развернуть ▼
|
На шуруповёрте имеется шкала, с помощью которой можно регулировать непосредственную силу вращения. Поворачивая регулятор, вы выбираете нужный вам режим. Этим же регулятором можно выбрать режим сверления.
Есть несколько правил, которые позволяют значительно продлить срок службы устройства.
1.Избегать сверления шуруповертом твёрдые, бетонные и каменные поверхности, прилагая чрезмерное усилие (для этого есть другие устройства)
2.Не переключать регулятор во время работы шуруповерта
3.После переключения скорости необходимо убедиться что шестерни-сателлиты зашли плотно в зацепление, включив шуруповерт без нагрузки.
Частым повреждением является износ блокировочных зубьев на подвижной шестерне переключения скоростей. На рис.1 пример такого повреждения. При не полностью включенном переключателе (спешка, неаккуратность, невнимательность) происходит проскальзывание зубьев. При неоднократном проскальзывании получается износ зубьев шестерни (Рис.2) - редуктор разрезан для наглядности. В дальнейшем, даже при незначительной нагрузке, редуктор начинает трещать и устройство становится не пригодным для эксплуатации.
Такие повреждения носят эксплуатационный характер и являются результатом либо неаккуратного, либо интенсивного использования инструмента и гарантийным случаем не являются.
В пластиковом исполнении блокировочных зубьев, повреждение происходит на ответной части (Рис.3). Открыть в новой вкладке
|
Карбюратор настройка (2-х тактные двигатели) Развернуть ▼
|
Существует несколько вариантов исполнения безпоплавковых карбюраторов. Некоторые модели карбюраторов, в целях удешевления товара, исполнены в нерегулируемом варианте. Такие карбюраторы, в случаях каких-нибудь неисправностей, просто меняются на новый. В нашей статье мы рассмотрим карбюратор, который поддается полной регулировке как по качеству смеси, по ее количеству, так и по режиму холостого хода (ХХ).
Такие карбюраторы имеют три регулировочных винта. Винт качества смеси (Рис.1_А), обозначается буквой "L". Он расположен всегда ближе к цилиндру. Винт количества смеси (Рис.1_В) или винт максимальных оборотов, обозначается буквой "H". И винт регулировки холостого хода (Рис.1_С). На Рис.1_D - условно обозначен главный жиклер.
В первую очередь необходимо настроить качество смеси. Идеальным соотношением воздуха к топливу (по весу) 14,7/1 (14,7кг воздуха к 1кг топлива). Такое соотношение называют стехиометрической. При таком соотношении коэффициент избытка воздуха равен единице (обозначается буквой лямбда), т.е. лямбда равна единице.
Если вращать винт в сторону откручивания, то этим самым мы, добавляя топливо, обогащаем смесь и лямбда становится меньше единицы (лямбда - соотношение воздуха к топливу, а не наоборот). На Рис.2_GIF понятна закономерность обогащения смеси и реакция двигателя.
Вращение винта в обратную сторону приводит к противоположному результату (Рис.3_GIF). Смесь обедняется и коэффициент избытка воздуха (лямбда) становится больше (много воздуха - мало топлива).
В обоих случаях обороты двигателя падают. Наша задача добиться максимальных оборотов двигателя, найдя такое положение винта качества смеси, при котором это требование будет выполняться (Рис.4_GIF).
После того как мы выставили максимальные обороты двигателя, винтом холостого хода (подпирает дроссельную заслонку, может обозначаться LD) (Рис.1_С) добиваемся такого положения при котором обороты двигателя будут на 300 об/мин больше нормальных оборотов холостого хода. В нашем случае ХХ 2800 об/мин. Мы докручиваем до 3100 об/мин (Рис.5_GIF).
Возвращаемся к винту качества смеси "L" (Рис.1_А) и вращаем в сторону ОТКРУЧИВАНИЯ (встречаются карбюраторы с левой резьбой). При этом обороты начнут падать. Доводим обороты двигателя до нужных нам 2800 об/мин (Рис.6_GIF).
Завершаем настройку карбюратора винтом количества смеси "Н" (Рис.1_В). Выжимаем полный газ и по тахометру выставляем необходимое количество максимальных оборотов.
Если ориентироваться "на слух", то придется ориентироваться по реакции двигателя. Если при резком нажатии на газ происходит провал (двигатель как бы "душится"), то это означает обеднение топлива в переходный момент (винтом "Н" добавить, открутить). Если максимальные обороты недостаточны, двигатель не набирает нужные обороты - смесь богатая. Винт "Н" закрутить для уменьшения подачи топлива. Открыть в новой вкладке
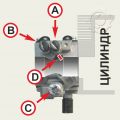 Рис.1 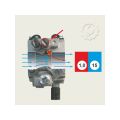 Рис.1_GIF 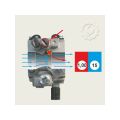 Рис.2_GIF 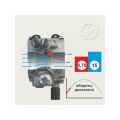 Рис.3_GIF 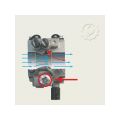 Рис.4_GIF 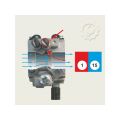 Рис.5_GIF
|
Выдвижение штока (погружной вибрационный насос) Развернуть ▼
|
В погружных насосах иногда происходит такое явление как выдвижение штока. Насос в результате перестает работать. Основные узлы насоса на Рис.1. Более детально можно рассмотреть на Рис.2
Насос относится к устройствам вибрационного типа. Принцип работы основан на периодическом примагничивании якоря к катушке с частотой, обусловленной нашей сетью, т.е. 50 Гц (Рис.5).
На Рис.3_А цикл всасывания, Рис.3_В режим прокачивания воды из насоса.
Якорь напрессован на шток (Рис.2) и удерживается двумя контргайками(Рис.5_А) через шайбы (Рис.4_B). Конструкция насосного механизма на Рис.6.
При ударах якоря о катушку статора, вся нагрузка приходится на резьбовое соединение двух гаек и штока. При ослаблении гаек (Рис.7_А), от вибрации, шток по инерции может выдвинуться вниз (Рис.7_В) и работа насоса при этом прекратится. Ремонт в таком случае сводится к тому, что достаточно вернуть шток на место и затянуть гайки. Гайки обязательно посадить на фиксирующий резьбовой состав.
В случаях когда сорвана резьба - меняется шток и гайки на новые. Открыть в новой вкладке
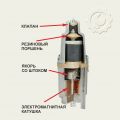 Рис.1 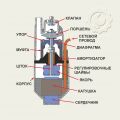 Рис.2 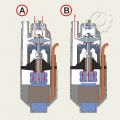 Рис.3 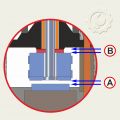 Рис.4 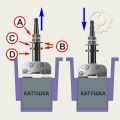 Рис.5 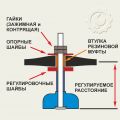 Рис.6 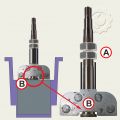 Рис.7
|
Обслуживание теплогенератора Развернуть ▼
|
Принцип работы дизельных теплогенераторов (Рис.1) везде имеет схожую схему. Топливо из бака (Рис.2_1) поступает через топливный фильтр (Рис.2_2) в насос (Рис.2_3) и под давлением подается дальше по магистрали (Рис.2_4). В магистраль высокого давления включены электромагнитный клапан (Рис.2_5) и распыляющая форсунка (Рис.2_6). Искра для поджига топлива создается модулем высокого напряжения (Рис.2_7) и подается на электроды (Рис.2_8). Излишки топлива сбрасываются насосом обратно в бак (Рис.2_9).
Топливные насосы бывают роторного и шестеренного типа и между собой также имеют схожие схемы. Нагнетающей системой в насосах шестеренного типа являются эксцентриковая шестерня и ответная рабочая камера (Рис.3_1). Снаружи насос имеет входной канал (Рис.4_1), выходной канал (Рис.4_2), канал сброса избытка топлива, "обратка" (Рис.4_3). Так же имеется выход на манометр для проверки давления (Рис.4_4), закрыт заглушкой. Давление регулируется винтом (Рис.4_5). Сверху корпуса фильтр тонкой очистки (Рис.5_1) под заглушкой (Рис.5_2).
Первичный топливный фильтр состоит из колбы отстойника (Рис.6_1), фильтрующего элемента (Рис.6_2) и самого корпуса (Рис.6_3). Топливо засасывается в колбу (Рис.6_4), далее через фильтр поступает на вход насоса (Рис.6_5).
Самым последним барьером для нежелательных примесей в топливе является узел форсунки (Рис.7_1). В форсунку ввернут фильтрующий элемент (Рис.7_2) который выполнен из мелких спрессованных шариков.
Теперь о правилах обслуживания теплогенератора и поддержке его в рабочем состоянии:
- чистить первичный топливный фильтр руководствуясь визуальным осмотром на отсутствие мусора в колбе (Рис.6_1), при необходимости заменить фильтрующий элемент (Рис.6_2)
- после каждых 300 часов эксплуатации очистить топливный фильтр насоса (Рис.5_1), осмотреть форсунку, ее фильтрующий элемент (Рис.7_2) и при необходимости (Рис.7_3) заменить.
Можно попытаться очистить фильтр форсунки используя средство для очистки карбюраторов или ацетон. Для этого следует поместить фильтр в промывочное средство на несколько часов и затем продуть сжатым воздухом. Но из практики следует отметить, что подобными процедурами редко удается достичь хорошего результата. Как правило меняется форсунка целиком.
- через каждые 500 часов промыть топливный бак чистым дизельным топливом (нельзя использовать для промывки воду). Сливное отверстие находится внизу бака под заглушкой (Рис.8)
- дважды в сезон очистить вентилятор и камеру сгорания сжатым воздухом, сняв верхнюю крышку
- раз в сезон проверить зазор между электродами, целостность трансформатора и высоковольтных проводов, надежность крепежных соединений, целостность электрических контактов и клемм.
Соблюдение этих простых правил позволит значительно увеличить срок службы теплогенератора.
И последнее что хотелось бы отметить. Винт регулировки давления насоса (Рис.4_5) настраивается в сервисном центре на определенное давление, которое оговорено инструкцией для данной модели теплогенератора. Нельзя его использовать как винт для увеличения или уменьшения получаемого тепла. Это часто приводит к нарушению нормальной работы устройства и возможному выходу его из строя. Для исключения соблазна покрутить винт, рекомендуется в сервисном центре установить какую-нибудь пломбу-заглушку (Рис.9), можно просто капнуть герметиком. Открыть в новой вкладке
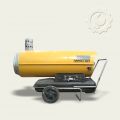 Рис.1 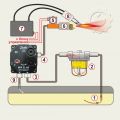 Рис.2 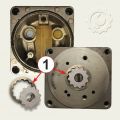 Рис.3 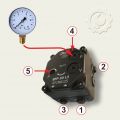 Рис.4 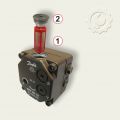 Рис.5 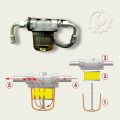 Рис.6 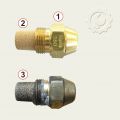 Рис.7 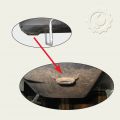 Рис.8 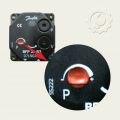 Рис.9
|
LG-634_задир ЦПГ (только в моделях 2022 г.в. с поролоновым фильтром) Развернуть ▼
|
В модели газонокосилок ECO LG-634 обнаружен неприятный момент с конструктивным дефектом воздушного фильтра (Рис.1). Внешний вид фильтрующего узла на Рис.2.
Под крышкой, внутри корпуса фильтра, находится 3 поролоновые пластинки (Рис.3). Две из них стоят на пути всасывания воздуха (Рис.4_А), одна непосредственно перед карбюратором (Рис.4_В). Пластины поролона лежат в предусмотренных нишах корпуса фильтра и разделены перегородками. Воздух, поступая снизу, проходит через 2 крайних поролоновых фильтра (Рис.5_А). Далее, огибая перемычки, поступает через центральный паролоновый фильтр в карбюратор и далее в камеру сгорания двигателя (Рис5_В).
В результате того, что пластины имеют меньший чем нужно размер, в процессе эксплуатации они деформируются и перестают плотно прилегать к краям перегородок. При частичном засорении фильтра такое происходит намного быстрее, т.к. сопротивление потоку увеличивается и воздух ищет более легкие пути. Этим путем становится образовавшаяся щель (Рис.6). Так же бывали случаи несоответствия размеров фильтров с самим корпусом. Они были короче нужных размеров, где так же образовывалась щель между корпусом и фильтром.
В этом случае воздух уже проходит не через фильтр, а мимо него (Рис.7_А) и беспрепятственно, вместе с абразивной пылью, поступает в цилиндр двигателя (Рис.7_В).
Результат можно увидеть на Рис.8. Грязь в полости карбюратора (Рис.8_А) и абразивный износ цилиндра двигателя (Рис.8_В).
В большинстве случаев это признается как гарантия, за исключением случаев, когда на устройстве есть следы эксплуатации в пыльной среде. Открыть в новой вкладке
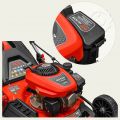 Рис.1 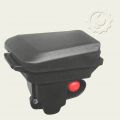 Рис.2 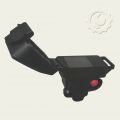 Рис.3 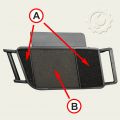 Рис.4 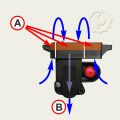 Рис.5 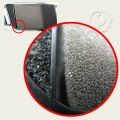 Рис.6 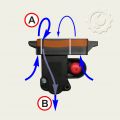 Рис.7 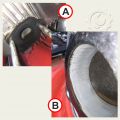 Рис.8
|
Клапана, большой зазор и в чем опасность Развернуть ▼
|
Общая работа клапанного механизма на Рис.1_GIF. Нас интересует место взаимодействия клапана с рычагом механизма газораспределения (Рис.2).
Для наглядности на Рис.3 удалена возвратная пружина клапанной тарелки. На схеме рычаг (Рис.3_1), хвостовик клапана (Рис.3_2) и клапанная тарелка (Рис.3_3). Клапанная тарелка, через возвратную пружину, обеспечивает прижатие клапана к седлу в цилиндре, закрывая каналы впуска-выпуска. При работе хвостовик клапана опирается на рычаг, который и управляет клапаном. Между клапаном и рычагом должен быть температурный зазор, который составляет в большинстве случаев 0,15 - 0,2 мм.
При эксплуатации происходит износ узлов хвостовика клапана (Рис.4_1), клапанной тарелки (Рис.5_1) и контактного места на рычаге. Клапанная тарелка вырабатывается в месте контакта с клапаном (Рис.6). При больших износах этих узлов (Рис.7_1) появляется такой момент при котором хвостовик клапана уже не достает до рычага и рычаг начинает опираться о тарелку (Рис.7_2). Результат такого касания на Рис.8 где виден износ контактной площадки рычага. Синим овалом обозначена контактная площадка такой, какой она должна быть изначально (Рис.8_красная стрелка).
Что происходит в этом случае и чем это опасно? Рычаг опираясь на тарелку отжимает возвратную пружину и освобождает клапан. Клапан выпадает из зацепления тарелки и отправляется в "свободное путешествие" (Рис.9_GIF). Часто это заканчивается встречей с поршнем, повреждая его вплоть до пробивания насквозь.
Из выше сказанного вывод - игнорирование такого состояния клапанов может обернуться большими проблемами с двигателем. Открыть в новой вкладке
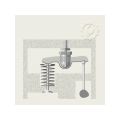 Рис.1_GIF 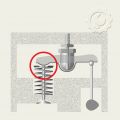 Рис.2 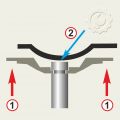 Рис.3 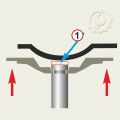 Рис.4 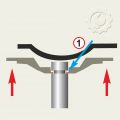 Рис.5 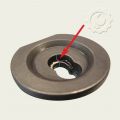 Рис.6  Рис.7 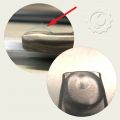 Рис.8 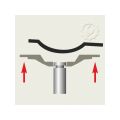 Рис.9_GIF
|
Принцип работы перфоратора, про отверстия в цилиндре (часть 2) Развернуть ▼
|
В некоторых поршнях цилиндрического типа имеются отверстия (Рис.1). Это характерно для перфораторов с качающимся подшипником, где электродвигатель расположен по одной оси со стволом. Аналогичные отверстия есть и в перфораторах с шатунно-кривошипным механизмом. Там они расположены в самом стволе. Для чего нужны эти отверстия?
Отверстие (Рис.2_В) предназначено для дросселирования полости воздуха между поршнем и тараном (Рис.2_А). При отсутствии такого отверстия таран не смог бы перемещаться по цилиндру и не выполнял бы своих функций по обеспечению удара (Рис.3_GIF).
Второе отверстие (Рис.4_В) необходимо для того, что бы при отсутствии насадки (бура) не было бесконтрольного перемещения тарана по цилиндру. Без нагрузки такое перемещение может вызвать сильные ударные моменты на переднюю часть ствола. При нормальной работе вся ударная нагрузка от тарана приходится на ударник или боек, который в свою очередь опирается на бур. При отсутствии насадки ударник будет утоплен в переднюю часть ствола и вся ударная нагрузка будет приходиться на узлы ствола, которые не предназначены для этого.
Отверстие (Рис.4_В) соединяет воздушную полость цилиндра (Рис.4_А) с атмосферой. При отсутствии насадки боек будет перемещен в переднюю часть ствола, а таран "запаркуется" в конечном цикле своего перемещения. При работающем перфораторе воздух будет свободно засасываться и также выходить из цилиндра не перемещая таран (Рис.5_GIF). Для удержания тарана на месте предусмотрена проточка в передней его части, которая прихватывается резиновым кольцом.
Для приведения ударного механизма в рабочее положение достаточно установить бур и надавить на него. Этим самым мы вытолкнем таран из "парковки" и он, перекрыв дроссельное отверстие, подхватится поршнем (Рис.6_GIF). И дальше уже будет происходить работа в штатном режиме (Рис.7_GIF). Таран не проваливается так как постоянно ударяется о боек.
Как только мы снимем оснастку таран дойдет до крайнего переднего положения и прихватится резиновым кольцом. Дроссельное отверстие не позволит тарану сняться с "парковки" (Рис.8_GIF). Открыть в новой вкладке
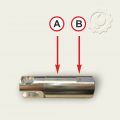 Рис.1 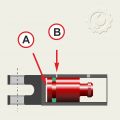 Рис.2 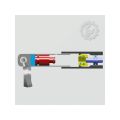 Рис.3_GIF 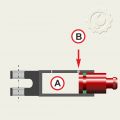 Рис.4 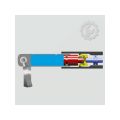 Рис.5_GIF 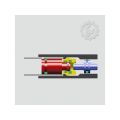 Рис.6_GIF 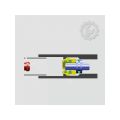 Рис.7_GIF 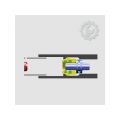 Рис.8_GIF
|
Принцип работы перфоратора (часть 1) Развернуть ▼
|
Большинство перфораторов имеют основные сходные по назначению узлы. Рассмотрим работу узлов в перфораторе с кривошипно-шатунным механизмом. Ударный механизм состоит из бойка или ударника (Рис.1,1), тарана (Рис.1,2) и поршня (Рис.1,3). Во всех этих узлах имеются уплотнительные кольца. Благодаря им создаются две независимые воздушные полости. Одна между ударником и тараном. Вторая между тараном и поршнем.
В статичном положении давление в обоих полостях одинаковое (Рис.1,А). При вращении приводной шестерни поршень начинает смещаться назад, создавая между собой и тараном полость с пониженным давлением (Рис.1,В). Уплотнение и масса тарана несколько придерживает его от перемещения. И когда давление понизится достаточно для преодоления сопротивления уплотнителя, таран рывком перемещается в сторону поршня (Рис.1,С), который к тому времени уже начинает двигаться навстречу. Давление в полости таран-поршень повышается, замедляя ход тарана. На встречном движении получается максимальное давление в этой полости и таран начинает двигаться в одном направлении с поршнем (Рис.2,А). Какое-то время они двигаются синхронно, но затем таран начинает двигаться быстрее поршня. На него действует поступательная сила поршня и давление между ними. В конце своего движения таран бьет по ударнику (Рис.2,В). Сила удара передается дальше через ударник к буру (Рис.2,С). Возвращаясь назад поршень потянет за собой таран. Цикл повториться (Рис.1,В). Следует добавить что таран, перемещаясь к поршню, за собой так же оставляет зону пониженного давления между собой и ударником (Рис.1,С), позволяя ударнику вернуться в исходное состояние. Проще понять принцип работы можно в динамике движения этих узлов, где изменение цвета в полостях показывает уплотнение воздуха (Рис.3_GIF).
В перфораторах, в которых применяется качающийся подшипник в качестве узла ударного механизма, принцип тот же самый. Здесь качающийся подшипник (Рис.4_1) выполняет ту же задачу что и кривошипно-шатунный узел. При вращении ведущего вала качающийся подшипник своим рычагом, связанным с внешней обоймой, приводит в поступательное движение поршень (Рис.4_2). В таких типах перфораторов поршень выполнен в форме глухого цилиндра, в котором перемещается таран (Рис.4_3). Таран толкает боек (Рис.4_4), а тот в свою очередь бур (Рис.4_5).
Механизм действия тут такой. Поршень совершает возвратно-поступательные движения, внутри которого находится таран. Если бы не было уплотнения, то имея некоторую массу таран находился бы в статичном состоянии (Рис.5_GIF). С уплотнением таран отделяет воздушную полость в глухой части поршня-цилиндра. И теперь таран уже не может находится в статичном состоянии, он вынужден перемещаться вместе с поршнем, а воздух играет роль пружины, как было описано в начальной части статьи (Рис.6_GIF). Общий механизм работы перфоратора на (Рис.7_GIF).
Из всего сказанного можно сделать определенный вывод. Для хорошего удара необходимы новые уплотнения и идеальная внутренняя поверхность цилиндров по которым двигаются узлы с этими уплотнениями. Особое внимание следует уделить смазке узла поршень-таран. Смазка должна быть достаточно жидкая, что бы не блокировать таран и достаточно вязкой, что бы сохраняться на стенках узлов. Густая смазка может блокировать дроссельные отверстия и таран "зависнет" в цилиндре поршня (Рис.8_GIF). Открыть в новой вкладке
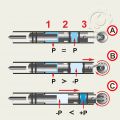 Рис.1 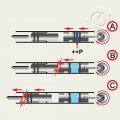 Рис.2 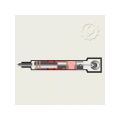 Рис.3_GIF 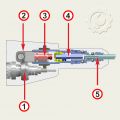 Рис.4 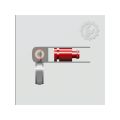 Рис.5_GIF 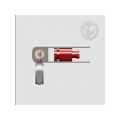 Рис.6_GIF 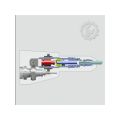 Рис.7_GIF 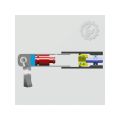 Рис.8_GIF
|
Стартер, вырывает из рук (двигатели 4-х тактные) Развернуть ▼
|
Во многих 4-х тактных двигателях, для облегчения запуска, применяется центробежный декомпрессор.
Работает это следующим образом. В статичном состоянии клапан, через толкатель, подпирается механизмом декомпрессора. Клапан двигателя при этом находится в приоткрытом состоянии, снижая компрессию двигателя. Как только мы начинаем вращать стартерной рукояткой двигатель, центробежный механизм отходит в сторону, смещая при этом упор под клапаном. Клапан возвращается в нормальное положение и двигатель работает в штатном режиме. На Рис.1_GIF видно как центробежный механизм, смещаясь по синей стрелке, перемещает поводок подпора клапана (Рис.1_GIF, красный цвет).
Это же самое мы можем посмотреть в другом ракурсе (Рис.2_GIF). Подпор клапана, под действием центробежного механизма (Рис.2_GIF,1), смещается (Рис.2_GIF,2) освобождая клапан. Клапан возвращается в штатное положение (Рис.2_GIF,3).
При повреждении подпора клапана (Рис.3 )пропадает декомпрессия двигателя. В результате при попытке завести такой двигатель стартерную рукоятку просто вырывает из рук. Рис.4_1 - зона прилегания клапанного толкателя, Рис.4_2 - повреждение.
В таких ситуациях меняется распредвал на новый. Открыть в новой вкладке
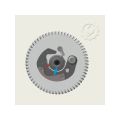 Рис.1_GIF 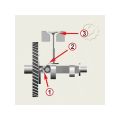 Рис.2_GIF 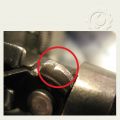 Рис.3 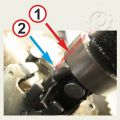 Рис.4
|
Гайковерт пневматический (принцип работы) Развернуть ▼
|
Для надежной работы пневмоинструмента необходимо соблюдать некоторые правила. После компрессора (Рис.1-1) должен стоять влагоотделитель (Рис.1-2) или более простой (Рис.1-2а). Далее между влагоотделителем и гайковертом должен стоять лубрикатор (Рис.1-3).
Пневматический гайковерт (Рис.2) и его внутреннее устройство (Рис.3). Воздух под давлением раскручивает ротор через лопатки, который передает вращение на дальнейшие узлы. Ударный механизм гайковерта (Рис.4) состоит из 6-ти основных узлов, рамка, 2 молотка, 2 штифта и упорный вал. Молотки имеют особую конструкцию (Рис.5). Относительно одного штифта (Рис.5-А) молоток смещаться в сторону не может, а относительно второго (Рис.5-В) может перемещаться в некоторых пределах (указано стрелками).
Принцип действия следующий (Рис.6). Вращение от ротора передается на рамку. В рамку вставлены штифты которые, в свою очередь, вращают молотки. Молотки имеют выступы и на валу также имеются соответствующие выступы. Войдя в зацепление друг с другом (Рис.6-А) вращение передается дальше на вал (Рис.6-В). Если гайка/болт не поддаются вращению (Рис.7), то вал останавливается, а молоток соскакивает с выступа вала (Рис.7-А) и продолжает дальнейшее вращение (Рис.7-В) Следующий выступ, ударяясь о выступ вала, возвращает молоток в исходное положение. При дальнейшем вращении выступ молотка встречается с выступом вала и происходит удар (Рис.7-С). Если болт/гайка не поддались откручиванию цикл повторяется с позиции (Рис.7-А). Реверсивное вращение обеспечивается перенаправлением воздуха переключающим золотником.
Наглядно работу ударного механизма можно понять по Рис.8_GIF. Открыть в новой вкладке
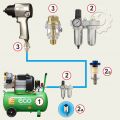 Рис.1 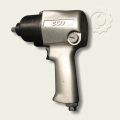 Рис.2 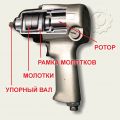 Рис.3 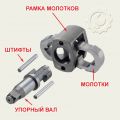 Рис.4 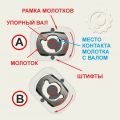 Рис.5 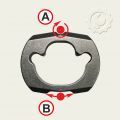 Рис.6 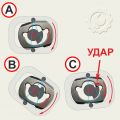 Рис.7 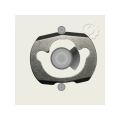 Рис.8_GIF
|
Цепи, заточка (цепные пилы) Развернуть ▼
|
Эта статья для тех у кого-то возникнет необходимость правильно либо заточить цепь, либо объяснить клиенту как грамотно это сделать. Если подобная задача стоит в условиях сервисного центра и заточки цепей носят не единичный характер, то лучший вариант это приобретение заточного станка (Рис.1).
Заточка цепи не совсем простая задача. Здесь надо учитывать одновременно несколько углов положения заточного инструмента, а заточка разно направленных зубьев должна быть произведена под одинаковыми углами. В противном случае цепь постоянно будет уходить в сторону, а шина изнашиваться неравномерно.
Для заточки лезвия режущего зуба понадобится специальный круглый напильник (Рис.2). Эти напильники разделяются по размерам. Диаметр напильника напрямую зависит от шага цепи.
• Шаг 1/4″ – диаметр 4,0 мм;
• Шаг 0,325″ — 4,8 мм;
• Шаг 3/8″ — 5,2 мм;
• Шаг 0,404″ — 5,5 мм.
Выше было сказано о не совсем простой задаче при заточке и вот в чем она заключается. Цепь, во время заточки при помощи напильника, должна быть натянута. Затачиваемый зуб, должен располагаться примерно посредине шины, это необходимо для удобства проведения работ. В процессе заточки нужно продвигать цепь по шине, не забывая при этом каждый раз устанавливать тормоз в рабочее положение. Напильник следует держать перпендикулярно вертикальной плоскости шины под углом 90 градусов (Рис.3) и одновременно выдерживать угол в 30 градусов относительно перпендикулярной линии к линии шины (Рис.4_А). В большинстве своем на режущем зубе имеется сервисная метка. Она указывает направление заточки и предел до которого можно точить цепь (Рис.5). Заточка цепи производится движениями напильника изнутри зуба наружу.
Значительно упростить задачу помогут несложные приспособления. Для правильного угла заточки используют специальные шаблоны (Рис.6). Пример использования на Рис.7_А. Шину необходимо лишить ненужной подвижности. Для этого можно воспользоваться способом с подкладыванием между цепью и шиной штатного свечного ключа (Рис.7_В), либо воспользоваться струбциной (Рис.8).
Стачиваясь зуб как бы уходит виз. Это обусловлено конструкцией режущего зуба, задняя часть режущей полки ниже режущей ее части. Соответственно количество захватываемой древесины уменьшается, что существенно сказывается на производительности. За глубину реза отвечает ограничительный зуб (Рис.9). После заточки режущей части необходимо подточить и ограничительный зуб. Он должен быть утоплен на 0,65 мм. Для этого может пригодиться еще один шаблон (Рис.10) и плоский напильник (Рис.11). Приложив шаблон на цепь можно заметить выступающий ограничитель (Рис.12). Плоским напильником его следует спилить вровень с шаблоном (Рис.13).
(!!!) Работу по заточке цепи, нужно обязательно проводить с использованием перчаток из грубого материала. В противном случае можно достаточно легко себя травмировать, т.к. рабочая поверхность зубьев очень острая.
Углы заточки цепей подробно оговорены в предыдущей статье "Углы заточки пильных цепей", https://remont.tools.by/diagnostics/view/1652518345 Открыть в новой вкладке
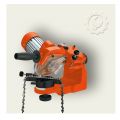 Рис.1 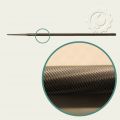 Рис.2 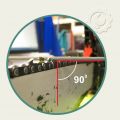 Рис.3 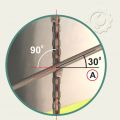 Рис.4 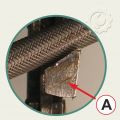 Рис.5 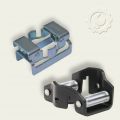 Рис.6 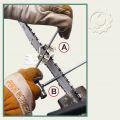 Рис.7 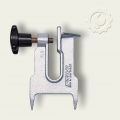 Рис.8 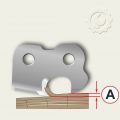 Рис.9 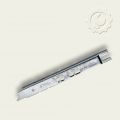 Рис.10 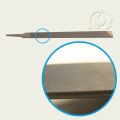 Рис.11 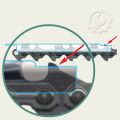 Рис.12 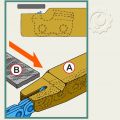 Рис.13
|
ECOTERM давление насоса, производительность форсунки (таблица) Развернуть ▼
|
* DHD-201W - 0,31bar - 2,00 л/ч
* DHD-301W - 0,31bar - 2,80 л/ч
* DHD-20W - 0,32bar - 2,00 л/ч
* DHD-501W - 0,38bar - 4,70 л/ч
* DHD-200 - 0,30bar - 1,58 л/ч
* DHD-300 - 0,34bar - 2,13 л/ч
* DHD-500 - 0,40bar - 3,40 л/ч
* DHI-30W - 10,0bar - 2,28 л/ч (после замены 9,0 bar_1,9 л/ч)
* DHI-50W - 10,0bar - 4,70 л/ч
* DHI-520W - 9,5 bar - 3,00 л/ч
Примечание:________________________________________________________
* DHI-30W - в этой модели необходима замена форсунки вместо штатной (0,6gal_60град.) установить (0,5gal_80град.)
** МАРКИРОВКА ФОРСУНОК
___ Производительность форсунки может обозначаться в галлонах США (USgal)-(Рис.1_А) или кг/час.-(Рис.1_В). Иногда может присутствовать оба обозначения.
___ Угол распыления факела обозначается в градусах (Рис.1_С). Это может быть 60 либо 80 градусов (Рис.2). Открыть в новой вкладке
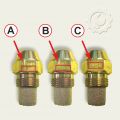 Рис.1 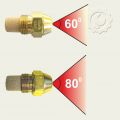 Рис.2
|
Редуктор, пробуксовка ( культиватор FM-1617MXL) Развернуть ▼
|
Такая неисправность как проскальзывание редуктора привода колес под нагрузкой объясняется износом или частичным повреждением зубчатой пары самого редуктора. В данном типе редукторов для передачи вращения используется коническая пара (Рис.1). Редуктор состоит из корпуса редуктора (Рис.2_1), ведущего вала (Рис.2_2) с конической шестерней (Рис.2_3). Ведомый вал (Рис.2_4) с коническим роликовым подшипником (Рис.2_5) входит в подшипник корпуса редуктора (Рис.2_6). На сам ведомый вал насажена коническая шестерня (Рис.2_7) и прижимная втулка (Рис.2_8). Весь этот механизм фиксируется крышкой редуктора (Рис.2_9) в которой находится внешняя обойма конического подшипника (Рис.2_5). Шестерня (Рис.2_7) при этом должна быть зафиксирована без осевого люфта. При этом должен соблюдаться температурный зазор между шестернями (Рис.2_7) и (Рис.2_3). Для обеспечения этого зазора используется регулировочная шайба (Рис.2_10), установленная на заводе. Часто случается так, что либо не выдержан необходимый зазор, либо присутствует осевой люфт шестерни (Рис.2_7). В обоих случаях появляется недопустимо большой зазор между шестернями (Рис.3), что неизменно приводит к повреждению зубчатой передачи (Рис.4). Наша задача состоит в том, что бы обеспечить правильный зазор путем подкладывания регулировочных шайб нужного размера. Увеличивая размер шайбы под шестерней (Рис.5_А) и уменьшая соответственно размер шайбы между шестерней и втулкой (Рис.5_В) мы уменьшаем зазор между шестернями. Устанавливая шайбы в обратном порядке (Рис.6) мы увеличиваем зазор между шестернями. Суть операции сводится к тому что бы ликвидировать осевое перемещение большой шестерни (Рис.2_7) и обеспечить необходимый зазор в зубчатой паре. В собранном редукторе, при вращении вала от руки, должен присутствовать небольшой люфт по оси вращения вала. Открыть в новой вкладке
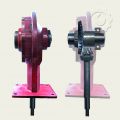 Рис.1 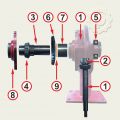 Рис.2 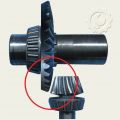 Рис.3 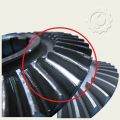 Рис.4 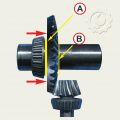 Рис.5 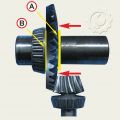 Рис.6
|
ЦПГ, абразивный износ (4-х тактный двигатель) Развернуть ▼
|
Абразивный износ поршневой группы происходит исключительно по причине попадания пыли в двигатель. Что бы этого не произошло установлен воздушный фильтр (Рис.1). Воздух, пройдя через фильтр, попадает в нижнюю часть корпуса фильтра и далее через карбюратор в камеру сгорания двигателя.
Узел воздушного фильтра (Рис.2) состоит из верхней крышки (Рис.2_А), фильтрующего элемента (Рис.2_В), нижней пластины крышки (Рис.2_С), уплотнительного кольца (Рис.2_D) и нижней части корпуса фильтра (Рис.2_Е). В нижней части корпуса фильтра (Рис.3) находится герметичная полость (синяя на рисунке) и имеет сообщение только с фильтрующим элементом и карбюратором. Эта полость образована двумя деталями, верхней и нижней и между собой плотно соединены. Были случаи когда это соединение было неплотным даже у новых устройств (Рис.4). Через эту щель воздух с абразивом попадает, минуя фильтр, прямо в двигатель. В результате грязь в карбюраторе (Рис.5) и появившиеся повреждения поршневой группы в виде задиров цилиндра и поршня и износ кулачка распредвала (Рис.6).
Устранить эту неисправность можно монтажным клеем, распределив его в углублении (Рис.7) в месте соединения двух половинок нижней части корпуса фильтра. Мы использовали монтажный клей типа "жидкие гвозди" (Рис.8).
Далее есть еще одно место, нуждающееся в хорошем уплотнении. Это примыкание фильтрующего элемента (Рис.2_В) к нижней части корпуса фильтра (Рис.2_Е). Между ними находится нижняя пластина крышки фильтра (Рис.2_С). Уплотнение обеспечивает резиновое кольцо (Рис.2_D). Все дело в том, что нижняя пластина не должна быть толще или равной по толщине с уплотнительным кольцом, иначе не возникнет плотного обжатия. По этому меняем тонкое резиновое кольцо на более подходящее толстое (Рис.9). Фильтрующий элемент (Рис.10_А) должен опираться на уплотнительное кольцо (Рис.10_В), но никак не на пластиковую пластину (Рис.10_С).
Отдельно стоит отметить, что необходимо убедиться в исправности прокладки карбюратора и плотной посадке газоотводящей трубки. Газоотводящая трубка соединена с корпусом фильтра и газ из двигателя возвращается обратно в двигатель через карбюратор, но минуя сам фильтрующий элемент. Открыть в новой вкладке
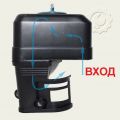 Рис.1 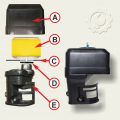 Рис.2 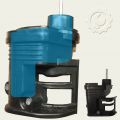 Рис.3 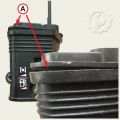 Рис.4 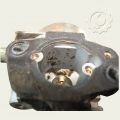 Рис.5 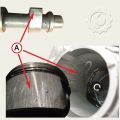 Рис.6 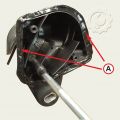 Рис.7 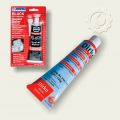 Рис.8 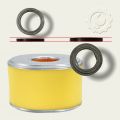 Рис.9 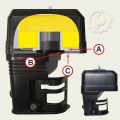 Рис.10
|
Подшипники аналоги (ГОСТ - международная система) Развернуть ▼
|
В последнее время мы привыкли к международной системе обозначений подшипников, но иногда встречаются обозначения по ГОСТу (отечественные подшипники). Здесь приведена таблица наиболее встречающихся в использовании у нас подшипников однорядных шариковых радиальных с обозначением по ГОСТу и их аналогов по международной маркировке. Нас интересуют в первую очередь сравнительные обозначения и основные размеры: наружный диаметр (Рис.1_D,Рис.4_D), внутренний диаметр (Рис.1_d,Рис.4_d) и высота подшипника (Рис.1_B,Рис.4_B).
Вначале оговоримся по маркировке ГОСТ. Подшипники могут быть открытыми, закрытыми с одной стороны и закрытыми с двух сторон защитной крышкой. Крышки могут быть металлические (Рис.1_А) и резинометаллические(Рис.2_А). Резинометаллические крышки лучше сохраняют подшипник то попадания грязи и пыли. Металлические крышки лучше переносят высокие обороты. Для примера возьмем подшипник 608(по международному стандарту), его аналог по ГОСТ (Рис.3). Последние 2 цифры (Рис.3_желтая зона) это основной тип подшипника 22-наружный диаметр_D, 8-внутренний диаметр_d, 7-высота подшипника_B. Под основной тип подшипника зарезервированы 4 последних знака. Пятая цифра сзади (Рис.3_красная зона)- количество защитных крышек, где 6-это одна крышка, 8-подшипник имеет крышки с обеих сторон. Перед 6-кой или 8-кой единица (Рис.3_зеленая зона) говорит о том, что крышки резинометаллические. Отсутствие знака - металлические. Как пример: 180018 (ГОСТ), подшипник типоразмера 22х8х7 защищен с двух сторон крышками из резинометаллического материала или 80018 (ГОСТ) подшипник 22х8х7 с двумя резинометаллическими крышками.
Обозначение защитных крышек по международному стандарту (ISO):
* отсутствие после цифр суффикса - открытый (608)
* Z-одна металлическая крышка (608-Z)
* 2Z-металлические крышки с двух сторон (608-2Z)
* RS- одна резинометаллическая крышка (608-RS)
* 2RS-резинометаллические крышки с двух сторон (608-2RS).
СРАВНИТЕЛЬНАЯ ТАБЛИЦА АНАЛОГОВ
ISO________ГОСТ________D-d-B________max об/мин
6000_______100________26-10-8__________30000
6001_______101________28-12-8__________32000
6002_______102________32-15-9__________28000
6003_______103________35-17-10_________24000
6004_______104________42-20-12_________20000
6005_______105________47-25-12_________18000
6008_______108________68-40-15_________12000
6009_______109________75-45-16_________11000
607_________17________19-7-6___________34000
608_________18________22-8-7___________32000
609_________19________24-9-7___________30000
61804____1000804______32-20-7__________22000
_6804____1000804______32-20-7__________22000
61806____1000806______42-30-7__________18000
_6806____1000806______42-30-7__________18000
6200_______200________30-10-9__________30000
6201_______201________32-12-10_________22000
6202_______202________35-15-11_________19000
6203_______203________40-17-12_________17000
6204_______204________47-20-14_________15000
6205_______205________52-25-15_________12000
6206_______206________62-30-16_________10000
625_________25_________16-5-5__________36000
626_________26_________19-6-6__________32000
627_________27_________22-7-7__________30000
628_________28_________24-8-8__________31000
629_________29_________26-9-8__________26000
6300_______300________35-10-11_________26000
6301_______301________37-12-12_________26000
6302_______302________42-15-13_________20000
6306_______306________72-30-19__________9000
6307_______307________80-35-21__________8500
6308_______308________90-40-23__________7500
6309_______309_______100-45-25__________8000
6900_____1000900______22-10-6__________36000
6902_____1000902______28-15-7__________28000
6905_____1000905______42-25-9__________18000
696______1000096_______15-6-5__________45000
697______1000097_______17-7-5__________43000
698______1000098_______19-8-6__________40000
30303_____7303_________47-17-15_________8500 Открыть в новой вкладке
|
Заклинивание редуктора (WORTEX_рейсмус) Развернуть ▼
|
Нередким явлением бывают случаи заклинивания цепной передачи в приводном механизме рейсмусного станка. Причиной неисправности являются забившиеся опилки в редуктор, которые препятствуют работе инструмента.
Добраться до редуктора несложно. В первую очередь следует ослабить 4 винта крепления верхней крышки (Рис.1). Винты откручиваются шестигранным ключом 5mm. Полностью снимать крышку не обязательно, достаточно ослабить винты крепления с тем, что бы верхняя часть не прижимала боковые крышки станка. Затем демонтируем левую боковую крышку устройства, которая крепится двумя винтами (Рис.2). Винты откручиваются крестообразной отверткой. Снимаем крышку (Рис.3). Под ней мы увидим пластиковый кожух (Рис.4_А). Крепится он двумя винтами внизу (Рис.5). Откручиваем шестигранным ключом 4mm.
Конструктивно пластиковый кожух выполнен в форме короба, который по мнению конструктора должен был защищать приводной механизм от попадания опилок (Рис.6). На практике получается обратный эффект. Опилки находят пути для попадания в редуктор и из-за защитного кожуха там аккумулируются, образуя плотную массу, препятствующую работе приводного механизма.
Сняв кожух мы доберемся до редуктора (Рис.7). Цепь и шестерни смазаны густой смазкой. Опилки, попадая в редуктор, налипают из-за смазки на узлы редуктора и образуют плотную массу (Рис.8). Наша задача очистить редуктор от опилок и смазать узлы смазкой типа Литол-24 (Рис.9).
В целях обслуживания также следует поступить и с правой крышкой, открыв приводной механизм с ремнем (Рис.10). Убедившись в чистоте механизма и целостности ремня (Рис.11), все узлы монтируем обратно.
Отдельно следует отметить один нюанс. При монтаже крышек рекомендуем не устанавливать пластиковый кожух (Рис.4_А). Если сравнивать модель WORTEX ТР-3117 с аналогичными устройствами других известных брендов (Makita, Hitachi, DeWALT), то у них дополнительные защитные кожуха отсутствуют. Опилки, попадая на узлы редуктора в процессе работы, свободно выпадают обратно под действием вращающихся узлов. Часть налипших опилок легко удаляется в процессе ежедневного обслуживания устройства по окончании работ. Открыть в новой вкладке
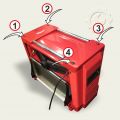 Рис.1 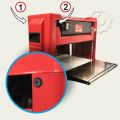 Рис.2 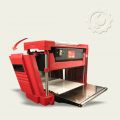 Рис.3 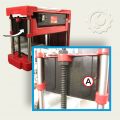 Рис.4 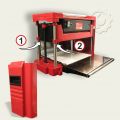 Рис.5 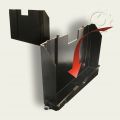 Рис.6 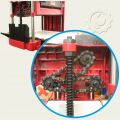 Рис.7 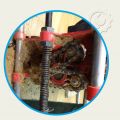 Рис.8 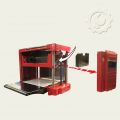 Рис.9 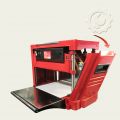 Рис.10 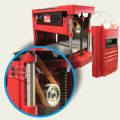 Рис.11
|
Карбюратор диагностика, ремонт Развернуть ▼
|
Статья касается карбюраторов для 2-ух тактных двигателей общего типа (Рис.1), без праймера, самовзвода и пр. дополнений.
Откручиваем винт (Рис.2_А). Сняв крышку, под ней видим прокладку (Рис.2_В) и мембрану клапанов (Рис.2_С). С другой стороны карбюратора откручиваем 4 винта и снимаем крышку (Рис.3_А). Под ней находятся дозирующая игла, жиклеры и мембрана управления иглой. Дозирующая игла приводится в действие целым механизмом, который состоит из коромысла (Рис.4_А), оси (Рис.4_В), самой иглы (Рис.4_С) и фиксирующего винта (Рис.4_D). Под коромыслом находится пружинка, которая через коромысло прижимает иглу к седлу, перекрывая топливный канал.
Открутив винт (Рис.4_D), демонтируем коромысло (Рис.5_А) с осью (Рис.5_В). Убеждаемся в свободном вращении коромысла на оси. При удержании рукой за ось, коромысло должно свободно под своим весом проворачиваться по оси и опускаться вниз.
Затем проверяем свободное перемещение иглы в канале. Взявшись за иглу пинцетом, отпускаем ее в канал (Рис.7). Она так же под своим весом должна беспрепятственно падать вниз. После этих проверок и обратного монтажа механизма дозирующей иглы проверяем уровень относительно коромысла и корпуса карбюратора (Рис.8). Коромысло не должно выступать или глубоко сидеть относительно краев ниши в корпусе. Т.е. быть почти вровень с краями.
В конце, с обратной стороны карбюратора, проверяем фильтрующую сетку (Рис.9). Она должна быть абсолютно чистой. Если устройство побыло в эксплуатации, то лучше ее заменить. Открыть в новой вкладке
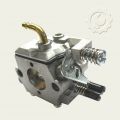 Рис.1 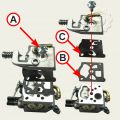 Рис.2 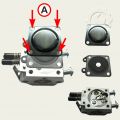 Рис.3 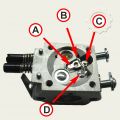 Рис.4 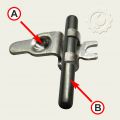 Рис.5 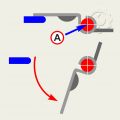 Рис.6 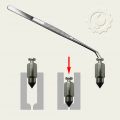 Рис.7 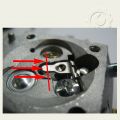 Рис.8 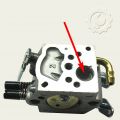 Рис.9
|
Кольца поршневые_завышен размер Развернуть ▼
|
Обнаружилось неприятное явление с ЦПГ для бензопил. Это касается поршневых групп диаметром 45мм. ЦПГ поставляются в сборе и кольца, которые лежат в комплекте, имеют завышенный размер и не входят в цилиндр. Тепловой зазор колец в замке должен быть в районе 0,3мм (Рис.1). Полученная партия ЦПГ, в некоторых случаях, имеет комплектные кольца, которые невозможно установить в цилиндр и становятся с нахлестом (Рис.2). При ремонте следует иметь ввиду этот факт и заранее проверять размерность колец, поместив их в цилиндр. Сделав это до монтажа поршня и цилиндра можно сэкономить кучу рабочего времени и нервов. Открыть в новой вкладке
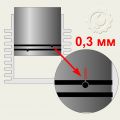 Рис.1 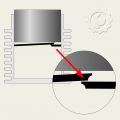 Рис.2
|
|
|
|